1. | Диаметр | 6,3 мм | 7,0 мм | ![]() |
2. | Шаг резьбы (В), мм | 2,40 | 3,00 | |
3. | Диаметр резьбы (D), мм | 6,10 — 6,30 | 6,72 — 7,05 | |
4. | Диаметр тела (d), мм | 4,40 | 4,70 | |
5. | Диаметр наконечника (d2), мм | 4,20 — 4,30 | 4,45 — 4,55 | |
6. | Длина безрезьбового участка (Т), мм | 2,40 — 4,80 | 3,00 — 6,00 | |
7. | Диаметр головки (Р), мм | 9,50 — 10,30 | 9,50 — 10,30 | |
8. | Высота головки (Н), мм | 7,00 — 9,00 | 10,00 — 12,00 | |
9. | Размер под ключ (М), мм | 4,02 — 4,12 | 4,02 — 4,12 | |
10. | Глубина шлица (h), мм | 2,72 — 3,20 | 2,72 — 3,20 |
Приспособление для сверления торцов | Блог Андрея Лаппо
Казалось бы, простая задача – просверлить детали с торца для установки конфирматов или шкантов. Но проблема состоит в том, что их нужно сверлить точно под углом 90. Конечно бывалые мебельщики сверлят всегда вручную, и получается у них это быстро и точно! Но в то же время думаю никого не покидает мысль о том, чтобы как-то упростить и систематизировать этот процесс, особенно когда много деталей. Часто бывает, что приходится доверить процесс сверления кому-то неопытному, и тогда возникает много «косяков» со стыковкой деталей. И тогда задумываешься… был бы какой-нибудь простенький станочек, чтобы показать помощнику без навыков что ему нужно делать, а он бы сверлил не торопясь, и качественно.
Для торцевого сверления существуют различные приспособления, промышленного производства, как стационарные для цеха или гаража, так и мобильные. Их называют сверлильно-присадочными станками. Но всех начинающих мебельщиков и «сам себе мастеров» интересуют бытовые варианты со стоимостью стремящейся к нулю.
Как изготовить такого помощника самостоятельно? Изучая соответствующую тему на форуме мебельщиков мы увидели, что приспособлений для сверления существует наверное столько же, сколько и мебельщиков, каждый считает свое приспособление самым удобным. В принципе это в некоторой степени правильно, ведь каждый делает приспособление под свои задачи и так как ему удобнее.
Рассмотрим опыт форумчан, возможно кому-то из вас понравится определенная идея и облегчит работу.
Первым мы рассмотрим приспособление, предложенное пользователем Babel.
Сам по себе принцип приспособления не нов – в подставке закреплен патрон со сверлом и деталь подается на сверло. Собрано оно из того что было под рукой: кусок столешницы 60х60см, несколько обрезков ДСП, рулетка, саморезы и винты с «барашками». Самая дорогая деталь в приспособлении – небольшая дрель на 400Вт. Дешево и сердито, но свою главную задачу выполняет – упрощает работу и экономит вам время. Для начинающих мебельщиков — просто находка.
Для изготовления приспособления потребуется мощный фрезерный станок, чтобы сделать пазы под направляющую и под линейку. Линейку сделали из рулетки, разрезанной пополам (экономия никому не повредит). Чем больше линейка – тем более универсальной получится конструкция. Для быстрой настройки желательно иметь столешницу около 80см.
Дрель закрепляется между двумя обрезками этой столешницы. Справа скрепляем обрезки винтами, а после этого просверливаем перпендикулярно коронкой на 60мм отверстие. По высоте дрель регулируется подкладыванием снизу кусочков наждачки, так чтобы ось сверла была на расстоянии 8мм от столешницы.
***************************************************************************
Другой вариант приспособления кажется более универсальным, позволяет сверлить детали любой длины, хоть все 2750мм, принцип работы прост – кладем деталь, нажимаем педаль и сверлим. Это уже полуавтоматическая система.
Холостой ход.
Сверление в ЛДСП.
Гофра для отвода опилок из зоны сверления.
Простое устройство педального узла.
Принцип работы и сборки виден на фотографиях и в ролике, выглядит несколько серьезнее, чем первый вариант и, на наш взгляд более удобно, даже отвод для стружки присутствует. Как для начинающих мебельщиков с ограниченным бюджетом тоже вариант отличный, хотя стоит задуматься над более надежным креплением дрели. Аппарат вполне обеспечивает точное сверление под углом 90° на нужную глубину – это его основное предназначение. В педаль можно установить контакт, например от жигулевской педали, для автоматического включения при нажатии и отключения дрели при отпускании педали – это позволит экономить электроэнергию и, самое важное, ресурс инструмента.
***************************************************************************
Третий вариант выглядит уж совсем промышленным, стол с линейкой, изготовленной по принципу форматно-раскроечного станка.
[aslideshow]
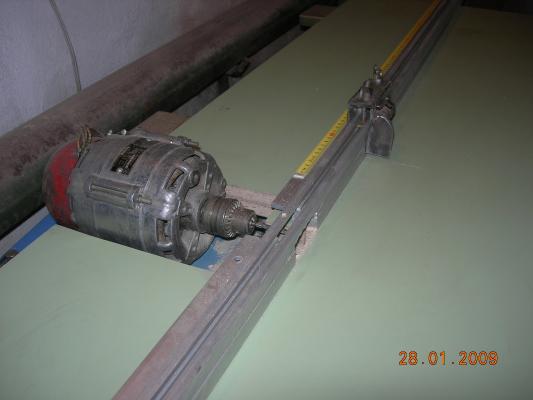

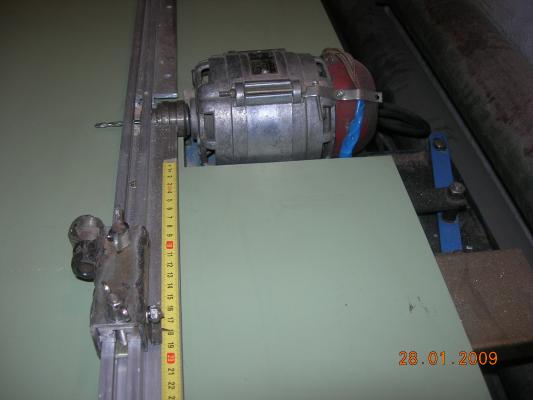
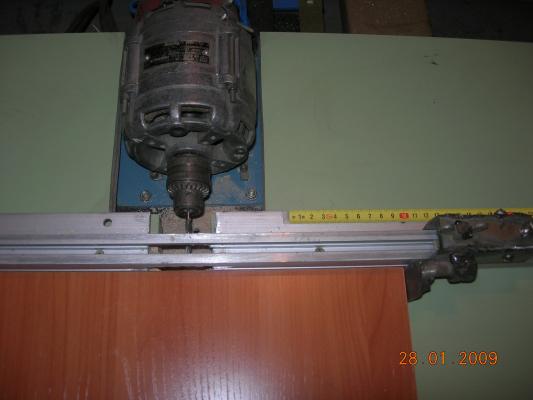
В этом варианте, в отличие от предыдущих, сверло подается на деталь. Двигатель стоит на каретке, взятой от бытового деревообрабатывающего станка. Это как бы все в одном – ставим на каретку двигатель, тянем за рычаг и все проблемы. Для удобства лучше вынести его на передний край стола. Двигатель установлен от стиральной машинки, если работы много лучше поставить что-то более мощное, ход каретки около 10 сантиметров.
В качестве переносного «карманного» кондуктора можно использовать идею пользователя suvic.
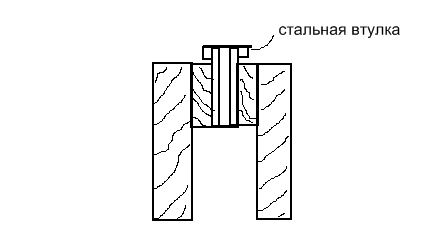
Просто и надежно, даже относительно точно, как для переносного варианта «must have» для мебельщика.
***************************************************************************
Ну и на закуску еще одна неплохая простая идея для тех, у кого нет места для стационарных конструкций.
[aslideshow]


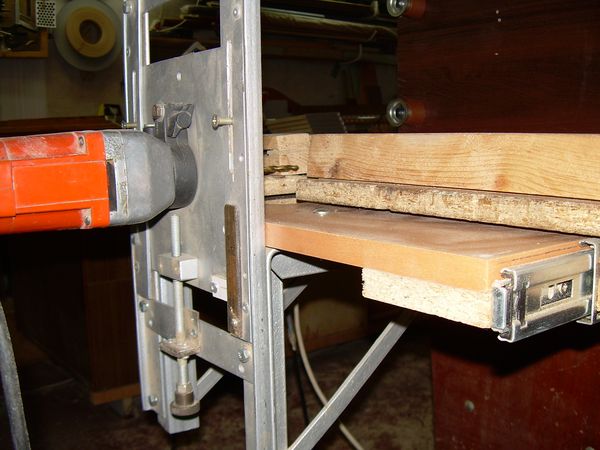
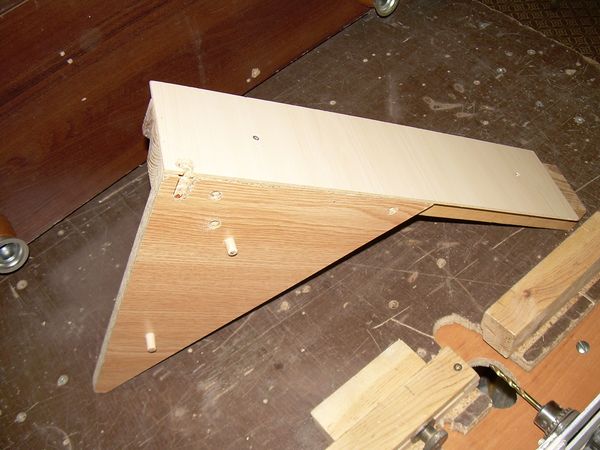
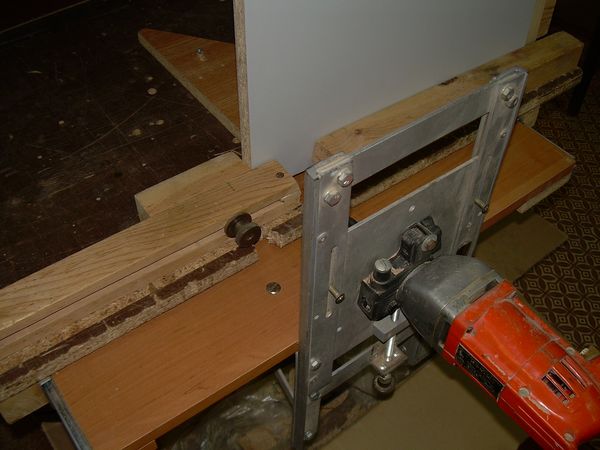
Приспособление предназначено для сверления как торцевого так и в пласть. Подъем сверла до 65 мм, упор выставляется по шаблону и используется одним размером и в торец и в пласть. Большие детали (шкафы и длинные элементы) проще и удобнее будет сверлить по кондуктору, а для небольших изделий, как кухонные элементы, например, это самое оно. Настройка очень простая, монтаж и демонтаж легкий и быстрый.
**************************************************************************
Кроме описанных в обзоре самодельных приспособлений существует большое множество серийных вещей, сейчас рынок завален различными вариантами линеек, разовых кондукторов и т.п. Но перед тем как покупать такие вещи, задумайтесь о их функциональности и удобстве использования, так как множество из них не расчитаны на то, чтобы производить большое количество работы. Это скорее приспособы для «домохозяек», испытывающих страх перед дрелью.
А то что мы видим в обзоре, это простые, и эффективные приспособления, сделанные бывалыми мастерами.
Использовать или нет описанные конструкции в своих целях решать все равно вам, а что удобнее и надежнее – покажет уже ваш опыт и опыт форумчан. Надеемся, и вы поделитесь своим опытом в комментариях к данному материалу.
И не забывайте посещать форум мебельщиков. Там тонны полезных идей и тем.
Кондуктор для сверления в торец
При изготовлении корпусной мебели, возникает необходимость иметь возможность точно и быстро производить засверливание в торец деталей. Как правило, эта необходимость обусловлена использованием евровинтов (конфирматов), при которых в торец деталей сверлятся отверстия диаметров 4,5-5,0 мм (зависит от плотности плиты) на глубину от 35-55мм (зависит от длины евровинтов).
Конечно, для таких целей существуют специальные сверлильно-присадочные станки, но они малодоступны частным мебельщикам или небольшим организациям по причине своей высокой цены, плюс к этому, станки не удобны по причине исключительно стационарного использования. Для упрощения работы мебельщика, были придуманы кондукторы – небольшие приспособления для точного сверления обычной ручной электродрелью. Сегодня на рынке существует несколько производителей, заплатив не малую цену, можно купить готовый кондуктор. В этой статье пойдет речь о том, как из подручного и легкодоступного материала за пару часов можно изготовить хороший самодельный кондуктор. В качестве направляющих сверло втулок, используем шариковые подшипники. Подшипники изготовлены из прочной стали, будут служить долго. Для того, чтобы сверло было хорошо сориентировано в кондукторе, для каждого рабочего расстояния применяются по два подшипника (подшипники расположены соосно другой под другом).
Для изготовления кондуктора (на три рабочих фиксированных расстояния) нам понадобится:
- Кусочек плиты МДФ толщиной 16мм.
- Кусочек плиты МДФ толщиной 10мм.
- Шесть штук (по паре для каждого рабочего расстояния) любых шарикоподшипников с внутренним диаметром 5,0 мм, внешним диаметром не более 16 мм. Высота подшипника должна быть, по возможности, как можно меньше и не более 8мм.
- Десяток саморезов 4×25 мм.
- Клей ПВА, «Суперклей».
- Футорка мебельная с внутренней резьбой M6 (см. фото).
-
Винт M6x50. Гайка M6. Шайба Гровера 6мм.
Изготовление корпуса кондуктора.
Для начала, необходимо изготовить сам корпус. Особо что-то пояснять по корпусу нет необходимости, все элементарно. Поперечное сечение корпуса – буква «П» с одной торцевой (закрытой) стенкой. Эта стенка будет использоваться в качестве упора, будет задавать нулевую точку, точку начала отсчета для сверления. При выполнении сверления, упор прижимается к торцу детали. Основные размеры:
- Внешний размер кондуктора произвольный.
- Верхняя деталь, в которую будут посажены подшипники, выполнена из МДФ 16мм, остальные детали — МДФ 10мм.
- Расстояние между двумя боковинами (где будет размещена обрабатываемая деталь) равно 16,5 мм, что соответствует реальной толщине плиты плюс небольшой зазор для удобства установки и съема кондуктора.
- Расстояния между центрами подшипников и упором: 50, 70, 100 мм, — самые распространенные в мебельной практике.
Для сборки корпуса необходимо точно вырезать все четыре детали (верх, две боковых и одну торцевую), измерения рекомендуется выполнять штангенциркулем. Далее, размечаются и сверлятся отверстия для саморезов, которые будут скреплять все детали воедино. Сборка корпуса выполняется с клеем ПВА.
Расстояние между боковыми стенками кондукторасоставляет 16,5 мм (для ЛДСП номинальной толщины 16 мм).
Посадка подшипников.
После высыхания клея, приступаем к разметке и кернению отверстий для подшипников. Стараемся очень точно выполнить эту операцию! Для сверления отверстий под подшипники нам понадобится сверлильный станок или дрель, закрепленная в стойке. Выполнить точное сверление от руки очень сложно, но, при определенной сноровке, возможно. Размечаем карандашом центры подшипников, керним. По кернению сверлим три сквозных отверстия диаметром 2 мм. Зажимаем в сверлильный патрон перовое сверло (пёрку), диаметр пёрки должен равняться внешнему диаметру подшипников. Сверлим по два глухих (несквозных) отверстия для каждого подшипника с каждой стороны просверленного ранее сквозного отверстия. Глубина сверления пёркой (глубина проникновения центрального шипа не учитывается) должна быть примерно на 1 мм больше высоты подшипника. В результате, мы должны получить шесть посадочных отверстий (по три с каждой стороны) для подшипников. Можно попробовать вставить подшипники в посадочные места, подшипники должны входить свободно, но без заметного люфта. После примерок, нужно смазать снаружи каждый подшипник клеем и посадить до упора на свое место. Если используется «Суперклей» (он быстро впитывается и высыхает), то эта операция выполняется с применением резиновой киянки.
Кондуктор сверху. Расстояния между центрами подшипников и упором.
Изготовление регулируемого упора.
Для возможности выполнять сверление на любых произвольных расстояния от упора (не только 50, 70, 100 мм), необходимо дополнить кондуктор несложным регулируемым упором — длинным винтом. Сверлим по центру торцевого упора сквозное отверстие диаметром на 0,5 мм меньше внешнего диаметра мебельной футорки (см. фото). Вкручиваем футорку. В футорку вкручиваем длинный винт, не забыв предварительно накрутить на винт гайку и надеть шайбу Гровера. Теперь, путем изменения глубины вкручивания винта, можно задать любое расстояние сверления от 0 до 100 мм.
Мебельная футорка. Для вкручивания футорки в корпус кондуктора понадобится шестигранный ключ.
Регулировочный винт кондуктора вкручивается в мебельную футорку.
Кондуктор. Вид сбоку.
Кондуктор. Вид изнутри.
Сверление отверстия в торце ЛДСП с применением самодельного кондуктора.
Вылет сверла. На такую максимальную глубину можно выполнить сверление. Длина применяемого сверла и глубина его крепления в патроне дрели должны выбираться с учетом толщины кондуктора (то есть, без малого, суммарной высоты двух подшипников).
При желании, поверхность кондуктора можно отшлифовать мелкой наждачной бумагой, загрунтовать и покрасить (например, эмалью из баллончика). Практика показала, что точность сверления с кондуктором получается не хуже +/-0,5мм и во многом зависит от того, насколько реальная толщина делали (плиты ЛДСП) отличается от расчетной толщины. В любом случае, погрешность максимум в полмиллиметра не является критичной для сверления в торец при изготовлении корпусной мебели.
Похожие статьи:
Самодельный кондуктор для сверления торцов деталей – Сделаем мебель сами
Здравствуйте друзья.
При сборке любых конструкций из ДСП или МДФ, всегда есть детали, которые стыкуются под прямым углом.
И в этом случае, одни из них сверлятся (под крепеж) по наружной плоскости, а другие (те, которые к ним стыкуются) – с торцов.
Торец детали должен сверлиться точно под прямым углом. Это очень важно по следующим причинам:
- Когда торец засверлен под прямым углом – это залог того, что в креплении не возникнут внутренние напряжения, нарушающие геометрию всей конструкции.
- При точной засверловке, всегда получится ровный (правильный) стык (это особенно важно для соединений с помощью шкантов, так как их нет возможности подрегулировать).
Это – чисто технические причины.
Но есть еще и организационные….
Часто, мебельщики сверлят торцевые отверстия вручную (я, например, всегда так делаю). Не знаю, может, у кого они и получаются идеально правильными, у меня все равно получается небольшой уклон. Но, что ни говори, а «рука набита», и весь этот процесс делается «на автомате».
Проблемы возникают тогда, когда нужны помощники (сборщики).
Без должной сноровки, неопытный сборщик может не только криво засверлить торец детали, а вообще, ее испортить (сверло, может «вылезти» с лицевой стороны детали). Одним словом, это один из самых «косяковых» моментов для неопытных сборщиков.
Так же, при большом объеме производства, сверлить торцы деталей вручную является не целесообразным по той причине, что это занимает довольно много времени.
По этому, рано или поздно, люди, занимающиеся изготовлением мебели, приходят к мысли о механизации этого процесса. А за мыслью, как вы понимаете, всегда следует действие.
Вопрос этот, естественно, в любом случае решаем: можно купить готовый сверлильно-присадочный станок, и работать себе в удовольствие.
Но такие станки стоят не дешево.
Если вы читали мой блог, то, наверное, «уловили», что вся соль мебельного производства (в частности, производства корпусной мебели) состоит в том, что его можно организовать, практически без вложений. А раз так, то больший интерес у любого мебельщика вызовет возможность самому сделать подобное приспособление (когда себестоимость которого будет стремиться к нулю), чем покупать готовый фабричный станок.
Вот, о подобных изделиях, которые можно сделать из подручных материалов, мы с вами и поговорим.
Итак, первое приспособление – кусок столешницы, на которой стационарно закреплена дрель. Деталь подается на сверло.
Для изготовления такого кондуктора, нужно сделать пазы под направляющую и под линейку (на фрезерном станке). Чем больше будет линейка, фиксирующая деталь, тем детали больших размеров можно будет на этом приспособлении обрабатывать.
Сама дрель закреплена между двумя кусками ДСП (стянутых между собой винтами), и выставлена по высоте (чтобы сверло точно попадало по центру детали).
Следующий вариант – более универсальный и «продвинутый».
На столе установлена дрель, которая подается на нужную глубину нажатием педали (под столом).
Данное приспособление способно обрабатывать детали больших размеров.
Дальше – стол с линейкой.
На каретке подается на нужную глубину двигатель от стиральной машины, на котором установлен патрон со сверлом.
Принцип работы прост. Тянем за рычаг – и сверло входит на нужную (заранее выставленную) глубину в деталь.
Ну и в заключении – небольшое приспособление, которое подойдет для тех, у кого просто нет места для установки стационарных шаблонов, из-за небольшого рабочего помещения.
В конце хотелось бы отметить, что подобных самодельных кондукторов существует «море». Этот обзор приведен просто как пример. Каждый сам придумывает то, что для него более подходит (исходя из возможностей) для облегчения работы и экономии времени.
А на этом все.
До новых встреч в следующих статьях.