Сверлильный станок из пластиковых труб своими руками
Эта конструкция станка для тех, кто хочет быстро сделать небольшой сверлильный станок, при этом не имеет желания или умения работать с железом.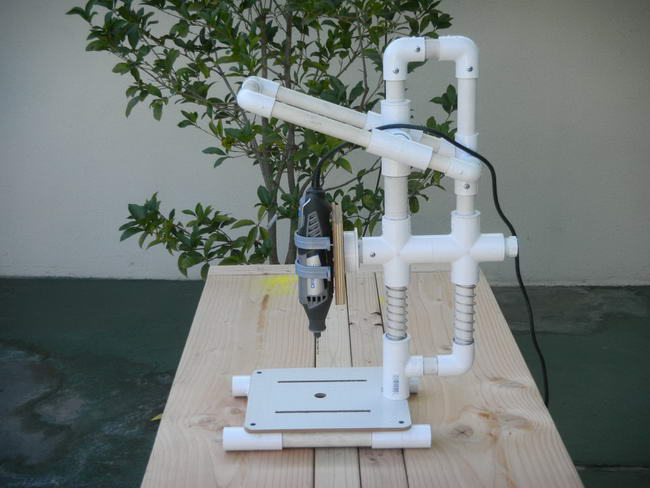
Сверлильный станок из пластиковых труб обладает рядом преимуществ, по сравнению со станком из железа:
- Просто в изготовлении.
- Легкий.
- Легко повторяем без всяких чертежей.
Уступает он железному разве что в нагрузочной способности, хотя для сверления небольших деталей его прочности хватает с головой.
На фото детали, которые вам понадобятся. Почти все их можно купить в сантехническом и строительном магазинах.
Обратите внимание, что помимо пластиковых частей в конструкции есть и две деревянные. Это основание станины и подложка крепления самой дрели.
Детали лежат так как они будут спаяны.
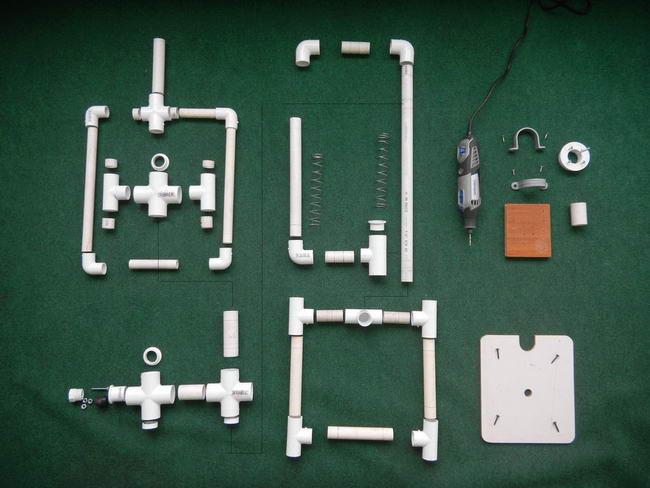
Какой диаметр трубы использовать? – Решать вам. Все зависит от размеров вашей дрели. Я взял диаметр 25 мм.
Начнем сборку сверлильного станка.
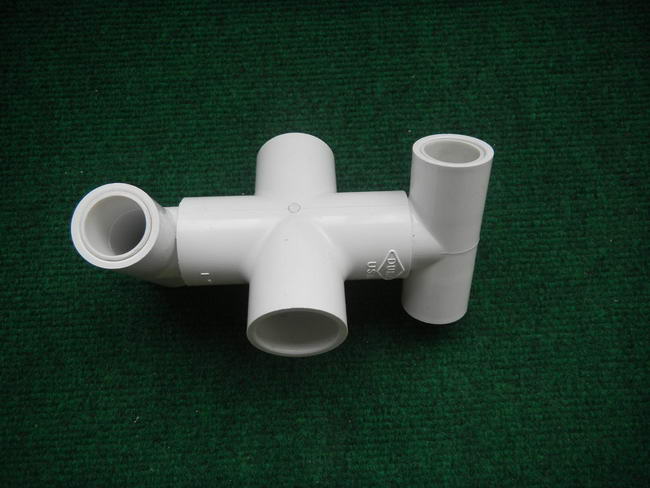
Движимый узел, который на рукоятки опускания и поднимания. Средняя крестовина больше по диаметру, чтобы она спокойное ездила по трубе. Она не спаивается, а просто собирается. Далее спаиваем центральный узел на котором будет крепиться дрель. Крестовины взяты такого же диаметра, что и трубки на которых она будет ездить. Брать её большего диаметра нельзя – слишком большой люфт будет, а чтобы она ездила по трубе без проблем, трубу необходимо сточить наждачной бумагой.
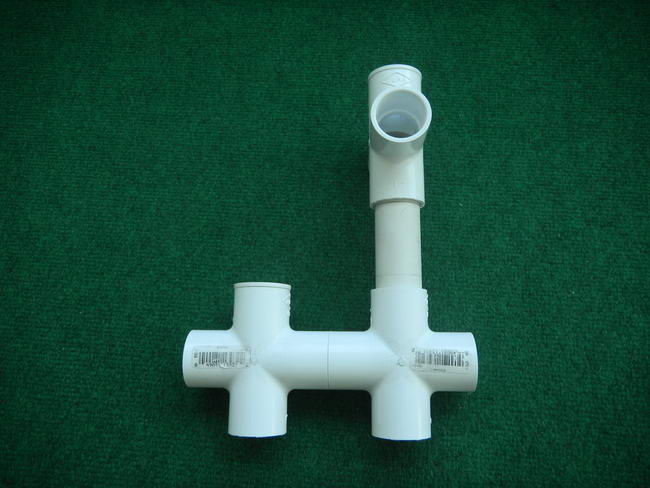
Собираем всю конструкцию со основанием станка.
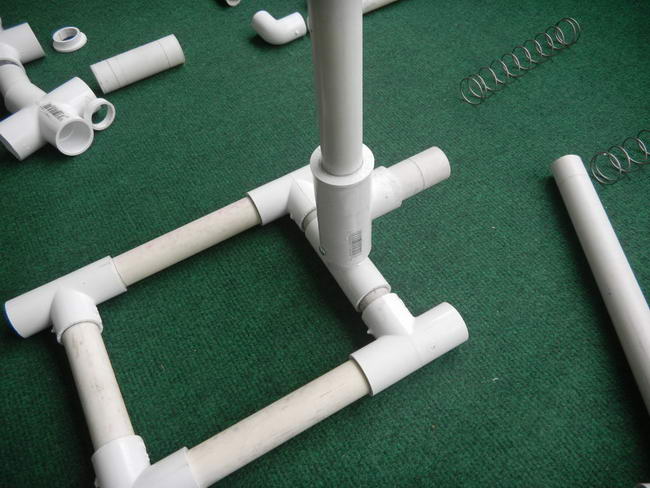
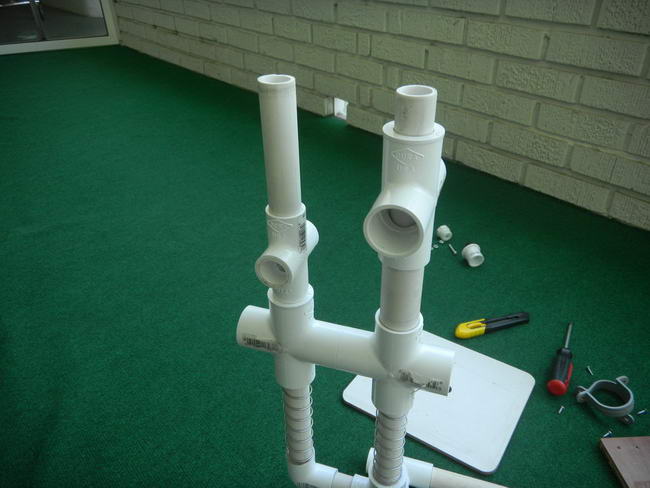
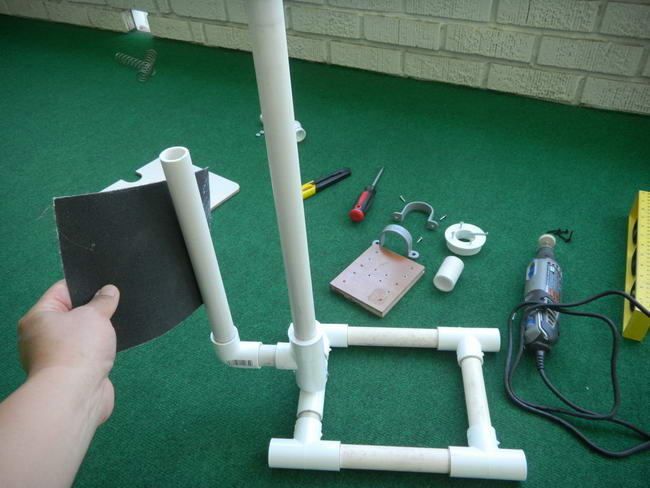
Пружины куплены. Похожие пружины можно попробовать найти в старом матрасе.
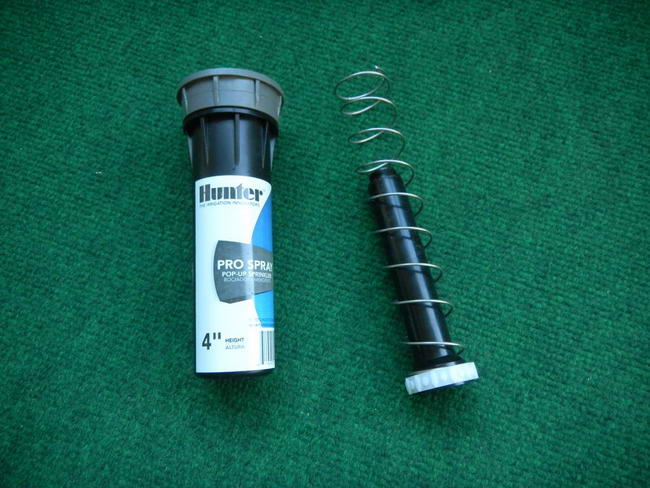
Узел дрели.
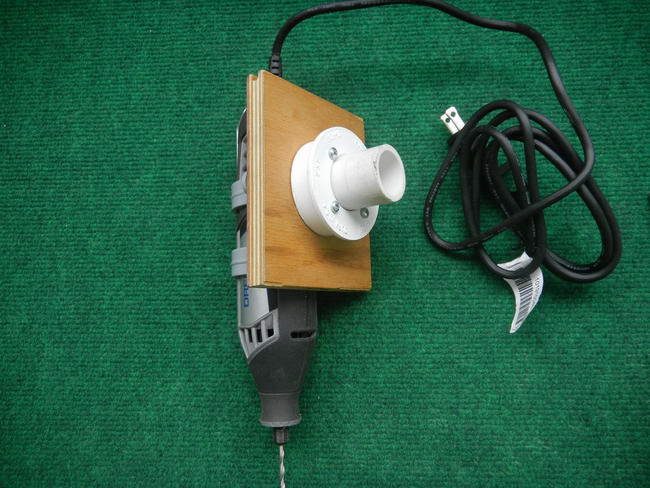
Станок готов. Основание деревянное, выпиленное предварительно и покрашено. В центре отверстие под свободный ход дрели.
Дрель закреплена пластиковыми хомутами. Также можно использовать дрель с пистолетной рукояткой, предварительно зажав курок.
При пайке станка будьте особо осторожны: используйте перчатки чтобы не обжечься.
Вот такой небольшой станок у меня получился, который хорошо подойдет для сверления радиоэлектронных плат, небольших металлических или пластмассовых изделий.
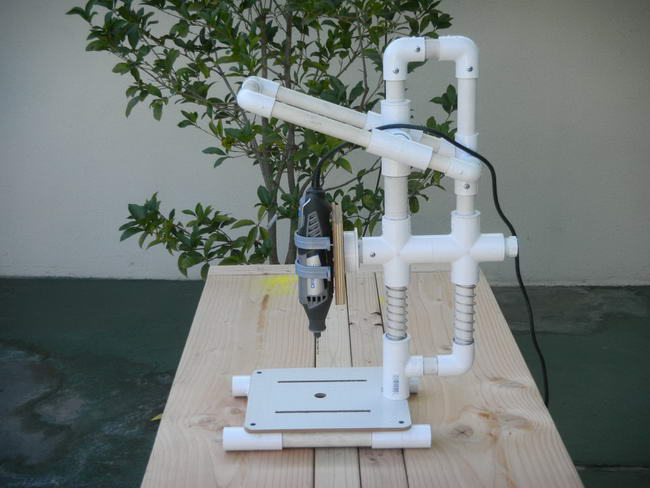
В общем применение в быту найдется обязательно.
Простой ткацкий станок из ПВХ-трубы и фанеры


В этой статье мастер-самодельщик расскажет нам, как он сделал простой ткацкий станок. Для изготовления станка не нужны дорогостоящее
Инструменты и материалы:
-Фанера;
-ПВХ-труба ø 25 мм;
-Деревянный дюбель;
-Колесико из нейлона;
-Шуруп;
-Силиконовый герметик;
-Дрель;
-Dremel Ultra;
-Коронки по дереву;
-Рулетка;
-Маркер;
-Ножовка по металлу;
-Гвозди;
-Молоток;
-Столярный клей;
-Акрил;
-Нитки;
-Палочки для мороженного;
Шаг первый: распиловка
Длина фанерного листа, который был у мастера, 61 сантиметр. Длина станка будет такой же длинны.
-7,5 см * 61 см;
-30,5 см * 7,5 см — 2 шт;
-28 см * 20 см;
-20 см * 7,5 см;
Шаг второй: отверстия
Теперь на вертикальных стойках и на продольной доске нужно сделать отверстия. Размечает центральную линию на всех трех заготовках. На вертикальных стойках сверлит по три отверстия: два сверху на расстоянии 4 см, 15 см, и одно снизу на расстоянии 5 см.
На продольной доске отверстие на расстоянии 36 см от задней части. Отверстия мастер вырезает коронкой по дереву на 25 мм.
Шаг третий: вырез
Для натяжения нити на длинную доску будет устанавливается деревянный дюбель. Для установки дюбеля в доске вырезается паз 13*0,6 см.
Шаг четвертый: сборка рамы
Теперь собираем станок, как на фото. На места соединения наносит столярный клей. Фиксирует детали гвоздями. Одна вертикальная стойка крепится на краю, вторая через 28 см.
Закрепляет собранный узел на опорной доске.
В торце дюбеля сверлит отверстие. Устанавливает дюбель в прорезь, и прикручивает в торец нейлоновое колесо.
Закрепляет под дюбелем еще одну доску с закрученными на боковой поверхности шурупами.
Шаг пятый: ПВХ-трубы
Отрезает семь отрезков ПВХ-труб по 18 см.
Устанавливает в отверстия станка.
Шаг шестой: челнок
Ткацкий челок, это рабочий орган ткацкого станка, прокладывающий уточную (поперечную) нить между нитями основы при выработке ткани.
Челнок мастер вырезает из акрила.
Шаг седьмой: работа за станком
Дальше мастер переходит к ткачеству. Для работы понадобятся нитки разных цветов и палочки для мороженного.
Навязывает из ниток белого цвета петли.
Привязывает конец нить к шурупу. Протягивает нить, как на фото.


Дальше нужно петлю из нитки. Обернуть вокруг цветной нити и надеть на нижнюю трубу.
Дальше, в зависимости от цветовой схемы полотна, продолжает наматывать нитки по той же схеме.
Когда нужная ширина полотна достигнута, концы ниток связываются.
Теперь нужно пропустить поперечную нитку. Сначала нитка наматывается на челнок. Затем нужно разделить намотанные нити. Для этого нужно просто надавить на полотно за белыми петлями. В просвет между нитями протягивается челнок с ниткой. Нитка «подбивается» к деревянной палочке. Затем челнок вытаскивается и полотно отпускается.
Продолжает ткать, продвигая полотно по кругу.
Когда почти все полотно соткано, лента снимается со станка. Петли вытаскиваются (их можно использовать в следующей работе). Теперь можно свободные нити разрезать и связать на концах.
Источник
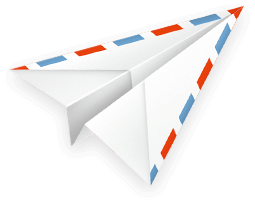
Получайте на почту подборку новых самоделок. Никакого спама, только полезные идеи!
*Заполняя форму вы соглашаетесь на обработку персональных данных
Становитесь автором сайта, публикуйте собственные статьи, описания самоделок с оплатой за текст. Подробнее здесь.Простая стойка для болгарки из профильных труб
Приветствую всех любителей помастерить, предлагаю к рассмотрению инструкцию по изготовлению простой и надежной стойки для болгарки своими руками. Такая стойка позволит превратить вашу болгарку в торцовочную пилу, это даст возможность резать трубы и другие материалы под точно заданным углом. Основным материалом для рамы послужили квадратные профильные трубы, а в качестве шарнира автор приспособил две длинные гайки и резьбовой стержень. Машина получилась очень простая, удобная, дешевая и долговечная. Если вас заинтересовала самоделка, предлагаю изучить проект более детально!
Материалы и инструменты, которые использовал автор:
Список материалов:
— пружина для дверей;
— квадратные профильные трубы;
— две длинные гайки и резьбовой стержень;
— уголок для упора;
— болты, гайки, шайбы;
— два крюка;
— краска на ваш вкус.
Список инструментов:
— болгарка;
— сварочный аппарат;
— угольник;
— маркер;
— дрель или сверлильный станок;
— зажимы;
— гаечные ключи.
Процесс изготовления самоделки:
Шаг первый. Нарезаем трубы
Автор нарисовал схему стойки на бумаге и приступил к нарезанию материала. Нам будет нужно нарезать трубы для основания, всего понадобится 8 отрезков. Помимо этого, понадобятся трубы для стойки.
Конечно, работать болгаркой от руки будет тяжеловато, так что все нужно предварительно разметить, в дальнейшем у нас уже не будет проблем с резкой, имея такую станину для болгарки.




Шаг второй. Крепеж для болгарки
Делаем крепеж для болгарки, тут автор тоже использовал квадратные трубы. Крепеж должен получиться в виде буквы «П». У автора болгарка будет крепиться двумя болтами, а также ручкой. Хорошо все свариваем и зачищаем сварные швы, чтобы изделие красиво смотрелось.
Шаг третий. Стойка и шарнир
Отрезаем два куска трубы и под прямым углом привариваем к основе, это и будет наша стойка. Предварительно в рубах сверлим отверстие под резьбовой стержень, который будет выступать в качестве оси.
Что касается шарнира, то он у автора «резьбовой», на резьбовой стержень устанавливаем две длинные гайки и свариваем их в одну гайку. Как итог получаем надежный, долговечный шарнир с минимальным люфтом, служить такой шарнир будет также долго, особенно если его смазать. Ну а резьбой стержень крепим к стойкам гайками с шайбами, по одной гайке с каждой стороны трубы. Гайки хорошо бы использовать со стопорными пластиковыми кольцами.


Шаг четвертый. Крепим болгарку
К шарниру привариваем два куска квадратной трубы, это будет рычаг, на конце которого мы и закрепим болгарку. Само собой, в машине должна иметься возможность регулировки, поэтому кронштейн болгарки к рычагу мы будем крепить через болты с гайками. На конце рычага автор приварил кусок уголка с расточенными отверстиями под овал, это и даст возможность регулировки угла диска.
После тщательной настройки и проверки всех углов, раму можно окончательно всю сварить. Автор зачистил сварные швы, в итоге изделие выглядит монолитным.
Шаг пятый. Упор
Изготавливаем упор, тут автор использовал кусок уголка. Конечно же, угол упора должен быть регулируемым, для этого автор приварил к основе болт, упор зажимается длинной гайкой сверху.
Шаг шестой. Ножки
Изготавливаем регулируемые ножки для станка, автор использовал болты с гайками. Теперь вы сможете отрегулировать станок так, чтобы он не качался даже на кривом столе.


Шаг седьмой. Пружина и испытания
Станок почти готов, на него остается установить мощную пружину, которая будет поднимать болгарку вверх. Автор использовал пружину для дверей, обрезав ее до нужной длины. Чтобы прикрепить пружину, ставим в нужных местах стальные крюки.
Самоделка готова, можно испытывать, автор с легкостью и довольно точно режет профильные трубы, теперь есть более широкие перспективы для творчества. Остается покрасить станок, теперь самоделка радует глаз, и не будет ржаветь!
На этом проект завершен, надеюсь, вам самоделка понравилась, и вы нашли для себя полезные мысли. Удачи и творческих вдохновений, если решите повторить подобное. Не забывайте делиться с нами своими идеями и самоделками!
Источник
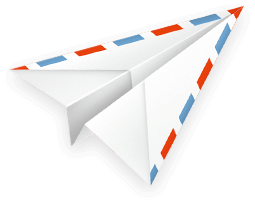
Получайте на почту подборку новых самоделок. Никакого спама, только полезные идеи!
*Заполняя форму вы соглашаетесь на обработку персональных данных
Становитесь автором сайта, публикуйте собственные статьи, описания самоделок с оплатой за текст. Подробнее здесь.Сверлильный станок из ПВХ труб: мастерим своими руками | Самоделки на все случаи жизни
Сверлильный станок – нужная и полезная вещь почти в любом гараже и мастерской. Без него сложно представить ряд слесарных работ. Именно сверлильный станок делает приятным и комфортным процесс сверления громоздких деталей и предметов, которые не очень удобно зажимать в тисках.
В данной статье мы расскажем, как изготовить сверлильный станок из водопроводных ПВХ труб своими руками.
Конечно, в первую очередь нам нужно приобрести водопроводные ПВХ трубы. Для нашей задачи подойдут и самые дешевые варианты для холодной воды. Также нам понадобится немного фурнитуры для данных труб и пружина.
В основе станка будет лежать дрель или многофункциональный сверлильный аппарат.
Собственно, все необходимые элементы представлены на фото ниже.
Размер выбираете лично вы, это индивидуальное решение для каждого.
Нам необходимо спаять или скрепить при помощи саморезов основу для нашего станка. Затем следует нарастить вертикальную стойку, на которой и будет крепиться наш сверлильный инструмент.
Потом стойку необходимо оборудовать пружинами для того, чтобы дрель не падал вниз, когда мы отпускали рычаг управления. Ведь нам нужен настоящий аналог станка для сверления.
В итоге у нас получается станок для сверления, который может быть использован в широком спектре задач слесарных работ. Такой станок имеет массу преимуществ. Конечно, основное преимущество – это его цена. Собрать такое устройство можно за сущие копейки, относительно его магазинных собратьев. Также данный станок не уступает по функционалу брендовым вариантам и его изготовление занимает мало времени и сил.
Надеемся, что данная статья будет вам, уважаемые читатели, полезна. Спасибо за внимание!
Похожие самоделки
Ткацкий станок из ПВХ трубы » Изобретения и самоделки
Сделайте простой ткацкий станок из трубы ПВХ.
В этом уроке рассказывается, как сделать простой ткацкий станок из доступного и материала ПВХ!
Я хотел построить ткацкий станок, потому что в последнее время я видел много очень милых ткацких проектов в блогах по домашнему дизайну и всегда думал: «Я мог бы сделать это!»
Приятного чтения, я уверен, что вы тоже можете сделать свой собственный станок!
Шаг 1: Инструменты и материалы.
Вот все инструменты и материалы, которые я использую в этой сборке. Мне очень нравится использовать ПВХ, потому что они немного похожи на гигантские структурные игрушки Tinker.
Шаг 2: Маркировка, куда пойдут колышки.

Я наложил малярную ленту на трубу из ПВХ, а затем использовал измерительную ленту и перманентную ручку, чтобы разметить расстояния 1/2 “, начиная и останавливая 1” от каждого конца, чтобы соединение все еще могло скользить до трубы позже.
Рисование прямой линии на цилиндрической поверхности – это боль, так что … лента на помощь! Из предыдущих сделок с ПВХ я узнал, что самый простой способ сделать маркировку вдоль изогнутой поверхности трубы лучше всего при помощи направляющей, прикрепленной к поверхности, вместо того, чтобы держать на месте волнистую рулетку
Шаг 3: штамповка и сверление в колышках.
Я использовал инструмент, чтобы сделать небольшие вмятины в ПВХ вдоль каждой из моих отметок 1/2 “.
Эти маленькие углубления будут действовать как указатели для винтов, чтобы войти в мягкий пластик ПВХ. Волшебство в использовании самонарезающих винтов что вам не нужно предварительно сверлить.
Шаг 4: Выровняйте колышки.
Колышки / винты выступали из трубы на разной высоте, и я хотел убедиться, что ни один из них не будет подвергнут риску выдергивания, и при этом они не будут настолько крепкими, что не смогут поместиться в шпагат за головкой винта.
Я опустился на уровне глаз с помощью колышков и быстро выполнил эту задачу с помощью ручной отвертки, но если ваша рука не устала от удерживания дрели, вы также можете использовать этот инструмент.
Шаг 5: Завершение сборки.


Я выложил диаграмму деталей на шаге материалов более близко, но ткацкий станок действительно соединился через несколько секунд после установки колышков.
Коленные суставы идут по нижней части квадрата, а 3-сторонние суставы идут по верхней части квадрата, а колышки лежат поперек ткацкого станка.
После того, как квадрат собран, 6-дюймовый элемент входит в заднюю часть 3-сторонних соединений и соединяется с 45-градусными соединениями, оставшимися стойками и торцевыми крышками.
Шаг 6: Внесение корректировок.
Я использовал перфоратор, чтобы удостовериться, что соединения ДЕЙСТВИТЕЛЬНО безопасны. Вдоль обоих рядов колышков я прошел молотком, чтобы выровнять колышки немного больше, чтобы струна не скользила за ними, и ориентировал колышки верхнего ряда, направленные на потолок.
Шаг 7: Начало натяжки шпагата.
Я начал натяжку с создания скользящего узла в струне и затянул его до колышка, который находился в 12 колышках от края.
Я использовал синтетическую нить для своей основы, что задним числом было ошибкой, я должен был использовать какое-то натуральное, более щадящее волокно – хлопковый шпагат, вероятно, идеален.
Шаг 8: Установите шпагат.


Убедитесь, что ваш перекос не слишком тугой. Я научился этому нелегко. В первый раз я расположил колышки лицом ко мне, и труба выскользнула из швов, когда я установил основу. Во второй раз я восстановил ткацкий станок так, чтобы колышки были направлены к потолку, и когда я сбросил основание, он, казалось, изгибался все меньше и жестче.
Шаг 9: Создание челнока.
Челноки – это вещи, которые переносят пряжу через основу. Они обычно представляют собой узкие, плоские, длинные катушки пряжи, которые можно легко вставить и протянуть между волокнами. Намного проще заложить нитку между волокнами, чем целую катушку пряжи, я сделал ее из картона за 2 секунды.
Шаг 10: Начни плести!
Я только начинаю, поэтому я не пробовал никаких причудливых стежков или узоров, я просто ходил туда-сюда, медленно укладывая слой за слоем. Правильное натяжение было немного сложным, но легче, когда я начал.
Шаг 11: Продолжай.
Хорошо, я не осознавал, что ткачество – такой своевременный навык! Хотя это было очень медитативно, эта часть заняла приблизительно 4-5 посвященных вечеров, чтобы закончить.
Каждый раз, когда я начинал или заканчивал разными нитями, я просто использовал один узел, чтобы прикрепить его к пряди основы.
Шаг 12: Снятие изделия с ткацкого станка.
Извлечь деталь из ткацкого станка было очень легко, все, что я сделал, это повернул верхнюю трубу из ПВХ, чтобы головки колышков были обращены к столешнице, а петли соскользнули с станка.
Шаг 13: Завяжите края.
Я знаю, что некоторые люди любят добавлять полосы или помпоны к своим тканым деталям, но для своей первой попытки я просто выбрал самый простой способ связывания – обычные узлы.
Я взял две нити основы одновременно и обмотал ее вокруг пальца, чтобы создать плотный узел.
Шаг 14: Склеивание свободной нити.
У меня была пара отлетевших свободных концов, которые я хотел спрятать в куске от хвостов, оставшихся свисающими с краев. Используя иглу для пряжи, я сплел их в пару столбцов, затем склеил хвосты. Я использовал Fabri-Tac, потому что я знал, что у него было короткое открытое время и очень быстрое время сушки, хотя я думаю, что для полного излечения требуется 24 часа.
Как только хвосты полностью высохли на ощупь, я подрезал их ближе к куску.
Шаг 15: Обучение
Я упоминал об этом выше, но, если бы я не натягивал основание так сильно, кусок заканчивал тем, что немного сгибался в середине из-за того, что стороны становились все плотнее, когда я поднимался на ткацкий станок. Еще одно замечание о перекосе: я использовал синтетическую нить, потому что это то, что у меня было, но в ретроспективе я бы хотел использовать вместо этого тяжелую хлопковую нить, это дало бы больше и, возможно, решило бы некоторые из моих дурацких проблем с натяжением.
Все изображения фактического плетения, которые я включаю в этот учебник, в основном, я играю, «рисую» и изучаю нюансы домашнего ткацкого станка.
Спасибо, я надеюсь, что это вдохновит вас попробовать сделать ткацкий станок!
Источник
Сверлильный станок из пластиковых труб своими руками
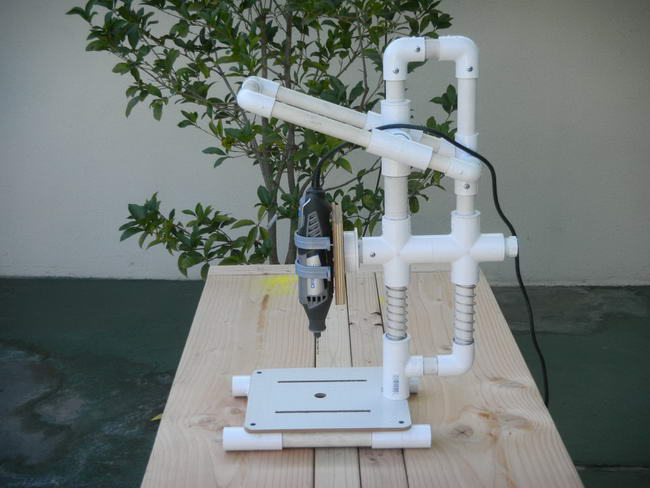
Сверлильный станок из пластиковых труб обладает рядом преимуществ, по сравнению со станком из железа:
- Просто в изготовлении.
- Легкий.
- Легко повторяем без всяких чертежей.
Уступает он железному разве что в нагрузочной способности, хотя для сверления небольших деталей его прочности хватает с головой.
На фото детали, которые вам понадобятся. Почти все их можно купить в сантехническом и строительном магазинах.
Обратите внимание, что помимо пластиковых частей в конструкции есть и две деревянные. Это основание станины и подложка крепления самой дрели.
Детали лежат так как они будут спаяны.
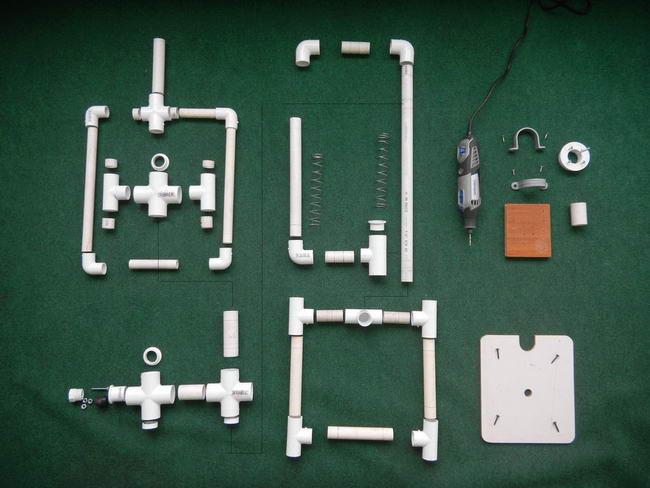
Какой диаметр трубы использовать? – Решать вам. Все зависит от размеров вашей дрели. Я взял диаметр 25 мм.
Начнем сборку сверлильного станка.
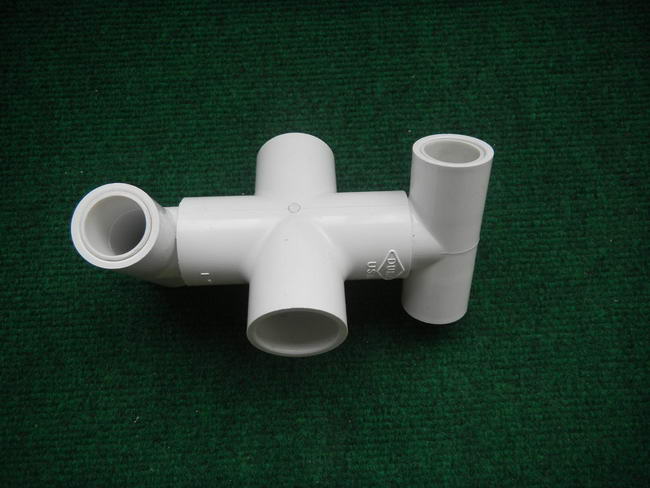
Движимый узел, который на рукоятки опускания и поднимания. Средняя крестовина больше по диаметру, чтобы она спокойное ездила по трубе. Она не спаивается, а просто собирается. Далее спаиваем центральный узел на котором будет крепиться дрель. Крестовины взяты такого же диаметра, что и трубки на которых она будет ездить. Брать её большего диаметра нельзя – слишком большой люфт будет, а чтобы она ездила по трубе без проблем, трубу необходимо сточить наждачной бумагой.
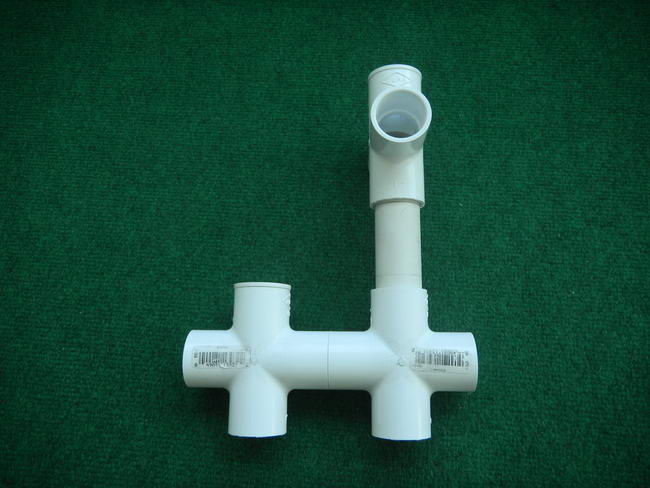
Собираем всю конструкцию со основанием станка.
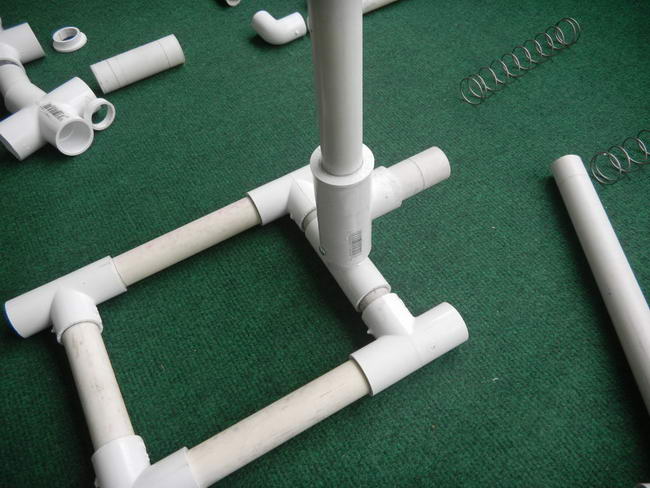
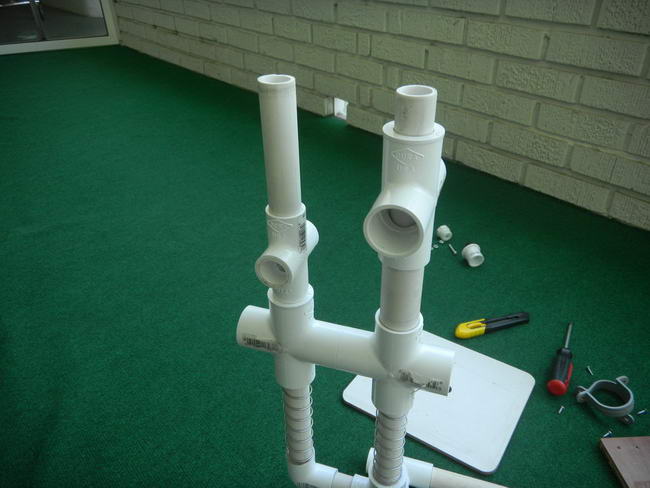
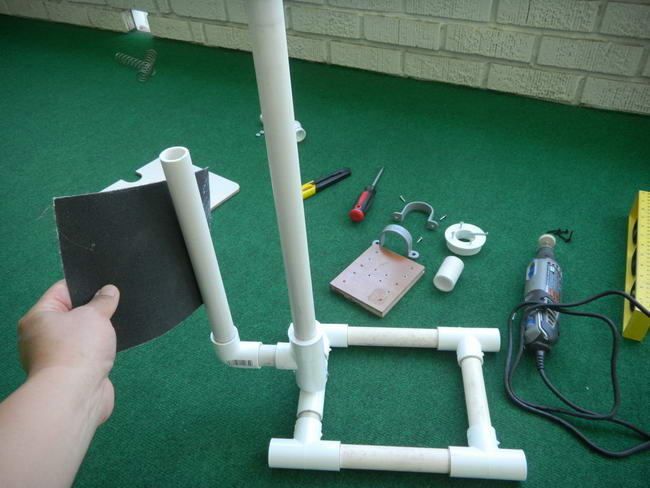
Пружины куплены. Похожие пружины можно попробовать найти в старом матрасе.
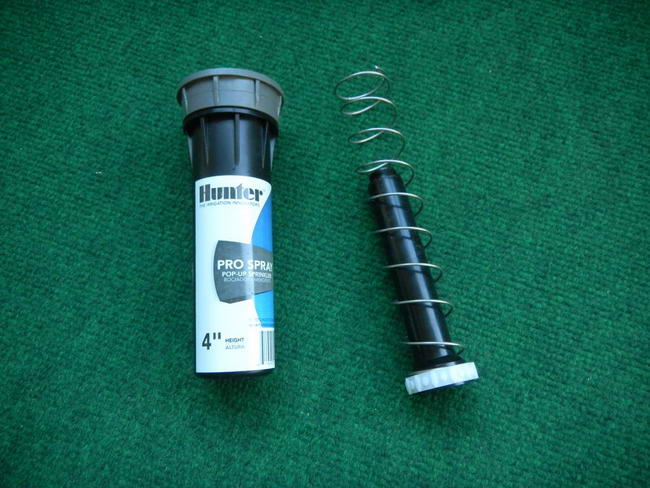
Узел дрели.
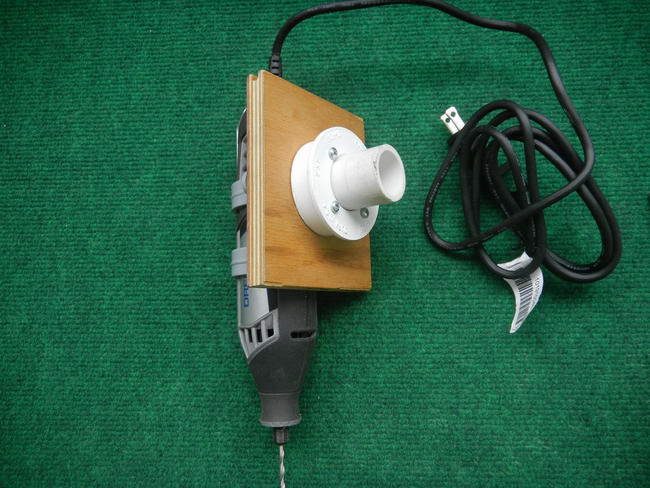
Станок готов. Основание деревянное, выпиленное предварительно и покрашено. В центре отверстие под свободный ход дрели.
Дрель закреплена пластиковыми хомутами. Также можно использовать дрель с пистолетной рукояткой, предварительно зажав курок.
При пайке станка будьте особо осторожны: используйте перчатки чтобы не обжечься.
Вот такой небольшой станок у меня получился, который хорошо подойдет для сверления радиоэлектронных плат, небольших металлических или пластмассовых изделий.
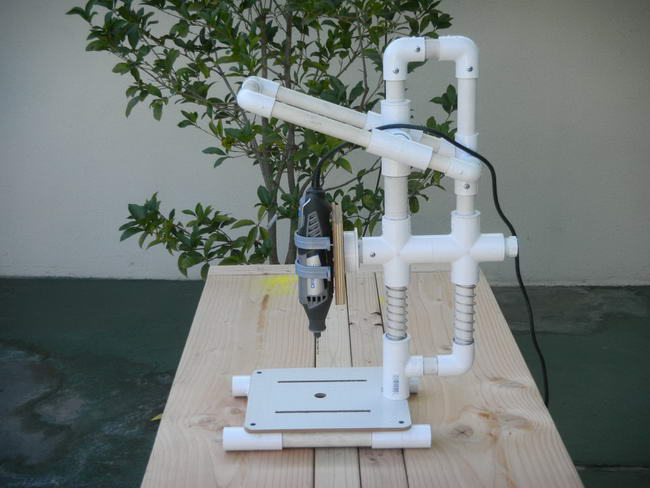
В общем применение в быту найдется обязательно.
Разновидности станков для гибки профильной трубы: Обзор +Видео
Станок для гибки профильной трубы считается одним из оборудований для обработки металлических изделий. Разрезать профильную трубу можно, используя ручной инструмент, а изогнуть конструкцию удастся только, применив оборудование, сгибающий металлические изделия.
Данные станки можно приобрести в готовом заводском варианте, либо смастерить своими руками. Так как оборудование, которое используют в доме редко, значит, не следует тратить деньги на покупку серийного станка. Изучив доступные чертежи устройства, стоит создать станок самостоятельно.
Содержание статьи:
Из чего состоит профилегиб
Перед тем, как начать работы по созданию оборудования, рисуют чертеж изделия. Какую схему для работы взять за основу обуславливается наличием определенного материала в доме.
Фронтальная разновидность оборудования включает такие элементы:
- валы три штуки, три штуки роликов.
- приводное цепное устройство.
- несколько осей.
- профильные детали, выполненные из металла, с помощью них выполняют раму-основание под станок.
Устройство принято оснащать деревянными либо полиуретановыми роликами. Выбирая элементы для изготовления, обращают внимание на прочность труб, чтобы профилегиб справился с нагрузкой.
Разновидности станков
Чтобы изменить конфигурацию трубы, создали множество моделей станков. Обусловлено это различием в минимальном радиусе сгиба. Нельзя пренебрегать данным значением, потому что, превысив параметр, нарушится целостность материала и понизит прочность изделия. Выбирая схему устройства, опираются на технологические особенности процесса гибки. Выбирая подходящую конструкцию учитывается материал изделия, внутреннее сечение, толщина стенок.
Разновидности устройств по приводным особенностям
Конструкции, имеющие разный приводной механизм, бывают ручными, электромеханическими, гидравлическими:
- Ручной станок считается самым простым оборудованием, монтаж изделия н требует специальных знаний.
- Электромеханический станок работает от шагового либо обычного электродвигателя, который подключают посредством нижнего редуктора, который равномерно распределяет напряжение и гарантирует высококачественный изгиб. Чтобы смастерить станок, необходимо иметь знания в металлической сфере.
- Гидравлическое устройство оснащено ручной приводной системой. Отличие данной конструкции от станка с обычным ручным управлением в том, что конструкция оснащена гидроцилиндром, это позволяет для выполнения работы применять минимум усилий. Вальцы сгибают профили в любую конфигурацию. Гидравлический профилегиб может согнуть трубу, равную 10 сантиметров.
Как различается оборудование от разновидности установки
Установочный способ влияет на конструкцию устройства. Конструкции бывают:
- Стационарные. Стационарное устройство выполнено в виде плиты из бетона со вставленными стержнями, либо как мощное устройство.
- Переносимые. Переносимые модели оснащены стойками, они компакты в применении.
- Носимые. Носимая модель не имеет опорных конструкций, приспособление под нее обустраивают в каждом случае отдельно.
Виды оборудования, которые отличаются методом изгиба профилей
Разновидность изгиба влияет на устройство конструкции, также ее производительность.
Методы, которые применяют для изгиба:
- С помощью выдавливания. Деформирующий ролик в качестве пуансона изменяет конфигурацию трубы. В устройстве нет матрицы. Для работы необходимо наличие двух надежных опор, расположенных по обе стороны изгиба, они же выступают в роли матрицы. Опорами служат поворотные ролики либо башмаки.
Справка! Качественный результат достигается с помощью равномерно нарастающего усилия, которое постоянно направлено к трубе под 90 градусами. Метод подходит для небольших работ.
- С помощью прессования. В основе принцип работ тисков слесарных, которые прессуют трубу, расположенную между пуансоном и матрицей. Чтобы качественно выполнить изгиб, профили должны двигаться точно по форме детали. Рассчитывая параметры, учитывают остаточное изменение формы металла. Если изгиб не требует точных замеров результата, то можно применять данную модель.
- С помощью прокатывания. Считается универсальным процессом, который применяют для всех видов трубных изделий, с толстыми и тонкими стенками. Изгиб получается с помощью протягивания заготовочных деталей сквозь ролики, один служит для вращения, два считаются опорой.
Существуют другие способы изгиба труб, такие, как вальцовочный, способ намотки, накатки и арбалетный метод, с помощью песка либо болгарки.
Во время работ по изготовлению стоит придерживаться советов профессионалов. Толщина металла станины не должна быть менее одной шестой от ширины трубы. К примеру, труба для изгиба имеет сечение в виде прямоугольника 50 на 25 миллиметров, во избежание деформации металла станины во время изгибочного процесса, применяют уголок либо швеллер, который имеет толщину свыше 1 см. Плита бетонная, матрица, пуансон должны иметь толщину больше в два раза. Размер внутреннего сечения роликов должен составлять три размера диаметра профиля. Ширину трубного профиля от полки швеллера с уголком берут в три раза меньше.
Во время изготовительных работ по изгибу трубы в виде прямоугольника, с сечением равным 50х25 миллиметров, применяют следующие параметры швеллера с уголком соответственно: 100х10, 150х10.
Устройство гидравлического типа своими руками
Конструкция с гидравликой работает посредством продавливания по центру профиля при помощи пуансона, который прикреплен к поднимающемуся штоку. Заготовка опирается на пару неподвижных опор, плотно прижимается пуансоном, постепенно приобретая его форму. Необходимо выполнить разметку поверхности, служащую для работы. Нужно прочертить ось по вертикали, выделяя нижние отверстия на определенной дистанции от оси. Далее делают разметку отверстий сверху. Центры отмеченных отверстий соединяют сквозной линией, деля ее на одинаковые куски.
Оси у отверстий, лежащих в промежутке, располагаются на линии пересечения наклонной оси с выполненными отметками. Отверстия на конструкции станка нужны, для регулирования радиуса сгиба изделий. Рабочая поверхность устройства представляет собой две детали, которые располагаются зеркально. Поэтому на второй детали делают те же отметки.
Размер домкрата, расстояние с обозначением «а» на схеме влияют на высоту оборудования.
Если надо изогнуть изделие, имеющее ширину 15 миллиметров, то зазор в статическом режиме домкрата должен равняться двадцати миллиметрам. Усилительные нагрузки данной конструкции, которое передает пуансон, сосредоточено сверху устройства. данное свойство способствует растяжению радиуса профиля снаружи, что может спровоцировать разрыв изделия. Чтобы изменить конфигурацию заготовок с тонкими стенками, данный станок применяют редко.
Станок прокатный
Деформация деталей происходит с помощью прокатки. Самостоятельно можно смастерить оборудование, имеющее три ролика с ручным типом привода. Существуют два вида подобных устройств. Самодельный станок, имеющий поворотную платформу.
Подходит для деформации труб, у которых некруглая внутренняя полость, имеет следующие особенности конструкции:
- Угол сгиба детали выполняет поворотная платформа. Металлическую станину соединяют с платформой с помощью шарнирного соединения.
- Домкрат задает движение платформе, который упирается в корпус платформы штоком.
- Вращая рукоятку, осуществляют протяжку профильной трубы. Рукоятка расположена в промежуточном валу.
Стойки и основание оборудования изготавливают из трех швеллеров, которые имеют стеночную высоту в пределах от 150 до 200 миллиметров. Основу под вальцы и обоймы подшипников выполняют из металлического профиля, которая имеет внутреннюю окружность равную внешнему сечению подшипника. Эту трубу разрезают на шесть кусков. С помощью швеллера изготавливают две платформы и основу станка. Из данного швеллера с помощью сварки монтируют стойку вертикальную, отступая примерно пол сантиметра от одной стороны.
Для прочности конструкции стойки, ее изготавливают из двух отрезков. Опираясь на горизонтальную ось, устанавливают постоянную платформу, затем к ее корпусу монтируют стойку сзади оборудования с помощью сварки. Из одного отрезка профиля выполняют ограничители, высота их должна быть больше толщины трубы, которую будут деформировать с помощью станка.
Платформа, задающая направление, присоединяется к основной станине с помощью петель для дверей. Подшипники приваривают к ограничителям и краям двух платформ, снабжают конструкцию для прочности уголками. В подшипники устанавливают валы. К валу, находящему посередине, устанавливают ручку. Под платформой с края для обеспечения направления ставят домкрат, скрепляют его с основой с помощью болтов.
Последовательность рабочего процесса:
- Подготовка материала, набора инструментов.
- Сборка основной платформы.
- Нарезка трубы под подшипники.
- Выполнение соединения вальцев с подшипниками.
- Присоединение катка с помощью сварки.
- Изготовление основы под каток.
- Сборка всех элементов конструкции.
- Проверка на качество работы устройства.
Станок прокатный трех роликовый
Изгиб трубы осуществляется с помощью роликов, которые находятся по бокам. Трубу кладут сверху на ролики. Двигающийся ролик сверху опускают и фиксируют изделие. Вращая ручку, с помощью цепи приводят в движение валы. Труба движется и меняет положение. Прижимной болт закручивается, усилие на трубу увеличивается, изделие продвигается и получается изгиб.
Внимание! Данный станок имеет три ролика. Если подсоединить к оборудованию электрический двигатель с мощностью в полтора килло ват, то можно деформировать трубы за один раз, имеющие сечение около восьми сантиметров.
Что необходимо для изготовления конструкции:
- полка
- профильный прокат из металла для изготовления каркаса.
- валы.
- пружины прочные, 4 шт.
- цепь, крепежные элементы, подшипники.
Чтобы прикрепить подшипники, нужно три вала, размер определяют по звездочкам и подшипникам. С боку устанавливают 2 вала, прижимной вал подвешивают сверху с помощью пружины. Данные детали необходимо заказать у специалистов, всю остальную работу можно сделать своими руками. Прижимной вал включает в себя кольца, подшипники, также шестерни. Кольца оснащают резьбой, по размеру равную болтам для зажима, далее проделывают пазы. Полки, изготовленные из швеллера, оснащают местом, куда будет опускаться вал для прижима профиля. Далее собирают весь станок, начинать надо с оборудования каркаса.
Затем подвешивают вал на пружинке, который соединен с полкой шпоночным соединением. Валы для опоры крепят с двух сторон основания, между опорами протягивают цепь, удерживая ее с помощью магнитного уголка. На вал для опоры прикрепляют ручку для поворота, монтируют на платформу домкрат с помощью болтов и сварки.
Подвесной вал требует правильной установки:
- установить вал на полку.
- к полке монтируют гайки для крепления пружины.
- площадку соединяют с пружинами, переворачивая площадку.
Важно! Если увеличить расстояние между роликами, то усилия, которые необходимы для создания изгиба, уменьшатся.
Поэтапный процесс сборки прокатного устройства:
заказать валы у специалистов.
- сделать каркас под устройство.
- устанавливают прижимной вал.
- прикрепляют пружины.
- закрепляют валы.
- протягивают цепь.
- делают ручку.
- наносят краску на конструкцию.
Простейший способ для гибки профиля
Самым простым методом для деформации профилей служит деревянный шаблон. С помощью него можно изменить форму трубы с тонкими стенами, например, стальные и алюминиевые. Для конструкции понадобятся доски, скрепляя детали. Затем производят выпилку деревянного шаблона.
Внимание! Практичнее изготавливать съемные шаблоны, потому что их можно заготовить в нескольких экземплярах разного радиуса. Для шаблона можно применять металлические крючки, расположив их на прорисованном контуре.
Толщину шаблона в месте, где он касается трубы, надо делать больше на пару сантиметров, нежели размер диаметра профиля. С краю шаблон должен иметь наклон, чтобы труба не скользила. На устройство монтируют упор, чтобы закрепить с прочным основанием. Профильную трубу кладут в промежуток между шаблоном и упором, производя деформацию материала, начинают процесс с конца профиля.
Начинать с центра нельзя, потому что это грозит сплющиванию всего изделия, так как материал слишком тонкий. Для облегчения процесса, внутрь трубы вставляют стержень из металла, диаметр его должен быть равен стольким, чтобы осуществлять проход сквозь трубу. Для сгиба более толстых труб станок усиливают лебедкой, закрепляя крепче профиль, чтоб не соскользнул.
Станок, изготовленный на заводе
Если профессиональная деятельность требует постоянного применения станка для гибки труб, то стоит приобрести серийный станок. Конструкции, изготовленные на заводе, обладают множеством функций, высокой мощностью и прочностью.
Ручное устройство компактного размера можно купить недорого.
Какими преимуществами обладает заводской станок:
- станки имеют автоматизированный процесс управления.
- станки оснащены сменными насадками, что расширяет спектр применения одного станка для разных профилей.
- некоторые станки имеют пульт управления на расстоянии.
- конструкции имеют небольшие размеры, из-за этого станки мобильны.
- серийное оборудование легко устанавливается на твердой гладкой поверхности.
- станки выполняют изгибы сложной конфигурации, к примеру, в виде N или П.
Работать за станком можно подготовленным людям, пройти обучение несложно по интернет-видео.