Поролон
ШВЕЙНОЕ ПРОИЗВОДСТВО
Эластичный поролон (пенополиуретан) — высокопористый упругий материал, получаемый химическим путем, В состав композиции для производства поролона входят: изоцианаты, гидро — ксилсодержащие олигомеры (простые олигоэфиры), вода, катализаторы, эмульгаторы.
Эластичный поролон (на основе полиэфира П2200) выпускается плотностью (кажущейся) 0,025; 0,035; 0,04; 0,045 г/см3. По теплозащитным свойствам поролон не уступает другим утепляющим материалам, а тепловое сопротивление прокладки из поролона несколько выше, чем других прокладок, при сравнительно одинаковой их толщине. Температура применения поролона -15… +100 °С.
Размягчается поролон при температуре 150 °С, плавится при температуре 180 °С. Необходимо иметь в виду, что при нагревании и особенно при плавлении поролон из-за наличия в его составе изоцианатов становится сильно токсичным. Поэтому при обработке поролона необходимо строго соблюдать условия охраны труда (например, обеспечивать сильную приточно-вытяжную вентиляцию).
По данным ЦНИИШПа, толщина поролоновых прокладок в зимней одежде, предназначенной для носки в районах с умеренным климатом, должна быть 6 — 8 мм, а в более суровых климатических районах — 9—12 мм. Однако поролон такой толщины плохо драпируется, а внешний вид одежды с такими поролоновыми прокладками получается некрасивым. Поэтому для одежды рекомендуется применять поролон в виде листов толщиной 2 — 3 мм, сложенных в несколько слоев. Соединяют детали одежды из поролона на обычных швейных машинах. Наблюдение за изделиями с поролоновыми прокладками показывает, что при носке поролон не крошится, не сваливается, легко чистится. Поролон достаточно прочен и характеризуется большим удлинением, воздухопроницаемость его при сравнительно одинаковой толщине прокладок значительно меньше, чем ваты и ватина. Гигроскопичность поролона незначительна и в то же время вследствие большой пористости он легко впитывает влагу, а после отжима быстро высыхает. По сравнению с другими материалами поролон имеет наибольшую упругость при сжатии.
Мерцание – новая тенденция в блеске
Блеск декоративных элементов одежды, тканей, аксессуаров – неотъемлемая часть модных коллекций нескольких последних лет. Несмотря на это, каждый раз творцы мира фешн индустрии доказывают, что блеск блеску рознь, он может …
Твил — очаровательный внешний вид, комфорт при ношении, пошив любой одежды
Материал твил производители выпускают в различных разновидностях. Из текстиля шьют одежду, декорируют интерьеры. Отдельные сорта ткани производятся для пошива подкладки в верхних носильных вещах. Материал шелковистый и нежный с приятным …
Материалы для изготовления палаток
Вылазки на природу по-прежнему остаются одним из самых романтичных и интересных видов досуга. Веселый пикник, пляжные развлечения, охота и рыбалка могут затянуться на несколько дней, поэтому отдыхающим обязательно понадобится добротная …
Продажа шагающий экскаватор 20/90
Цена договорная
Используются в горнодобывающей промышленности при добыче полезных ископаемых (уголь, сланцы, руды черных и
цветных металлов, золото, сырье для химической промышленности, огнеупоров и др. ) открытым способом. Их назначение – вскрышные работы с укладкой породы в выработанное пространство или на борт карьера. Экскаваторы способны
перемещать горную массу на большие расстояния. При разработке пород повышенной прочности требуется частичное или
сплошное рыхление взрыванием.
Вместимость ковша, м3 20
Длина стрелы, м 90
Угол наклона стрелы, град 32
Концевая нагрузка (max.) тс 63
Продолжительность рабочего цикла (грунт первой категории), с 60
Глубина копания, м 42,5
Радиус выгрузки, м 83
Просвет под задней частью платформы, м 1,61
Диаметр опорной базы, м 14,5
Удельное давление на грунт при работе и передвижении, МПа 0,105/0,24
Размеры башмака (длина и ширина), м 13 х 2,5
Рабочая масса, т 1690
Мощность механизма подъема, кВт 2х1120
Мощность механизма поворота, кВт 4х250
Мощность механизма тяги, кВт 2х1120
Мощность механизма хода, кВт 2х400
Мощность сетевого двигателя, кВ 2х1600
Напряжение питающей сети, кВ 6
Более детальную информацию можете получить по телефону (063)0416788
Эксплуатация поролона и изделий из него
Покупая диван, кресло или какой либо другой товар, в состав которого входит поролон, следует знать основные рекомендации по его эксплуатации.
Если поролон намочить, то его физико-механические свойства меняются. Поэтому намокший поролон нельзя подвергать нагрузке, сдавливать его или как-то по другому деформировать. Сначала необходимо его просушить, и уже потом пользоваться.
Необратимо испортить поролон может спиртовой раствор. Категорически запрещается протирать мебель или другие предметы, содержащие в своем составе поролон, спиртовыми растворами, так как при этом поролон разрушается. Об этом стоит помнить, прежде чем обрабатывать, например, пятно на диване спиртосодержащим пятновыводителем.
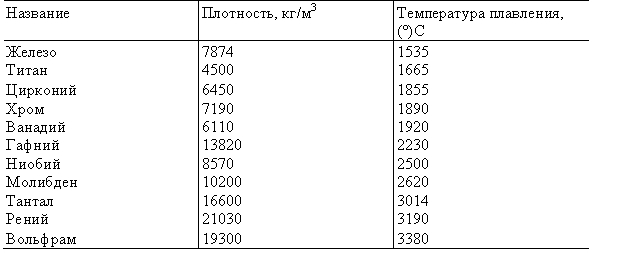
По определению поролон выдерживает температуры от -15°С до +100°С. Однако не рекомендуется допускать повышенное термическое воздействие на поролон, так как оно также губительно на нем сказывается. Недопустимо располагать поролоновые изделия вблизи открытого огня или раскаленных объектов. Гладить утюгом поролон и изделия из него также нельзя.
Однако для некоторых сфер применения просто необходим поролон, на который будет воздействовать высокая температура. В этом случае применяют жаростойкий пенополиуретан, в состав которого входят специальные компоненты, которые придают необходимые свойства. Такой поролон могут применять, например, в гладильных досках для обработки тканей, на которых нанесена вышивка, стразы, пришиты пуговицы и прочие выпуклые украшения.
Одним из главных факторов ухудшения качества поролона является транспортировка. При перевозке поролон сжимают, чаще всего, уменьшая его объемы в 4-6 раз.
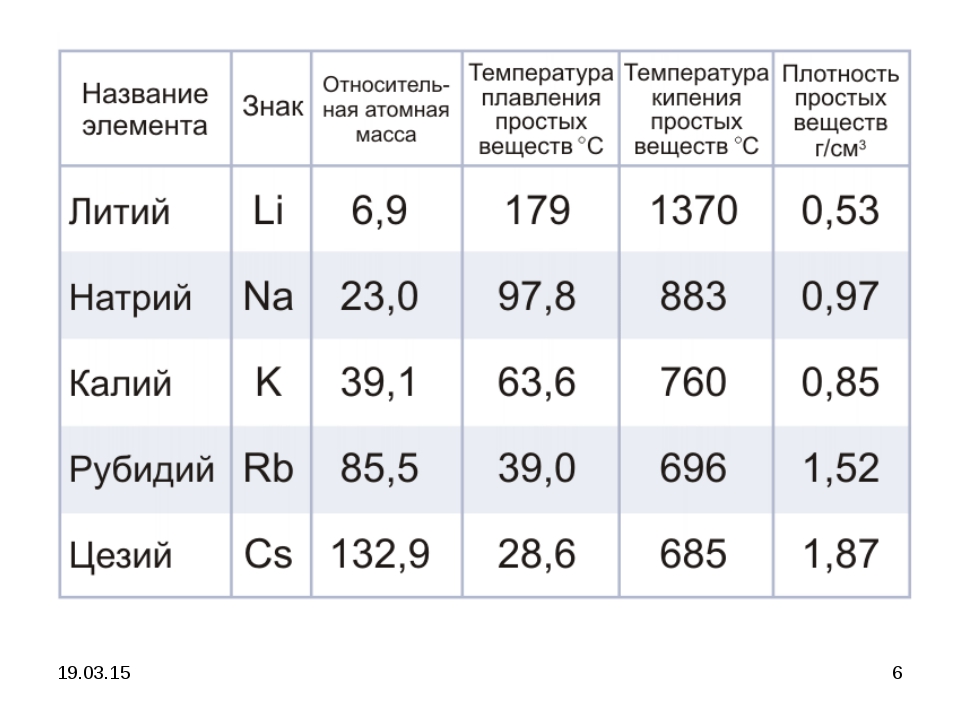
В зависимости от характеристик качества поролона его срок эксплуатации значительно отличается. Главным критерием при этом служит плотность поролона. Однако максимально допустимый срок службы поролоновых изделий – 15 лет. Снизить эксплуатационный период может вредное и агрессивное воздействие окружающей среды. В том числе особенно сильно влияет на срок эксплуатации поролона повышенная влажность, колебания температур, высокая температура воздуха.
Поролон свойства — Справочник химика 21
Свойства поролона. Поролон представляет собой мягкую пену от белого до коричневого цвета с однородной структурой пор. Он может выпускаться и окрашенным. Обладает достаточной прочностью, высокими показателями тепло-, звуко- и электроизоляционных свойств п хорошими амортизационными свойствами.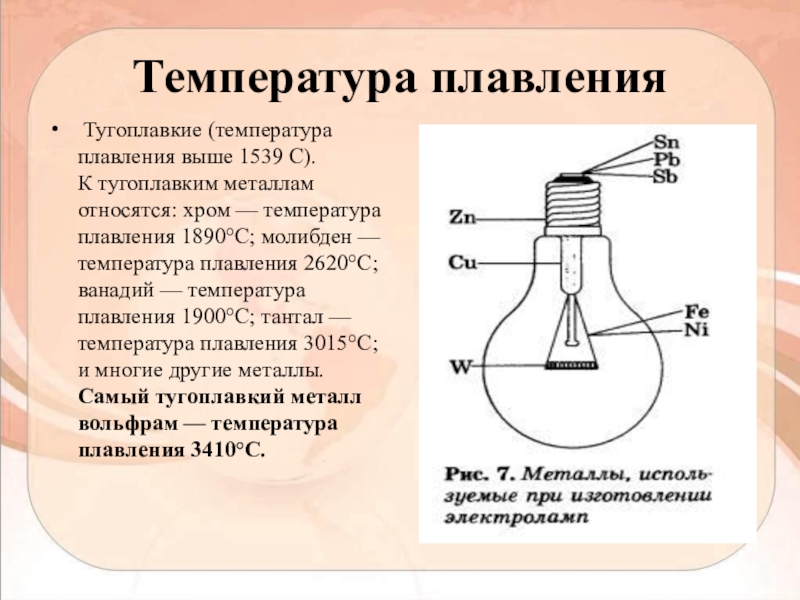
Ниже приведены показатели основных свойств поролона [c.87]
Эластичный пластик поролон имеет до 50—70% открытых пор. Его получают при использовании алифатических кислот с длинной углеродной цепью между карбоксильными группами (например себациновая кислота) и алифатических изоцианатов. При избытке полиэфира пластик сохраняет свои эластичные свойства. При избытке изоцианата получается твердый полимер трехмерного строения. В последнее время предложено применять фторированные полиуретаны, обладающие высокой стабильностью свойств. Пенопласт можно наносить при помощи распылительного пистолета с двойным питанием. Две жидкости (полиэфирная смола и изоцианат) подаются по шлангам к пистолету, в котором жидкости двигаются раздельно. Например, по внутреннему соплу подается изоцианат и по кольцевому соплу —смола.
В промышленности получают полиуретаны различных типов с разными свойствами — от мягких до жестких. Они широко используются для выработки пленочных материалов, поролонов (пенистые пластики), синтетических материалов. [c.277]
Пенополиуретаны могут быть эластичными и жесткими, причем эластичный пенополиуретан, называемый обычно поролоном, применяется наиболее часто. Поролон — это губчатая масса с очень малым удельным весом (0,03—0,06 г см ), высокими диэлектрическими свойствами, хорошими механической прочностью и сопротивляемостью истиранию, высокими термо- и звукоизоляционными свойствами и химической стойкостью. [c.50]
В УГНТУ выполнен цикл детальных исследований процесса нефтесбора с помощью ряда сорбентов с целью сопоставления свойств различных потенциальных сорбентов растительного происхождения при сорбции нефти и нефтепродуктов, в частности сорбентов на основе соломы, камыша, опилок, торфа, шелухи гречихи, мха, а также специализированных сорбентов для сбора нефти Пит Сорб» фирмы Клон Инк. (ФРГ) и Лессорб , представляющих собой мелкоиз-мельченный торф, подвергнутый специальной обработке. Одновременно был испытан ряд потенциальных поглотителей промышленного происхождения пенопласт полистирольный (гранулы), полипропилен (гранулы), каучуковая (резиновая) крошка, карбамидформальдегидная и фенолформальдегидная смолы, поролон, синтепон,, нетканый материал (лавсан),
Указанные свойства пенополиуретана позволяют его применять в качестве амортизационного (упругого) материала вместо пружин и набивочного материала, вместо ваты и пера в авиационной, автомобилестроительной, вагоностроительной и мебельной промышленности как теплоизоляционный и звукоизоляционный материал в судостроении, машиностроении, при строительстве зданий общественного и специального назначения, а также заменять мех и вату при изготовлении теплой и легкой одежды. Широко используют поролон для изготовления ковриков, губок и различных игрушек.

Некоторые полимерные материалы, полученные методом полимеризации, и их свойства. Полимеры, полученные методом полимеризации, выпускаются в виде крошки-для последующей переработки (литье, экструзия или выдавливание), в виде изделий — трубы различного сортамента, листов различной толщины, пленки. При добавлении газообразующих веществ в процессе переработки [ (N1-14) 2СО3] можно получить пористые материалы различного типа (поролон, мипора и т. д.). Эти материалы обладают очень малой объемной массой и используются как тепло- и звукоизоляторы. В зависимости от назначения их выпускают проницаемыми или непроницаемыми для газов это зависит от формы и расположения пор в самом материале. Помимо применения в качестве изолирующих материалов некоторые из них, например пенополистирол, используют в маши- [c.480]
Очень удобен в пользовании мягкий респиратор малого веса У-2К (рис. 29,6). Полумаска его выполнена из мягкого фильтрующего материала и покрыта слоем поролона. Внутренняя часть полумаски выполнена из полиэтиленовой пленки, обеспечивающей хорошие гигиенические свойства респиратора. Последний имеет два вдыхательных клапана, расположенных на внутренних боковых поверхностях, и выдыхательный клапан, находящийся в передней части. Респиратор У-2К задерживает 99,9% пыли, содержащейся во вдыхаемом воздухе. [c.120]
В Харьковском отделении ВНИИ ВОДГЕО были проведены исследования по доочистке биологически очищенных сточных вод на фильтрах, в которых в качестве загрузки использовался гранулированный синтетический материал —пенополиуретан (поролон). Характерными особенностями поролона помимо его малого объемного веса 0,028— 0,045 г/см и высокой пористости 90—92% являются его упругость и эластичность, а также высокие сорбционные и адгезионные свойства. [c.206]
Упругость и эластичность позволяют сжимать поролон, изменяя конфигурацию и уменьшая как пространство между гранулами, так и размеры пор в самих гранулах, и таким образом добиваться увеличения способности поролона задерживать более мелкие частицы взвешенных веществ, т. е. повышения эффективности очистки сточных вод. Эти же свойства позволяют при промывке, предварительно сняв напряже-. ние, расширить поролон и его поры, в результате чего задержанные, вещества легко и быстро вымываются. Загрузка фильтров состоит из гранулированного поролона с размером гранул 4—6 и 9—11 мм. Высота слоев загрузки 1м. [c.206]
Хорошие амортизационные свойства поролона и его сравнительная дешевизна позволяют с успехом применять его для упаковки легко бьющихся предметов, точных инструментов, приборов и даже… яиц. [c.136]
Новой областью применения поролона является ею использование для утепления одежды. Тонкий слой поролона, проложенный между двумя слоями ткани, великолепно защищает человека от холода, не мешая в то же время дышать коже. По теплоизолирующим свойствам поролон превосходит шерсть и даже прославленный гагачий пух. Он применяется для утепления летних комбинезонов, дамских шуб из искусственного меха (который изготовляется из полиамидов), теплых спальных мешков для полярников, штормовой одежды для моряков и альпинистов.
Процесс укрупнения капель воды на поверхности коагулирующей перегородки можно значительно улучшить, если в качестве наружного слоя применять эластичный полиуретан (поролон), обжатый перфорированным каркасом. Это объясняется тем, что поролон имеет высокоразвитую структуру с высокими гидрофобными свойствами, и капли воды после выхода из коагулирующей ступени накапливаются в порах поролона, где дополнительно укрупняются.н периодически выталкиваются потоком нефтепродукта. Преимуществом поролона является также то, что на этом материале не адсорбируются содержащиеся в нефтепродукте присадки и ПАВ, оказывающие отрицательное влияние на процесс укрупнения капель при использовании хлопчатобумажного чехла- Выбор материалов для водоотталкивающей перегородки ограничен требованиями, согласнр которым материал должен обладать гидрофобными свойствами и в то же время хорошо смачиваться нефтепрюдуктом. Для придания материалу указанных свойств его пропитывают каким-либо водоотталкивающим раствором. [c.100]
Так, весьма селективным сорбентом по отношению к хлор- и фосфорсодержащим пестицидам, ПХБ, ПХДД, ПХДФ и ПАУ жляется пенополиуретан (ППУ) плотностью 0,021 г/см , известный в быту как поролон. Он относительно дешев, прост в изготовлении, легко меняет свою форму и позволяет производить пробоотбор с высокой скоростью. Малолетучие ХОС почти полностью задерживаются ППУ, в то время как достаточно летучие вещества, например альдрин, сорбируются лишь на 50%. Фосфорсодержащие пестициды поглощаются ППУ на бб-вб /о, а ПХБ — на 70-85%. Блок из пенополиуретана толщиной 15 см способен полностью поглотить примеси ПХБ из 2700 м [32-35]. Для отбора гфоб воздуха на содержание ПХБ в индустриальных зонах используют и ам-берлит ХАО-2 [36,37]. Подобно пенополиуретану и ХАВ-2, хорошими сорбционными свойствами по отношению к ХОС обладают тенакс ОС, хромосорб 102, порапак Я [7]. Подтверждением высокой эффективности указанных сорбентов служат данные, представленные в табл. 5.3, [c.177]
Некоторые полимерные материалы, полученные методом полимеризации, и их свойства. Полимеры, полученные методом полимеризации, выпускаются в виде крошки для последующей переработки (литье, экструзия или выдавливание), в виде изделий — трубы различного сортамента, листов различной толщины, пленки. При добавлении газообразующих веи1,еств в процессе переработки [(ЫН гСОз], можно получить пористые материалы различного типа (поролон, мипора и т. д.). Эти материалы обладают очень малой объемной массой и используются как тепло- и звукоизоляторы. В зависимости от назначения их выпускают проницаемыми или непроницаемыми для газов это зависит от формы и расположения пор в самом материале. Помимо применения в качестве изолирующих материалов некоторые из них, например пенополистирол, используют в машиностроении из них делаот модели для отливки стали и других металлов — литье по газифицируюш имся моделям.

Для изготовления касок- (ее составных частей) применяют различные пластмассы, искусственную кожу, репсовую, капроновую или шелковую ленту (тесьму), поролон. Для производства корпусов используют пластические материалы полиэтилен низкого давления акри-лонитрилбутадиенстирол (пластик АБС), слоистый пластик типа текстолита, винипласт, стекловолокнистый пластик дев, пресс-материал АГ-4С. Корпуса, выполненные из полиэтилена низкого давления и пластика АБС, отличаются легкостью, хорошей устойчивостью к агрессивным химическим средам, имеют стабиль ные прочностные свойства в интервале температур от 40 до минус 25°С. Применяемые текстолит и стеклонаполненные материалы обладают большой прочностью, а также морозо- и теплостойкостью по сравнению с полиэтиленом, НО имеют большую массу. Внутреннюю оснастку изготавливают из полиэтилена высокого давления, хлопчатобумажной, репсовой или капроновой тесьмы.. [c.115]
В СССР серийно выпускаются антивибрационные рукавицы (ГОСТ 12.4.010-75 ТО 78-349-75) с внутренним карманом наладонной части для вибрационного вкладыша из поролона толщиной 8-10 мм и наладонником из износоустойчивой ткани [146]. Однако поролон пригоден для ручного механизированного инструмента, работающего при небольших нагрузках. При работе тяжелых молотков (рубильных, отбойных), когда на рукоятку оказывается большое давление, материал сжимается и его виброзащитные свойства снижаются. В таких случаях применяют специальный материал-пеноэласт, вспененный материал на основе поливинилхлорида, модифицированного нитрильным каучуком [147]. [c.115]
Другой метод получения полимерных материалов с высокоразвитой поверхностью заключается в термической обработке полимера, содержащего вещества, которые при нагревании выделяют газы (получение поропла-стов). Но такие материалы используются не как полимерные сорбенты, а как теплоизоляторы или механические амортизаторы (например, поролон). Высокоразвитая поверхность и пористость полимеров используется для проведения процессов сорбции преимущественно в ионообменных материалах, которые синтезируются в виде сшитого полпмера среде инертного разбавителя, что обеспечивает фиксацию рыхлой структуры. Соответствующий выбор мономеров или последующая химическая модификация позволяют придать такому материалу ионообменные свойства, а высокая пористость способствует хорошей доступности обрабатываемой жидкости к активным группам полимера, на которых разыгрывается процесс хемосорбции. [c.15]
Эластичность, способность самовентилироваться , негорючесть, абсолютная безвредность для человеческого организма — эти свойства поролона делают егс незаменимым материалом для изготовления мягкой мебели, матрацев, подушек, ковров, спальных мешков, одеял, мягких стелек для обуви и тысяч других предметов. Ряд мебельных предприятий Москвы и Ленинграда приступил к выпуску мягкой мебели с использованием поролона вместо пружинных подушек. [c.168]
Кроме отечественных пластмасс, в продажу поступают изделия на основе иностранных пено- и поропластов немецкого мольто-прена и норвежского поролона. При понижении температуры они несколько теряют свои эластичные свойства, которые потом вновь восстанавливаются горят слегка коптящим пламенем, не растворяются в бензине. По внешнему виду они напоминают искусственную губку с сообщающимися ячейками размером от 0,5 до [c.54]
Среди вспененных пластмасс особое место занимают эластичные пеномате-риалы с высоким относительным удлинением, достигающим 300—400% [8]. Подобные материалы (поролоны) были синтезированы в начале 50-х годов и к настоящему времени получили широкое распространение [9]. Незначительная кажущаяся плотность поролона (30—40 кг/м ), хорошие теплоизоляционные свойства, воздухопроницаемость, стойкость к маслам, бензину и другим веществам позволяют применять его качестве амортизационного, тепло- и звукоизоляционного материала, заменителя утеплителей в зимней одежде и т. д. [10]. [c.180]
Главные показатели качества поролона.
Характеристики поролона.
В данной статье мы собрали технические характеристики, виды и обозначения паралона.
Виды поролона: ST — стандартная марка; EL — повышенная жесткость; HL – жесткий; HS — мягкий и супермягкий; HR — высокоэластичный. Обозначение марки поролона: латинскими буквами обозначается тип, первыми двумя цифрами – плотность, следующими двумя цифрами – жесткость. Например: обозначение поролона EL 2540, где EL — повышенная жесткость, плотность поролона – 25 кг / м³, уровень жесткости – 4.
Главные показатели качества поролона.
Плотность
Одним из основных показателей качества поролона является плотность. Причем чем выше плотность, тем длиннее эксплуатационные сроки. Плотность указывает на количество поролона в единице объема. А так как в поролоновых ячейках есть еще и воздух, то этот показатель называют «кажущаяся плотность».
Но не следует думать, что плотность материала влияет на его жесткость — на мягкость этот показатель совсем не действует. Напротив, мягкий поролон может быть даже с большей плотностью. Более того, сроки эксплуатации поролона прежде всего зависят от его плотности: чем значительнее плотность, тем более долгий срок этот материал будет воспринимать нагрузки не деформируясь.
На заметку: поролон для спальных мест должен иметь плотность не ниже 25 кг / м².
Напряжение при сжатии.
Этой величиной характеризуется жесткость поролона и свидетельствует о том, какая сила в кПа может быть приложена к участку поролона, для сжатия его на 40%. Традиционно напряжение при сжатии и плотность являются основными характеристиками марки поролона. К примеру, марка поролона ST 2534 характеризуется напряжением сжатия 3,4 кПа.
Прочностные показатели.
Прочностные показатели в данном случае — это предельная прочность при разрыве и сравнительное удлинение при разрыве. Первый сообщает о величине силы, необходимой для разрыва поролона. Второй показатель говорит об относительной (по отношению к первоначальной) длине растяжения поролона до момента разрыва. Например, показатели для поролона ST 2534 обычно выражаются пределом прочности при разрыве 130-140 кПа и относительным удлинением при разрыве 220-280 %.
Эластичность поролона.
Эластичность поролона определяется высотой отскока особого шарика после свободного падения на поролон с определенной высоты. Естественно, более жесткий поролон не спровоцирует сильный отскок шарика.
Величина остаточной деформации.
Величину остаточной деформации поролона считают одним из самых главных показателей качества материала, характеризующего его способность сберегать свою форму и размеры в процессе использования. Для того чтобы определить остаточную деформацию образец поролона сдавливают вдвое и оставляют в таком положении на некоторое время, при условии что температура и влажность воздуха имеют определенное значение. После этого производят замеры размеров поролона и выявляют величину отклонения от заданных параметров. Ра-зумеется, для изготовления сидений нельзя использовать поролон с высокой остаточной деформацией. Очевидно также что более высокая плотность поролона соответствует его меньшей остаточной деформации.
Степени комфортности поролона.
Показатель комфортности определяется коэффициентом комфорта и коэффициентом опоры. Первый характеризуется приятным осязанием на ощупывание и мягкость поролона при небольшом сжатии, а второй способностью поролона удерживать и равномерно распределять усилие от груза, помещенного сверху.
Подытоживая вышесказанное, можно отметить, что выбор поролона должен полностью зависеть от его будущего функционального назначения, а не от стоимости, так как использование неподходящего поролона может в разы сократить время эксплуатации мебели. Кроме того, хороший поролон отличается высокими показателями эластичности, прочности и удлинения при разрыве и низкой остаточной деформацией.
Марки.
Для того чтобы обеспечить максимальную комфортность своей продукции изготовители матрацев и мягкой мебели часто применяют технологию многослойности: для верхнего настилочного слоя применяется поролон с высоким коэффициентом комфорта, а для нижнего – с высоким коэффициентом опоры.
1620. Данной маркой поролона открывается линейка мягких пен. Эта марка поролона является наиболее легкой и наименее долговечной, ее чаще всего используют как упаковку или для изготовления таких мебельных элементов, которые подвергаются небольшим нагрузкам. Кроме этого, поролон 1620-й прекрасно подходит для отделки задних и боковых поверхностей диванов и кресел.
2036, 1930, 1820. Все эти марки поролона сходны между собой. Они обладают большей долговечностью и лучшими физико-механическими характеристиками, чем 1620-я марка. Однако низкая плотность и сравнительно большие потери свойств во время динамических нагрузок не позволяют использовать данные марки для производства мебельных сидений, предусмотренных для длительной эксплуатации. Они прекрасно подходят для изготовления различных элементов недорогой мебели: подушек, подголовников, спинок, сидений и т.д. При этом марка 1820я больше подходит для производства спинок, а марка поролона 2036-я – для изготовления мебельных сидений.
2336, 2310. Эти марки поролона имеют различия как по жесткости, так и по эластичности. Причем 2310я марка намного мягче и эластичнее, чем 2336-я. Данные марки поролона выносливее, чем поролон предшествующей группы, хотя невысокая плотность все равно накладывает ограничения на срок их эксплуатации и соответственно, сферу использования.
Подобные материалы прекрасно подходят для производства мягких деталей подростковой и детской мебели, а также мебели для взрослых (при нагрузке 60 — 80 кг) с ограниченным эксплуатационным сроком. 2336-я и 2310я марки поролона хорошо зарекомендовали себя, как смягчающие слои мягких элементов пружинных блоков.
Но больше всего 2336-й подходит для производства деталей подголовников и спинок. Причем для того чтобы повысить комфортность элементов мебели лучше всего сочетать эту марку с 2310-й. Подобная комбинация значительно увеличит фактор комфортности и показатели эластичности изделия. В общем, марку 2310 не советуют применять для производства несущих элементов целиком. Гораздо лучше ее сочетать с более жесткими и плотными марками поролона.
2536, 2516. Эксплуатационные свойства этих марок намного превосходят характеристики марок поролона 2336 и 2310.
Марка 2536 — одна из самых популярных на российском мебельном рынке. Ей свойственна низкая остаточная деформация и достаточная эластичность при доступной стоимости.
2545, 2345, 2240. Данные марки ППУ представляют собой пены с повышенной жесткостью. Их можно применять для того, чтобы увеличить несущую способность сидений, подголовников, спинок и матрасов. Марки этого поролона не отличаются такой же комфортностью и эластичностью, как марки поролона 2536, 2336, следовательно, их лучше применять для производства внутреннего слоя комбинированных элементов. Марка 2240 также хорошо подходит для использования как упаковочный материал.
4050, 3540, 3530, 3040. Марки ППУ 3540, 3040, 4050 являются пенами с повышенной жесткостью, а марка ППУ 3530 причисляется к мягким пенам.
Подобные марки ППУ отличаются большими сроками службы и несущей способностью, идеально подходящей для производства матрасов и сидений. Марки ППУ, плотность которых 30 кг/м3 и выше, чаще всего применяются для мебельного производства в странах Евросоюза. Эластичные и комфортные материалы этой группы устойчивы к размягчительным процессам и прекрасно сохраняют размеры в процессе эксплуатации. Марка поролона 3040 рекомендуется для использования при изготовлении спинок, сидений, подлокотников и матрасов, которые рассчитаны на нагрузочное воздействие до 80 кг, а марка ППУ 3540 подходит для изделий, функционирующих при нагрузках до 100 кг.
Марки ППУ 3530 и 4050 являются одними из самых эластичных и комфортных. Высокая несущая способность и выдающаяся долговечность марки поролона 4050 позволяет использовать ее для производства элементов мебели, эксплуатирующихся в самых суровых условиях. К этой категории можно отнести, прежде всего, офисную мебель и мебель, используемую в различных общественных помещениях. Элементы из ППУ марки 4050 могут с успехом применяться при нагрузке 80-120 кг. Марка поролона 3530 – намного мягче. Она хорошо комбинируется с другими вариантами данной группы или используется отдельно, если нагрузка не превышает 80 кг.
Пены высокоэластичные 3535 и 3020. В этих материалах объединились преимущества мягких ППУ (с высокой эластичностью и небольшой начальной жесткостью) и преимущества пен высокой жесткости (с высокой несущей способностью и непрерывной поддержкой тела при лежании или сидении). Индекс комфортности подобных пен значительно превышает показатели проанализированных ранее марок ППУ. Высокоэластичные пены, плотность которых выше 30 кг/м3, прекрасно подходят для изготовления цельных мягких элементов мебели без применения комбинирования.
Марку ППУ 3020 можно применять для изготовления матрасов или спинок с расчетной нагрузкой до 60 кг, а марку поролона 3535 — для производства матрасов и сидений нагрузкой до 80 кг.
Преимущества
работы с нами
Широкий ассортимент изделий и привлекательные цены
Быстрая и качественная реализация продукции
Гибкие финансовые условия
Качественное сервисное обслуживание
Сделать заявку
на продукцию
По телефонам
+7 (812) 409-90 98+7 (499) 348-96-98
По почте
По форме
Оставить заявку
Сделать заказ
Заполните форму и наш специалист свяжется с вами в кратчайшие сроки и подготовит индивидуальное предложение
Пенополиуретан плотность 30 кг/м3
Листовой поролон 30 плотности толщиной 100 мм.Поролон — именно так называют в народе эластичный пенополиуретан. Слово прижилось в русском языке, благодаря популярному названию скандинавской фирмы Porolon, которая поставляла пенополиуретан в СССР.
Поролон или ППУ представляет из себя мягкую полиуретановую пену с мелкоячеистой структурой и уникальными качествами:
— Состоит на 90% из воздуха.
— Обладает отличной воздухопроницаемостью.
— Высокоэластичный. После применения некоторой силы способен полностью восстанавливать форму и размер. Величина нагрузки, после которой не бывает необратимых деформаций, зависит от жесткости и плотности поролона.
— Стойкий к перепадам температуры. Разрушается только при температуре замерзания в среде с повышенной влажностью. Замерзшая вода, разрушает ячейки пены. Без присутствия избыточной воды, поролон без труда выдерживает низкие и высокие значения температуры. При этом при уменьшении температуры эластичность ухудшается, а при повышении, восстанавливается.
— Температура при которой поролон загорается 255 гр. Цельсия. При нагревании до критической температуры, поролон сначала плавится, а затем загорается.
— Не портится от влияния ультрафиолета. Долгое воздействие солнечного излучения приводит к изменению цвета, но не отражается на его эксплуатационных свойствах. Под действием ультрафиолета, ячейка поролона, наполненная воздухом, насыщается озоном и в итоге меняет цвет.
— Отличный звукопоглощающий материал. Благодаря полуоткрытой форме ячеек, звуковые волны, часто сталкиваясь с перегородками ячейки, стихают и утрачивают силу.
— Безопасный и экологичный материал. Поролон при использовании не выделяет в атмосферу никаких вредных веществ. Он имеет стабильную химическую структуру (полиуретан) все полимеризационные процессы закончены. Не является источником пыли, не покрывается плесенью. Безопасность подтверждена многочисленными исследованиями и повсеместным использьванием поролона по всему миру.
— Низкое влагопоглощение, значительно меньшее, чем у ваты. При этом поролон быстро теряет влагу при сушке, абсолютно не изменяя своих свойств и параметров.
— Низкая теплопроводность поролона позволяет использовать его, как эластичный утеплитель.
Плотность поролона 30 кг/м3 используется только в дорогой элитной мягкой мебели и матрасах. Поролон до сих пор является лучшим материалом по соотношению цена — качество для мягкой мебели. Главное грамотно выбрать его плотность. Для спинок, подголовников и подлокотников достаточно 25 кг/м3, а для сидений 30-35 кг/м3.
Тонкий пенополиуретан плотность 30 кг/м3
Листовой поролон 30 плотности толщина 30 мм.Поролон — часто так называют в народе эластичный пенополиуретан. Слово прижилось в русском языке, благодаря популярному названию скандинавской фирмы Porolon, которая привозила пенополиуретан в СССР.
Поролон или ППУ представляет из себя мягкую полиуретановую пену с мелкоячеистой структурой и уникальными свойствами:
— Состоит из воздуха на 90%.
— Обладает прекрасной воздухопроницаемостью.
— Очень эластичный. После воздействия определенной силы способен полностью восстанавливать форму и размер. Значение нагрузки, после которой не бывает невозвратимых деформаций, зависит от жесткости и плотности поролона.
— Устойчивый к перепадам температуры. Разрушается обычно только в условиях низкой температуры в среде с повышенной влажностью. Вода при замерзании, разрушает ячейки пены. Без присутствия избыточной воды, поролон легко выдерживает низкие и высокие значения температуры. При уменьшении температуры эластичность уменьшается, а при повышении, восстанавливается.
— Температура при которой поролон загорается 255 гр. Цельсия. При нагревании до критической температуры, поролон сначала плавится, а затем загорается.
— Не разрушается от действия ультрафиолетового излучения. Долгое воздействие солнечного света приводит только к изменению его первоначального цвета, но не отражается на его рабочих свойствах. Под воздействием ультрафиолета, ячейка поролона, заполненная воздухом, насыщается озоном и в итоге просто меняет цвет.
— Отличный противошумный материал. Благодаря ячейкам полуоткрытого типа, звуковые волны, многократно ударяясь со стенками ячейки, угашаются и теряют силу.
— Экологичный и безопасный материал. Поролон при эксплуатации не источает в окружающую среду никаких ядовитых веществ. Он имеет неизменную химическую структуру (полиуретан) все полимеризационные процессы закончены. Не дает пыли, не покрывается плесенью. Безопасность подтверждена многочисленными испытаниями и долгой эксплуатацией поролона по всему миру.
— Небольшое влагопоглощение, значительно меньшее, чем у ваты. При этом поролон легко теряет влагу при сушке, совершенно не меняя своих свойств и параметров.
— Низкая теплопроводность поролона позволяет использовать его, как эластичный утеплитель.
Тонкий мебельный поролон высокой плотности 30 кг/м3
Поролон — часто так называют в народе эластичный пенополиуретан. Слово прижилось в русском языке, благодаря популярному названию скандинавской фирмы Porolon, которая привозила пенополиуретан в СССР.
Поролон или ППУ представляет из себя мягкую полиуретановую пену с мелкоячеистой структурой и уникальными свойствами:
Состоит из воздуха на 90%.
Обладает прекрасной воздухопроницаемостью.
Очень эластичный. После воздействия определенной силы способен полностью восстанавливать форму и размер. Значение нагрузки, после которой не бывает невозвратимых деформаций, зависит от жесткости и плотности поролона.
Устойчивый к перепадам температуры. Разрушается обычно только в условиях низкой температуры в среде с повышенной влажностью. Вода при замерзании, разрушает ячейки пены. Без присутствия избыточной воды, поролон легко выдерживает низкие и высокие значения температуры. При уменьшении температуры эластичность уменьшается, а при повышении, восстанавливается.
Температура при которой поролон загорается 255 гр. Цельсия. При нагревании до критической температуры, поролон сначала плавится, а затем загорается.
Не разрушается от действия ультрафиолетового излучения. Долгое воздействие солнечного света приводит только к изменению его первоначального цвета, но не отражается на его рабочих свойствах. Под воздействием ультрафиолета, ячейка поролона, заполненная воздухом, насыщается озоном и в итоге просто меняет цвет.
Отличный противошумный материал. Благодаря ячейкам полуоткрытого типа, звуковые волны, многократно ударяясь со стенками ячейки, угашаются и теряют силу.
Экологичный и безопасный материал. Поролон при эксплуатации не источает в окружающую среду никаких ядовитых веществ. Он имеет неизменную химическую структуру (полиуретан) все полимеризационные процессы закончены. Не дает пыли, не покрывается плесенью. Безопасность подтверждена многочисленными испытаниями и долгой эксплуатацией поролона по всему миру.
Небольшое влагопоглощение, значительно меньшее, чем у ваты. При этом поролон легко теряет влагу при сушке, совершенно не меняя своих свойств и параметров.
Низкая теплопроводность поролона позволяет использовать его, как эластичный утеплитель.
Мы продаем поролон только высочайшего качества, производства самарского поролонового завода. По своим свойствам он был признан в 2012 году лучшим товаром года, а в 2014 году заслужил национальный знак качества.
Самая лучшая плотность мебельного пенополиуретана — 30 кг/м3. Используется при производстве и ремонте мебели, изготовлении матрасов, стульев, кресел. Поролон до сих пор является лучшим материалом по соотношению цена — качества для мягкой мебели. Основное это правильно выбрать его плотность. Для спинок, подголовников и подлокотников достаточно 25 кг/м3, а для сидений 30-35 кг/м3.
Режем поролон любого размера, звоните!!!
Требования к температуре для обработки литых полиуретановых систем
Литые полиуретаны перерабатываются в жидком состоянии. То есть отдельные компоненты системы перед смешиванием разжижают, а затем отливают в форму или выливают на поверхность, чтобы дать отверждению перейти в твердое состояние.
После завершения первоначального отверждения в форме изделия можно перенести на стадию пост-отверждения для завершения реакции и достижения желаемых свойств. На рисунке ниже показаны этапы процесса литья полиуретана.
Условия обработки оказывают значительное влияние на конечные свойства литого полиуретана, независимо от системы. Два технологических параметра, которые имеют решающее влияние на характеристики систем полиуретан / мочевина, — это температура и соотношение форполимера и отвердителя. Количество отвердителя, необходимое для соответствия стехиометрии форполимера, обычно выбирается для улучшения определенного набора свойств (например, прочности на разрыв, сопротивления разрыву и истиранию и т. Д.) И должно соблюдаться в процессе дозирования и смешивания.
В этом блоге мы рассмотрим требования к температуре для эффективной работы с отвердителями, такими как диолы, диамины, а также с продуктами, используемыми в качестве удлинителей цепи и отвердителей в системах полиуретан / мочевина.
Твердые отвердители, используемые в литых полиуретановых системах
Во многих литых полиуретановых системах используются твердые отвердители, такие как MOCA, MCDEA, HQEE и HER, и эти отвердители необходимо плавить и обрабатывать в жидком состоянии. Ниже приведены температурные требования, которым необходимо следовать для этих удлинителей цепи.
Системы, отвержденные MOCA
MOCA — широко используемый отвердитель в процессе горячего литья, особенно с форполимерами TDI. Он обеспечивает полимеры с превосходными свойствами сохранения свойств при высоких температурах и хорошими динамическими характеристиками. По сравнению с другими диаминовыми лечебными средствами, такими как MBOEA, MCDEA и DETDA, MOCA демонстрирует более низкую реакционную способность и более длительный срок службы. См. Таблицу ниже.
Температура плавления MOCA составляет 98–102 ° C (208–216 ° F). Соответственно, номинальная рабочая температура расплавителя MOCA должна составлять от 110 до 120 ° C (230–248 ° F).Поскольку MOCA разлагается при воздействии более высоких температур, избегайте нагревания MOCA выше 125 ° C (257 ° F).
Системы, отвержденные MCDEA
MCDEA — это превосходный твердый ароматический диаминный отверждающий агент для высокоэффективных полиуретановых литых материалов. Он обеспечивает улучшенные динамические механические свойства и низкий гистерезис. Составы на основе MCDEA обычно обладают хорошей стойкостью к истиранию, хорошей эластичностью и прочностью на разрыв, а также хорошими технологическими характеристиками. Обычно эти свойства ценны для промышленных колес и шин, колес и роликов для спортивных и развлекательных парков, промышленных роликов и конвейерных лент.
Температура плавления MCDEA составляет 87–90 ° C (189–194 ° F). Соответственно, номинальная температура обработки для MCDEA должна составлять 95–110 ° C (203–230 ° F), обычно 100 ° C (212 ° F). MCDEA проявляет более высокую реакционную способность, чем MOCA. Следовательно, жизнеспособность систем MCDEA / TDI короче по сравнению с системами MOCA / TDI.
Системы отверждения HQEE
HQEE — это удлинитель цепи ароматического диола для систем преполимеров MDI, создающий полиуретановые эластомеры с превосходными динамическими свойствами, хорошим сопротивлением разрыву и высокой упругостью.Эластомеры серии HQEE / MDI могут соответствовать многим характеристикам систем MOCA / TDI. Применения эластомеров MDI / HQEE включают промышленные колеса и шины, колеса для спортивных и развлекательных парков, футеровки и покрытия труб, ролики, покрытия промышленных роликов, прокладки, уплотнения для нефтяных месторождений и другие высокоэффективные конечные применения.
Однако существуют трудности, связанные с переработкой HQEE из-за его высокой температуры плавления, ~ 98 ° C (~ 208 ° F), и того факта, что HQEE не переохлажден (HQEE будет быстро кристаллизоваться ниже своей точки плавления).Соответственно, важно равномерно нагреть и слегка перемешать HQEE в плавильном баке и предварительно нагреть форполимер до 90 ° C (194 ° F) или выше перед добавлением HQEE. Кроме того, все линии передачи HQEE должны быть нагреты до 110 ° C. (230 ° F) и изолирован, чтобы предотвратить появление холодных пятен, которые могут вызвать кристаллизацию HQEE в линиях и привести к неточному соотношению компонентов смеси. Температура формы должна быть 110 ° C (230 ° F) или выше, чтобы предотвратить дефекты литых деталей.
Еще одна технологическая проблема, с которой сталкивается HQEE в качестве удлинителя цепи, — это явление, называемое «врезанием в звездочку» на поверхности деталей.Это явление объясняется прекращением использования продукта реакции HQEE и свободного мономера MDI, особенно на поверхностях форм при температурах ниже 110 ° C (230 ° F). Сообщалось, что преполимеры MDI с низким содержанием свободного MDI проявляют гораздо меньшую тенденцию к образованию звездочек из-за более низкого содержания мономера свободного MDI.
В некоторых случаях другие диолы, такие как HER или PTMEG, могут быть добавлены в небольших количествах к HQEE для облегчения поддержания расплавленного состояния.
Системы HER-отверждения
HER является изомерным аналогом HQEE и еще одним удлинителем цепи ароматического диола для систем форполимеров MDI.Свойства преполимеров HER расширенного MDI сравнимы со свойствами HQEE. Однако HER имеет более низкую температуру плавления 89 ° C (192 ° F) и способность переохлаждаться, что дает значительные технологические преимущества по сравнению с HQEE: более низкие температуры обработки, более широкий диапазон температур обработки, отсутствие «звездочек» и меньшая склонность к кристаллизации в технологическом оборудовании. После плавления при 90–100 ° C (194–212 ° F) температура HER может быть снижена примерно до 80 ° C (176 ° F) без кристаллизации.
В уретановых эластомерах HER обеспечивает превосходные механические свойства; твердость; очень хорошая устойчивость к разрыву, порезам и истиранию; и хорошая отказоустойчивость. Применения такие же, как у HQEE, в том числе промышленные колеса и шины, спортивные колеса, штамповочные подушки и покрытия, ролики, покрытия промышленных валков, прокладки, уплотнения для нефтепромыслов, детали конвейеров и другие высокоэффективные конечные применения.
Жидкие отвердители, используемые в литых полиуретановых системах
Некоторые отвердители для литых полиуретановых систем находятся в жидком состоянии при комнатной температуре, но их вязкость может быть слишком высокой для эффективного смешивания с форполимером.В таких случаях обычно необходимо повысить температуру отверждения, чтобы снизить его вязкость. Ниже приведены температурные требования для некоторых жидких диаминовых и диольных отвердителей, используемых в литых полиуретановых системах.
Diamines
Некоторыми обычно используемыми жидкими ароматическими диаминовыми отвердителями являются DETDA, DMTDA, MBOEA и P-1000. Эти диамины обладают тем преимуществом, что позволяют обрабатывать их при более низких температурах. Однако известно, что отверждение при более высоких температурах может привести к повышению прочности на разрыв, а также устойчивости к разрыву и истиранию.DETDA и MBOEA демонстрируют очень высокую скорость отверждения и короткую жизнеспособность с форполимерами TDI. DMTDA имеет более низкую реакционную способность и показывает работоспособную жизнеспособность при 100 ° C (212 ° F), сравнимую с таковой у систем MOCA / TDI.
Смеси диаминовых отвердителей, такие как MBOEA с DETDA, могут снизить общую вязкость и улучшить текучесть при более низких температурах.
P-1000 представляет собой полимерный диаминный отверждающий агент, который представляет собой вязкую жидкость при комнатной температуре и проявляет гораздо более низкую реакционную способность в системах TDI; его также можно использовать в системах MDI.P-2000 представляет собой воскообразное твердое вещество при температуре окружающей среды с температурой плавления в диапазоне 18–23 ° C. Оба отвердителя выигрывают от обработки при более высоких температурах, при которых снижается вязкость.
Diols
Жидкие диоловые удлинители цепей, такие как 1,4-бутандиол (BDO) и 2-метил-1,3-пропандиол (MPO), могут использоваться в литых полиуретановых системах на основе MDI при комнатной температуре. Температура обработки и уровни загрузки катализатора влияют на жизнеспособность систем диол / МДИ. Некатализированные системы могут иметь жизнеспособность 10–20 минут при 70 ° C; однако обработка при более высоких температурах или использование катализаторов значительно сокращает жизнеспособность.
При обработке литых полиуретановых систем важно учитывать, что BDO замерзает при 20 ° C (68 ° F). Следовательно, его необходимо поддерживать выше точки замерзания, чтобы избежать кристаллизации в линиях оборудования и разделения фаз в составе на стороне B.
MPO — еще один жидкий удлинитель цепи первичного диола с температурой замерзания -54 ° C. Как изомер BDO, он имеет идентичную молекулярную и эквивалентную массу, что и BDO, но обеспечивает лучшую совместимость с преполимерами на основе сложного полиэфира и простого полиэфира.Следует отметить, что полученный эластомер будет более мягким по сравнению с эластомером, полученным с использованием BDO, и будет демонстрировать лучшую гидролитическую стабильность. Реактивность MPO лишь немного ниже, чем у BDO, и в процессорах использовались смеси BDO с MPO.
Если вы хотите приобрести эти лечебные средства или получить дополнительную информацию о том, как их правильно использовать, свяжитесь с Gantrade Corporation, чтобы получить опыт и поддержку нашей технической команды.Температурный диапазон полиуретана
Один из многих распространенных вопросов, которые мы часто получаем от дизайнеров продукции, — «Какой температурный диапазон может выдерживать полиуретан?».В зависимости от химического состава термореактивные полиуретаны обычно могут выдерживать широкий диапазон температур, в отличие от термопластов и резины. От арктических тундр до сухих жарких пустынь — этот настраиваемый материал часто может сохранять свою первоначальную форму и физические свойства даже в самых суровых условиях. Однако есть несколько условий, которые проектировщики должны учитывать при проектировании с использованием термореактивного полиуретана. В этом посте мы обсудим важность диапазона температур в вашем дизайне и то, как он может потенциально повлиять на производительность вашего продукта.
Диапазон температурСтандартные термореактивные полиуретаны обычно выдерживают температуры от -80 ° F до 200 ° F. Однако некоторые химические составы полиуретана могут иметь более высокую устойчивость к температуре, достигающую 300 ° F. За пределами этих температур термореактивные полиуретаны со временем будут ослабевать или разрушаться.
Рабочие температурыРабочие температуры обычно относятся к диапазону температур, который материал может выдерживать, успешно выполняя свою роль в работе.Другими словами, речь идет не только о том, чтобы выжить при такой температуре, но и о выполнении задачи при этой температуре. Таким образом, рабочие температуры будут определяться окружающей средой приложения, а также продолжительностью пребывания в этой среде. При выборе материала очень важно проверить физические свойства, которые не будут нарушены в ожидаемых условиях окружающей среды во время эксплуатации.
К счастью, термореактивные полиуретаны бывают разных форм и форм.В зависимости от химического состава основы материала разработчик часто может иметь возможность указать широкий диапазон рабочих температур. Например, полиуретаны на основе TDI обычно имеют более высокие диапазоны рабочих температур, чем полиуретаны на основе MDI. Возьмем, к примеру, Durethane XL. Этот мощный материал был разработан с поликарбонатной основой для работы в самых суровых условиях.
Высокие температурыКогда термореактивные полиуретаны подвергаются воздействию температур, превышающих допустимый диапазон, в течение длительных периодов времени, это часто может привести к следующим условиям:
- Ослабленные физические свойства
- Материал может вернуться в исходное состояние, стать липким
- Материал может гореть в зависимости от температуры и воздействия пламени
Применения с длительными рабочими температурами ниже -0 ° F могут привести к усилению уретана, изменяя физические свойства материала.Температура ниже -80 ° F сделает материал хрупким, что увеличит вероятность разрыва и / или разрыва.
ЗаключениеТермореактивные полиуретаны могут быть изготовлены по индивидуальному заказу для самых тяжелых условий эксплуатации. Из практически бесконечного диапазона физических свойств, включая двойной твердомер, проводимость, огнестойкость и / или стойкость к истиранию — мы можем сформулировать все это по индивидуальному заказу! Чтобы узнать больше о наших высокоэффективных материалах для повышения производительности, загрузите нашу спецификацию материалов здесь или щелкните баннер ниже:
Полимеры | Бесплатный полнотекстовый | Химия, обработка, свойства и применение резиновых пен
3.2. Тип каучуков
Характеристики отверждения и ячеистая структура, а также механические и физические свойства пен можно контролировать путем тщательного выбора типа резины. До сих пор сообщалось о различных пенопластах на основе NR, EPDM, полиизопренового каучука (IR), CR, бутадиенстирольного каучука (SBR), EVA, изобутиленового каучука (IIR), акрилонитрилбутадиенового каучука (NBR), полиуретана (PU), хлорированного полиэтиленовый каучук (CPE), силиконовый каучук (SR) и др. [93,94,95,96,97,98]. Сводка основных типов каучуков с их свойствами и молекулярной структурой представлена в таблице 1.Среди каучуков NR является основной матрицей для производства пен из-за его естественного происхождения (биологического происхождения), доступности, возобновляемости и соответствующих механических и электрических свойств [99]. Хорошие механические свойства включают высокие эластичные свойства, высокую упругость и демпфирующие свойства, высокую прочность на растяжение, низкую остаточную деформацию при сжатии, сопротивление разрыву и истиранию, но плохую химическую стойкость и способность к обработке [50,100]. NR имеет четыре возможных микроструктуры в своих молекулярных цепочках: цис-1,4-, транс-1,4-, 1,2- и 3,4-полиизопрен [101], но основным компонентом является цис-1,4-полиизопрен. .NR получают в латексе из таких деревьев, как Hevea brasiliensis (пара каучуковые деревья) и баньяновых фиговых деревьев (Ficus bengalensis) или различных растений, таких как куст гваюле (Parthenium argentatum Gray) и русский одуванчик (Taraxacum koksaghyz), но он содержит различные примеси (в основном белки, аминокислоты, фосфолипиды и компоненты геля) [102]. Стандартный малазийский каучук (SMR) подразделяет латекс NR на различные классы в зависимости от количества основных примесей (грязь, зола, азот, летучие вещества).Азотистые материалы в каучуке связаны с белками, что определяется по содержанию азота и может дать оценку содержания белка в каучуке [103]. SMR-L, SMR-5, SMR-10 и SMR-20 являются основными сортами NR, а основные примеси перечислены в Таблице 2. Другой важный сорт — это эпоксидированный натуральный каучук (ENR), который представляет собой химически модифицированный сорт полученного NR. путем эпоксидирования [104]. Присутствие эпоксидных групп на основной цепи увеличивает полярность NR, что приводит к более высокой скорости отверждения и лучшим конечным свойствам пен.Ariff et al. исследовали влияние различных марок NR на морфологические, механические и физические свойства пен NR [105]. Они использовали три различных сорта NR (SMR-L, SMR-10 и ENR-25: ENR с 25 мол.% Эпоксида). Их результаты показали, что обе немодифицированные марки (SMRL и SMR-10) не показали значительной разницы в размере ячеек, плотности сшивки (CLD), скорости расширения, скорости отверждения и механических свойствах из-за их сходной химической структуры [106]. С другой стороны, пены ENR-25 имели меньший размер ячеек, большую толщину стенок ячеек, более высокую плотность и лучшие механические свойства.Такое поведение объясняется тем, что эпоксидные группы на основной цепи ENR реагируют с центрами двойной связи углерода и увеличивают CLD. Xu et al. обнаружили, что механические свойства NR / диоксида кремния улучшились после добавления ENR [107]. Это улучшение было приписано реакции раскрытия кольца между эпоксидными группами ENR и группами Si-OH на поверхности диоксида кремния, которая улучшила дисперсию диоксида кремния в резиновой матрице и усилила межфазные взаимодействия между каучуком и диоксидом кремния (рис. 4).Salmazo et al. производили пенопласты SMR-L и ENR-25 отдельно в присутствии ADC и отверждали различными дозами облучения электронным пучком (50, 100 и 150 кГр) [108]. Их результаты показали, что пены ENR имели более высокую скорость зарождения клеток и меньшую деградацию клеток, чем пеноматериалы, полученные из одного SMR-L. Это было связано с присутствием эпоксидных групп в отвержденной пене ENR, способствующей более высокой степени отверждения. Следовательно, пены ENR имели более однородные пористые структуры и меньшие размеры ячеек.SBR — это синтетический каучук, полученный из нефти. Первоначально он разрабатывался как альтернатива NR. SBR получают сополимеризацией ~ 75% бутадиена (CH 2 = CH-CH = CH 2 ) и 25% стирола (CH 2 = CHC 6 H 5 ) [110]. Некоторые свойства SBR, такие как отличная остаточная деформация при сжатии, повышенная трещиностойкость, стойкость к истиранию, износостойкость и снижение стоимости, позволяют использовать его в промышленности благодаря улучшенным свойствам старения и теплоизоляции [111].Однако о пенах SBR сообщалось редко из-за их очень высокой вязкости и усадки [112]. Влияние типа CFA (OBSH и ADC) и содержания (0, 2, 4, 6, 8 и 10 phr) на характеристики отверждения, механические и морфологические свойства клеточного NR / SBR было изучено Wimolmala et al. [113]. Они сообщили, что 4 части на 100 частей были оптимальной концентрацией пенообразователя (как для OBSH, так и для ADC), но OBSH приводил к более высокой скорости отверждения (более низкому времени отверждения) по сравнению с ADC. Кроме того, увеличение содержания пенообразователя привело к более низкому упругому восстановлению и более высокой упругости пен NR / SBR.Shao et al. смогли снизить усадку пен SBR до 2,25% за счет использования серы и дикумилпероксида (DCP), создавая систему двойного сшивания [96]. Их исследование показало, что усадка в основном зависит от синергетического эффекта между обоими сшивающими агентами. Пенопласты SBR / RR (переработанный каучук) с различными соотношениями (100: 0, 80:20 и 60:40) были приготовлены с использованием бикарбоната натрия Algaily и соавторами [114]. Увеличение концентрации RR привело к лучшим механическим свойствам (более высокое удлинение при разрыве и предел прочности на разрыв), более высоким характеристикам отверждения (максимальный / минимальный крутящий момент и плотность сшивки) и более высокой плотности пены.Изменение соотношения RR: SBR привело к сдвигу резонансной частоты с 500 Гц (100: 0) на более высокую частоту 800 Гц (80:20 и 60:40). Бахадар и др. подготовили смесь EPDM / SBR, армированную одностенными углеродными нанотрубками (SWCNT), для применения в амортизаторах [115]. Введение SWCNT в матрицу EPDM / SBR привело к значительному улучшению модуля упругости (80%), но уменьшению модуля потерь на 27% для самого высокого протестированного содержания SWCNT (0,6 мас.%). Реологические исследования показали, что добавление SWCNT в каучуковую смесь увеличивает коэффициент потерь (tan δ = E ‘/ E ″), но снижает крутящий момент перемешивания.Деградация с увеличением соотношения наполнитель / матрица наблюдалась в отношении прочности на сжатие и эффективности поглощения энергии. Все эти эффекты были связаны с превосходной механической прочностью, более однородной дисперсией и длительным связыванием между матрицей и SWCNT. EPDM представляет собой ненасыщенный полиолефиновый каучук, полученный сополимеризацией этилена, пропилена и несопряженного диена (этилиденнорборнен, дициклопентадиен или 1,4-гексадиен), который обеспечивает сайты сшивания для вулканизации [116].Присутствие пропилена в основной цепи EPDM предотвращает образование кристалличности, чтобы поддерживать более высокое содержание аморфности. Отсутствие ненасыщенной двойной связи в основной цепи EPDM обеспечивает высокую стойкость к тепловому старению, химическую стабильность, устойчивость к озону, ультрафиолету и окислению, а также высокую нагрузочную способность и высокую устойчивость к разрушению во время [116,117]. EPDM привлекает большое внимание для наружных применений, таких как автомобильные уплотнительные системы, проволочные материалы, строительные профили, белые боковины шин, электро-электронные компоненты, кровельные листы и спортивные товары.Выбор подходящей системы вулканизации в сочетании с подходящим пенообразователем всегда был проблемой для пен EPDM из-за его низкой скорости вулканизации [118]. Путем смешивания EPDM с NR Льюис с соавторами обнаружили, что на структуру, свойства и характеристики отверждения пен EPDM / NR влияет количество NR в смеси [119]. Время подвулканизации и время отверждения уменьшались с увеличением содержания NR из-за высокой реакционной способности двойных связей и метильной группы, повышающей активность двойной связи в NR [120].Нанокомпозитные пенопласты EPDM / галлуазитные нанотрубки (HNT) были произведены с использованием периодического процесса в автоклаве с использованием scCO 2 как PFA Ли и соавторами [121]. Они достигли микроклеточной пены со средним размером ячеек 7,8 мкм и плотностью клеток 1,5 × 10 10 клеток / см 3 , показывая, что HNT действовал как эффективный зародышеобразователь для процесса вспенивания. Эта микропористая эластомерная нанокомпозитная пена потенциально может быть использована во множестве промышленных применений, включая прокладки и уплотнения для автомобильных и электрических корпусов.Suntako исследовала влияние синтезированных наночастиц ZnO методом осаждения в качестве активатора вулканизации серы по сравнению с обычным ZnO на характеристики отверждения и морфологию пен EPDM [122]. Было показано, что пены EPDM на основе синтезированных наночастиц ZnO демонстрируют более высокий предел крутящего момента, сжимающую нагрузку и твердость с увеличением содержания наночастиц, в то время как оптимальное время отверждения и время подвулканизации уменьшаются. Ячеистая структура пен EPDM была более сферической, и размер ячеек уменьшался с увеличением синтезированных наночастиц ZnO.Также было возможно уменьшить количество синтезированного ZnO с 5 до 3 частей на 100 частей на 100 (40%), потому что наночастицы ZnO имеют гораздо более высокие удельные поверхности. Ma et al. разработали композитные пенопласты EPDM с различными соотношениями SR для определения его влияния на износостойкость, структуру, отверждение, реологические и механические свойства смесей [27]. Значения крутящего момента и уровень отверждения были увеличены с концентрацией SR. Все механические свойства композитных пеноматериалов были улучшены при добавлении SR, за исключением удлинения при разрыве.Что еще более важно, износостойкость и остаточная деформация при сжатии существенно улучшались с увеличением содержания SR. Пенопласты из био-EPDM с различным соотношением наностержней из вольфрамовой бронзы (TBNR) были изготовлены для улучшения теплоизоляционных свойств для использования в высокофункциональных экологичных гидрокостюмах для дайвинга [123]. Задержка сшивания и стабилизация скорости вспенивания при добавлении TBNR контролировали рост пузырьков и индуцировали образование более мелких ячеек с более равномерным распределением по размерам.Также была улучшена технологическая стабильность пены, что привело к получению эластомерной пены с превосходной теплоизоляцией, гибкостью, эластичными свойствами и стабильностью пены без значительных изменений механических свойств. Кроме того, отличная фототермическая стабильность после светового облучения показала, что разработанный материал подходит для термо-функциональных гидрокостюмов при водных видах спорта и других видах активного отдыха. Пена EVA промышленно применяется в широком спектре продуктов, таких как подошвы и межподошвы для обуви, спортивное оборудование, изоляционные материалы. и системы доставки лекарств, потому что они очень прочные, очень удобные и мягкие [36].Однако некоторые недостатки, такие как высокая плотность и низкие физические свойства, ограничивали дальнейшее применение [28]. Чтобы преодолеть эти недостатки, Park et al. смешанный EVA с сополимером этилена-1-бутена (EtBC) для улучшения физических свойств пен EVA, включая прочность на разрыв, упругость при отскоке и остаточную деформацию при сжатии [124]. Kim et al. достигли низкой плотности, высокой упругости отскока и прочности на разрыв пен EVA (при оптимальной температуре сшивания) за счет смешивания с NR [125]. Случайное замещение атомов хлора на основной цепи PE приводит к его превращению из термопластичного материала в резиновый материал ( CPE) путем подавления кристаллизации.CPE обладает высокой устойчивостью к углеводородным маслам, теплу и атмосферным воздействиям из-за добавления атомов хлора к основной цепи PE [126]. Более того, наличие как неполярных групп (немодифицированных метиленовых звеньев), так и полярных групп (хлорированных метиленовых звеньев) в основной цепи CPE увеличивает его совместимость с полярными или неполярными полимерами для достижения определенных наборов свойств и ценовых преимуществ [127 ]. Чжан с соавторами приготовили серию пен для исследования влияния соотношения CPE / EVA на отверждение, пенообразование и механические свойства [128].Они обнаружили, что увеличение содержания EVA оказывает незначительное влияние на подвулканизацию и время отверждения, но получают более высокую твердость с более низкой упругостью отскока и коэффициентом усадки. Степень расширения и доля пустот увеличивались с увеличением содержания EVA, в то время как плотность клеток снижалась со 100: 0 до 50:50 CPE: EVA, а затем значительно увеличивалась с 70:30 до 90:10. Силикон (полиорганосилоксан) состоит из чередующихся атомов кремния и кислорода (силоксановые звенья) с боковыми углеводородными радикалами, непосредственно соединенными с кремнием [129,130,131].Характеристики связи Si-O-Si, большая длина связи (0,163 нм), угол связи (130 °) и энергия связи (445 кДж / моль) обеспечивают SR с превосходными эксплуатационными характеристиками, включая превосходную химическую стойкость, хорошую электрическую изоляционную способность, высокая эластичность, отличная термическая, ультрафиолетовая и озоновая стабильность, высокая стойкость к атмосферным воздействиям и очень низкая температура стеклования (T g ≈ -120 ° C), а также биосовместимость [132,133,134,135]. Пены SR сочетают в себе характеристики силиконового каучука и вспененных материалов, такие как хорошая упругость, высокая термостойкость, соответствие форме, низкая плотность и легкий вес [136].Пенопласты из силиконовой резины обладают повышенной температурной стабильностью (от –60 ° C до 250 ° C для длительного использования и до 400 ° C для краткосрочного применения), предлагая более широкий диапазон рабочих температур по сравнению с любыми другими вспененными материалами из органического каучука [137 ]. Луо и др. изготовили пенопласт из метилвинилсиликонового каучука с различными сферическими размерами ячеек путем физического вспенивания (с использованием сферической мочевины с разными размерами в качестве агента, формирующего ячейки), чтобы изучить взаимосвязь между размером ячеек и механическими свойствами [138].Они показали, что пена силиконового каучука со сферическими ячейками диаметром от 300 до 450 мкм демонстрирует очень хорошую прочность на сжатие и свойство релаксации напряжения сжатия. Liao et al. оценили влияние содержания кремнезема, температуры и давления на вязкоупругие свойства силиконовых резиновых смесей, приготовленных с использованием scCO 2 [139]. Согласно их результатам, концентрация диоксида кремния влияла как на зарождение клеток, так и на рост клеток, поскольку он действовал как гетерогенный агент зародышеобразования, а также увеличивал вязкость соединений SR.Кроме того, при снижении температуры насыщения (T s = 40 ° C) зарождение клеток было заметным из-за образования большого объема молекул CO 2 . Напротив, увеличение T s (60 ° C и 80 ° C) приводило к слиянию клеток, ассоциированному с быстрым ростом клеток (этап контроля). В целом они получили пенопласты SR с более низкой плотностью ячеек и большим размером ячеек при высоких температурах. Наконец, высокое давление насыщения привело к более высокому эффекту пластификации scCO 2 и более низкой вязкости матрицы SR, что привело к улучшенным скоростям роста клеток.Чен и его коллеги разработали напечатанные на 3D-принтере пенопласты SR с тримодальной пористостью, обеспечивающие выдающиеся свойства, многофункциональность и многомерную настраиваемость (рис. 5) [140]. Вязкоупругие чернила для печати получали простым смешиванием хлорида натрия (NaCl) с гелем-предшественником полидиметилсилоксана (PDMS). Иерархическая пористость, создаваемая выщелачиванием соли и удалением растворителя, позволила получить пенопласты из ПДМС с беспрецедентной гиперэластичностью, чрезвычайной сжимаемостью, циклической износостойкостью (почти нулевая необратимая деформация формы при экстремальном сжатии 90% деформации и 1000 циклов большого сжатия) и отличным растяжением. способность (максимальная нагрузка 210%).Пористая структура также работает как шероховатость поверхности, обеспечивая супергидрофобность. Модуль упругости, эластичность, способность к растяжению и способность впитывания масла регулировались с помощью рецептуры чернил или компьютерного рисования. Пены силиконового каучука (VMQ) в сочетании с химически восстановленным оксидом графена (rGO) и функционализированным 3-аминопропилтриэтоксисиланом графеном (FG) были получены Shi et al. оценить их реологическое поведение, структуру ячеек и механические свойства [141]. Наличие rGO повысило прочность матрицы в два раза, а FG увеличило ее в шесть раз.Основная причина — более сильное взаимодействие и отличная совместимость FG с VMQ. Повышенная прочность матрицы также ограничивала усадку стенок ячеек, что приводило к пенам VMQ / FG, имеющим больший размер ячеек по сравнению с пенами VMQ / rGO. Механические результаты показали, что FG может улучшить прочность на разрыв (130%) и удлинение при разрыве (140%) по сравнению с пенами VMQ / rGO. Легкие и гибкие полые стеклянные микросферы с покрытием SR / Ag (HGM) использовались для защиты от электромагнитных помех (EMI) в композитных пенопластах с градиентной структурой, полученной комбинацией индукции плотности и вспенивания scCO 2 [142].Композитные пенопласты имеют проводимость до 279,3 См / м при 0,51 об.% Ag и соответствующую эффективность экранирования от электромагнитных помех (SE), достигающую 30 дБ при толщине всего 0,7 мм. Многослойная структура пенопласта не только увеличивала EMI SE, но и не увеличивала отражение. Трехслойный композитный пенопласт показал средний EMI SE 59 дБ и коэффициент мощности отражения (значение R) 0,60 при толщине 2 мм. Превосходная устойчивость композитного пенопласта к EMI SE была получена благодаря хорошей гибкости матрицы SR.3.3. Тип и количество ускорителей
Для получения полезных свойств эластомеры необходимо вулканизировать. Несмотря на наличие различных процессов и систем сшивания, в резиновой промышленности обычно используются системы вулканизации серой или пероксидом для вулканизации резины [143,144,145,146]. Вулканизация каучука серой без ускорителей может длиться несколько часов, но в их присутствии реакции завершаются за несколько минут. Кроме того, добавление ускорителей снижает необходимое количество серы, что приводит к повышению стойкости к окислению [147,148].Для хорошего контроля ячеистой структуры и конечных свойств решающее значение имеет выбор подходящего типа и состава ускорителя. Другими словами, во время процесса отверждения время подвулканизации (время, необходимое при фиксированной температуре для начала образования сшивки) должно быть достаточно большим, чтобы предотвратить полную вулканизацию резины перед заполнением полости формы, но оно должно быть достаточно коротким. для увеличения производительности [149 150]. Вот почему скорость вулканизации играет важную роль, поскольку она влияет как на ячеистую структуру, так и на плотность сшивки конечных пен.Реакция отверждения эластомерных пен на основе серы и ускорителей очень сложна из-за большого количества одновременных реакций. До сих пор использовалось несколько ускорительных систем, но наиболее важные из них можно разделить на четыре группы в зависимости от их схемы реакции отверждения и химической структуры [151]. Во-первых, были разработаны анилин и тиокарбанилид (производные амина), но они больше не используются из-за их токсичности. Во-вторых, дитиокарбаматы и ксантаты имеют высокие скорости сшивания, но почти не имеют времени подвулканизации.Кроме того, сегодня наиболее широко используются бензотиазолы и сульфенамиды из-за их превосходных свойств подвулканизации. Наконец, тиурамы можно использовать как в качестве ультраускорителей, так и в качестве вулканизирующих агентов. Обычно ускоритель реагирует с серой с образованием мономерных полисульфидов, которые взаимодействуют с молекулами каучука с образованием полимерных полисульфидов, а также для сокращения времени, необходимого для вулканизации [ 152]. Структура, свойства и названия наиболее важных ускорителей приведены в таблице 3.Влияние сульфенамидного ускорителя (MBS, TBBS и CBS) на кинетику отверждения и свойства пен из натурального каучука исследовали Charoeythornkhajhornchai et al. [154]. Основная информация приведена в Таблице 4. Пены на основе CBS показывают самую высокую скорость вулканизации с самой низкой энергией активации, потому что CBS дает более высокий уровень основности аминов, чем любой другой ускоритель, образуя сложную структуру с ионами цинка в качестве лигандов в сере. вулканизация. Кроме того, высокая скорость отверждения CBS приводит к образованию пен с наименьшим размером пузырьков, наименьшим распределением пузырьков по размерам и наименьшей плотностью ячеек, что приводит к наименьшей теплопроводности и коэффициенту теплового расширения по сравнению с другими пенами.Несмотря на присутствие ускорителя, оксид цинка и жирная (стеариновая) кислота также добавляются для активации реакции вулканизации. Оксид цинка в сочетании с кислотой образует соль, повышающую эффективность ускорителя [155]. Ariff и соавторы исследовали влияние различного соотношения ускорителя между TMTD и CBS на свойства пен SMR-L / ENR-25 [156]. Результаты показали, что время индукции увеличивалось с увеличением соотношения CBS, поскольку CBS не является эффективным донором серы по сравнению с TMTD.Более высокое отношение CBS также привело к большему среднему размеру ячеек, более толстой стенке ячеек, более низкой степени расширения (более высокой относительной плотности) и более высокой остаточной деформации при сжатии. Напряжение при сжатии увеличивалось с увеличением отношения CBS, поскольку полученные пены сильно зависели от свойств матрицы и более высокой относительной плотности, то есть большего количества более прочного материала в стенках ячеек. Неопренпротив полиуретана: какой выбрать
Полиуретан состоит из нескольких или «поли» уретановых звеньев, которые связаны химической реакцией, называемой полимеризацией.Это превращает податливый материал в твердый и жесткий.
Неопрен также получают путем полимеризации, но на этот раз из хлоропрена.
Дороже ли полиуретан по сравнению с неопреном?
Сколько стоит полиуретан и неопрен, конечно, будет зависеть от вашего применения. Полиуретановый материал в твердом формате имеет высокую стойкость к истиранию и выдерживает некоторые агрессивные химические среды. Это особенно верно, когда требуется контакт с маслом или материалами на нефтяной основе.Следовательно, полиуретан будет иметь лучшие рабочие характеристики по сравнению с неопреном в этих средах. Однако он окажется чрезвычайно дорогим по сравнению с неопреном.
Области применения неопрена и полиуретана
Неопрен имеет подходящие качества и атрибуты в областях, требующих хорошей устойчивости к:
- Масла
- Химические вещества
- Углеводороды
- Растворители
Полиуретан очень прочен в расширенном или вспененном формате.Это делает его идеальным для использования на рынках мебели и автомобилей для использования в сиденьях и амортизаторах.
Свойства и применение неопрена
Полиуретановые материалы обладают хорошей устойчивостью к воздействию высоких или низких температур. В некоторых случаях они могут выдерживать диапазон температур от -45 ° C до 150 ° C, хотя в большинстве случаев рекомендуемым верхним пределом является температура 105 ° C.
Неопреновые пены производятся только в формате с закрытыми порами, чтобы обеспечить герметизирующие свойства там, где пенополиуретаны не могут обеспечить.
Производители неопрена
Итак, теперь вы знаете различия между ними! Если вам потребуется дополнительная информация при выборе между неопреном и полиуретаном, не стесняйтесь обращаться к нам по телефону +44 (0) 1922 723740. Мы будем рады помочь с вашими требованиями к полиуретановой пене с открытыми порами и с потребностями в губке из неопрена с закрытыми порами. .
Чтобы узнать больше о неопрене, нажмите здесь.Кроме того, неопрен можно смешивать с рядом материалов, включая популярный полимер EPDM.
Типичные свойства неопреновой губки с закрытыми ячейками SCE43NEO
Описание: Неопрен SCE43NEO с закрытыми ячейками может использоваться во многих внутренних и наружных прокладках, где требуется диапазон температур от -40 ° F до 150 ° F. Неопрен с закрытыми порами — это губка высокой плотности, которая обеспечивает стойкость к маслам и отличную стойкость к ультрафиолетовому излучению.SCE43NEO соответствует требованиям по воспламеняемости FMVSS-302 и UL 94HF-1 (не внесен в список UL). Неопрен SCE43NEO соответствует физическим требованиям ASTM D 1056-07 2C3.
Стиль SCE43NEO с закрытыми ячейками Неопрен — это материал высокой плотности, который также доступен с мягкой плотностью (SCE41NEO) и средней плотностью (SCE42NEO). SCE43NEO может поставляться в листах размером 36 x 64 дюйма и, в зависимости от количества, в рулонах шириной от 1/4 дюйма до 36 дюймов.Atlantic Gasket может поставлять SCE43NEO с клеем или без него. Модель SCE43NEO может быть вырезана методом высечки или гидроабразивной резки в соответствии с вашими требованиями.
Технические характеристики | |
---|---|
ASTM D 1056-07 | 2C3 |
ASTM D 1056 СУФФИКС | B2, F1, M |
ASTM D 6576-07 | ТИП II A, B, СРЕДНИЙ |
Физические свойства | Метод испытаний | Единица измерения | Результат |
---|---|---|---|
Прогиб при сжатии при 25% | ASTM D 1056 | фунтов на кв. Дюйм кПа | 11 +/- 2 75.8 +/- 13,8 |
ПЛОТНОСТЬ | ASTM D 3575 | pcf г / см 3 | 16 +/- 4 0,256 +/- 0,064 |
ПОГЛОЩЕНИЕ ВОДЫ (МАКС.) | ASTM D 1056 | % | 5 |
НИЗКАЯ ТЕМПЕРАТУРА | НЕТ | ˚F ˚C | -40 ˚F -40 ˚C |
ВЫСОКАЯ ТЕМПЕРАТУРА | НЕТ | ˚F ˚C | 150 ˚F 65 ˚C |
ВЫСОКАЯ ПРОМЕЖУТОЧНОСТЬ | НЕТ | ˚F ˚C | 200 ˚F 93 ˚C |
ПРОЧНОСТЬ НА РАЗРЫВ (СРЕДНЯЯ) | ASTM D 412 (DIE A) | фунтов на кв. Дюйм кПа | 150 1030 |
УДЛИНЕНИЕ (СРЕДНЕЕ) | ASTM D 412 (DIE A) | % | 100 |
ПРОЧНОСТЬ НА РАЗРЫВ | ASTM D 624 (DIE C) | фунт / дюйм кН / м | 20 3.5 |
КОМПРЕССИОННЫЙ НАБОР (МАКС.) | ASTM D 1056 | % | 25 |
ЗАМЕНА КОМПАКТНОГО ДИСКА ПОСЛЕ СТАРЕНИЯ | ASTM D 1056 | % | +/- 30 |
УСТОЙЧИВОСТЬ (СРЕДНЯЯ) | ASTM D 2632 | % | 10 |
ЦВЕТ | НЕТ | НЕТ | ЧЕРНЫЙ |
Уникальные особенности:
- Соответствует FMVSS-302
- Соответствует UL94 HF-1 (не указан)
- SAE J 18 APR2002 обозначение: 2A3 / 2C3
ЗАКРЫТЫЕ КЛЕТКИ НЕОПРЕНУСТОЙЧИВОСТЬ ДО | |
---|---|
КИСЛОТА | ХОРОШО |
ЩЕЛОЧНЫЙ | ХОРОШО |
БЕНЗИН И МАСЛО | ХОРОШО |
АРОМАТИЧЕСКИЕ УГЛЕВОДОРОДЫ | ЯРМАРКА |
ОЗОН | ЯРМАРКА |
КЕТОНЫ | ПЛОХО |
ХЛОРИРОВАННЫЕ РАСТВОРИТЕЛИ | ПЛОХО |
ОКИСЛЕНИЕ | ХОРОШО |
Эта информация предоставляется в качестве руководства по выбору материалов.Atlantic Gasket Corp. не несет ответственности за результаты или использование этой информации. Заказчик несет ответственность за получение и тестирование образцов при определении пригодности материала для конкретного применения.
Руководство по материалам неопреновой губки: свойства, типы и применение
Неопрен — популярный эластомер, который встречается практически во всех отраслях промышленности. Узнайте больше об услугах по высечке и изготовлению неопреновой губки Фрэнка Лоу на заказ.
— это каучук черного цвета , используемый в отраслях, где требуются умеренные уровни устойчивости к атмосферным воздействиям, нефти, озона и масел.В качестве синтетической альтернативы натуральному каучуку неопреновая губка доступна в следующих цветах:
- Твердый лист неопреновый поролон
- Неопрен с открытыми порами
- Неопрен с закрытыми порами
Сегодня неопреновая губка или неопреновый поролон составляют крупную промышленность — встреча потребности в несколько миллиардов фунтов каждый год.
Этот материал может похвастаться рядом замечательных качеств, но его способность сиять и работать в обширном списке коммерческих и промышленных применений делает его практически незаменимым.
Давайте подробнее рассмотрим неопреновый губчатый материал, способы его использования и многое другое.
Неопреновая губка Области применения и рынки
С тех пор, как в 1930 году была изобретена листовая неопреновая резина, этот универсальный материал использовался в различных отраслях промышленности и сферах применения, включая производство прокладок, водные изделия, электроизоляцию и многое другое.
Некоторые из типичных отраслей промышленности и областей применения, для которых мы предлагаем решения из неопреновой губки, включают:
- Строительная промышленность — Неопрен широко используется в этой отрасли благодаря своей высокой прочности на разрыв, отличной озоностойкости, отличным погодным условиям и погодным условиям. низкая степень сжатия.Обычно используется в лифтовых астрагалах; мостовые и автодорожные уплотнения; нестандартные уплотнители окон; оконные уплотнители из неопрена; и более.
- Fenestration Industry — Неопрен регулярно используется для дверей и чувствительных уплотнений, а также оконных уплотнений с запорной планкой.
- Массовый транспорт — неопреновая губка отвечает исключительно высоким требованиям по дымо-пламенной токсичности, предъявляемым к общественному транспорту.
- Автомобильная промышленность — Вы можете найти неопреновый губчатый материал по всему шасси и под капотом автомобилей в виброопорах, ботинках CVJ, уплотнениях амортизаторов, ремнях силовой передачи и т. Д.
- Производство кабелей и проводов — неопрен обеспечивает лучшую огнестойкость, химическую стойкость, тепло-, атмосферостойкость и озоностойкость, чем его аналог из натурального каучука. В результате компоненты из неопреновой резины широко используются для защитных покрытий для проводов и кабельных систем, таких как сверхпрочные оболочки кабелей и оболочки кабелей.
- HVAC Industry — неопрен предлагает более эффективный уплотнительный материал для защиты блоков HVAC от атмосферных воздействий и внешних загрязнений.
Основные характеристики неопреновой губки
Неопрен, изготовленный из синтетического каучука, очень прочный, гибкий, эластичный и исключительно устойчивый к воде, маслу и другим растворителям.Кроме того, неопреновая губка отличается исключительной устойчивостью к сжатию.
Прокладки из неопрена обычно производятся для герметизации. Вот некоторые из наиболее желательных атрибутов неопренового губчатого материала:
Неопрен может выдерживать повседневные химические вещества, что позволяет использовать его для обычных уплотняющих ролей, не опасаясь ухудшения качества продукта или выхода из строя. В отличие от других пенопластов, долговечность неопрена делает его отличным кандидатом для различных прокладок и уплотнений.
- Теплоизоляция Атрибут будет поддерживать высокие и низкие температуры, сохраняя при этом нежелательные тепловые условия. Неопрен отлично регулирует и поддерживает температуру окружающего воздуха. Проще говоря, губка из неопренового каучука не пропускает влагу или тепло, поэтому вы можете найти этот материал для холодильников, где герметичность имеет решающее значение.
- Неопрен гибкий и не деформируется, что означает, что он устойчив к сжатию и хорошо отскакивает.
- Благодаря прочности и гибкости неопрена они отлично подходят для использования в продуктах, требующих длительного жизненного цикла.
- Легкость неопрена позволяет ему существенно повысить ценность продуктов и приложений без дополнительного веса.
- Благодаря уникальной структуре резины с открытыми порами, неопрен может значительно снизить уровень шума.
- Неопрен обладает замечательной устойчивостью к озону и атмосферным воздействиям, включая устойчивость к влаге, дождю, снегу, УФ-лучам и воздуху.
Различные типы неопреновой губки
Компания Frank Lowe предлагает ряд различных типов неопреновой губки различной плотности и толщины, а также в рулонах или листах. Когда дело доходит до выбора лучшего типа неопрена, вы не одиноки.
Эксперты Frank Lowe обладают многолетним опытом, позволяя найти лучшее решение для уникальных потребностей наших клиентов. Мы выслушаем ваши потребности в применении и позаботимся о том, чтобы вы выбрали наиболее эффективный и действенный тип неопреновой губки.
Заказать Die Cut Neoprene Sponge
Ищете неопреновую губку определенной формы и толщины? Фрэнк Лоу может помочь! Мы используем современное оборудование и процессы, чтобы быстро доставить , быструю и точную губку для высечки в соответствии с техническими условиями применения.
Мы также предлагаем губку Kiss Cut , в которой материал полностью прорезан, а подложка остается нетронутой. Когда губка для поцелуев комбинируется с нашим самоклеящимся клеем, вы получаете легко наносимый, отшелушивающий и прилипающий компонент.
Свяжитесь с Фрэнком Лоу по поводу неопреновой губки
Независимо от марки, формы, плотности, цвета или толщины губки — Фрэнк Лоу может помочь.
Сотрудничая с нами, вы получите доступ к более чем 60-летнему опыту. Самое главное, что наши опытные инженеры по продукту будут работать над тем, чтобы понять ваш продукт и приложение на самом глубоком уровне. Это дает нам возможность помочь вам мыслить нестандартно и:
- Изучите различные толщины, формы и марки неопреновой губки, а также другие потенциальные материалы.
- Изучите каждый потенциальный вариант с анализом осуществимости, производительности и рентабельности.
- Создайте компонент или прокладку из неопреновой губки, которые не выходят за рамки вашего бюджета и обеспечивают наилучшие характеристики.
Готовы начать? Начните сегодня, связавшись с Фрэнком Лоу для беспроблемной консультации без каких-либо обязательств.
Точка плавления силиконового каучука
22 сентября 2015 г.
Это вопрос, который компании Silicone Engineering часто задают инженеры и дизайнеры, которые ищут точную температурную точку, при которой силиконовая резина начнет разлагаться при нанесении.
В большинстве случаев наши специалисты не могут дать однозначного ответа без дальнейшего обсуждения условий окружающей среды, в которой будет находиться силикон, и температуры, которой (-ам) будет подвергаться материал.
Силиконовый каучук, в отличие от большинства других каучуков, может выдерживать экстремальные температуры от 200 ° C до -60 ° C без деформации. Тем не менее, один аспект определяет, какие фактические температуры силикон действительно может выдерживать, и это ВРЕМЯ — Продолжительность времени, в течение которого силикон подвергается экстремальным температурам, определяет его срок службы и характеристики при применении, и это очень важный фактор при выборе резиновых материалов для приложений. .
Конечно, компания Silicone Engineering может говорить только о наших сортах силикона, но давайте приведем пример; Если силиконовая прокладка , изготовленная из нашего высокотемпературного сорта kSil ™ THT, подвергается воздействию температур до 300 ° C в течение периодических периодов, мы можем с уверенностью сказать, что наш силикон прошел испытания на выдерживание такой степени нагрева в течение коротких периодических периодов и будет поддерживать свои физические свойства. Однако, если бы инженер сообщил нам, что прокладка будет применяться в среде, где эта температура была постоянной 300 ° C, мы бы посоветовали, что силикон, скорее всего, разложится в течение более короткого срока службы, поэтому могут потребоваться другие варианты материалов. считается.
Тот же сценарий применим и к нашим маркам силикона общего назначения. Материал был протестирован на способность выдерживать постоянную температуру 230 ° C, что в большинстве случаев подходит для многих высокотемпературных применений. Однако мы также знаем, что этот сорт будет хорошо работать при более высоких температурах 250 ° C в течение снова прерывистых периодов , поэтому вопрос о «времени воздействия» этих температур необходимо оценить, прежде чем мы сможем посоветовать подходящий сорт силикона. использовать при высоких температурах.
Следовательно, при понимании силикона или любого другого эластомера, используемого в условиях высоких / низких температур, период воздействия, который резина будет испытывать при определенной температуре, является решающим фактором при попытке ответить на вопрос «Какие температуры может выдерживать силиконовая резина».
Что мы действительно знаем, так это то, что для любых приложений, подвергающихся постоянному воздействию температур выше 150 ° C, скорее всего, потребуется силиконовая резина, чтобы обеспечить эффективную работу и более длительный срок службы.Именно здесь компания Silicone Engineering может предоставить силиконовые решения для многих секторов промышленности и приложений.
Насколько сильно нагревается силикон, прежде чем он расплавится?
Первое, что вы заметите, это то, что силикон не плавится только от температуры!
Например, при нагревании до 150 ° C вы увидите очень мало изменений в силиконе, даже если выдерживать при этой температуре в течение очень долгого времени. При 200 ° C силикон со временем станет тверже и менее эластичным, и Если силикон нагреть до температуры выше 300 ° C, то из-за таких экстремальных температурных условий материал быстро станет тверже и менее эластичным, но при этом он не расплавится.
Температура плавления силиконовой резины
Доступны специальные марки для дальнейшего повышения уже естественно высокой термостойкости силиконов, например, наш силикон марки THT, который можно периодически использовать при температурах до 300 ° C.