Конструкции из фанеры
На сегодняшний день очень широко распространено направление экологически чистых продуктов. Курс на экологические продукты, в том числе на упаковку и стойки, торговую мебель, торговые стеллажи, промостойки, торговые дисплеи на которых они представлены. Как правило, распространен сотовый картон, так называемый реборд. Он хорош тем, что он легкий. В логистике его плюс тем, что он недорогой, а также он быстрый в сборке. Бывает многокомпонентный сотовый картон с участием металла, пластиков и так далее. Но у картона есть также свои минусы, он боится влаги. Как бы он не был защищен разными пластиковыми поддонами, но основная часть нагрузки влаги и персонала, участвует в судьбе картонных стоек. И с каждым днем все больше картонных стоек приходит в негодность. Мы разработали стойки из фанеры, из мебельного щита, стойки которые собирается без единого гвоздя, самореза, или системы крепления. Стеллажи из фанеры вырезаются лазером или на станках ЧПУ. Обрабатываются необходимым колером по цвету, собираются резными замками.
Какие вопросы задают заказчики по производству фанерных дисплеев торговых стеллажей или стеллажей из фанерного щита. Какую нагрузку выдерживают полки под их размеры продуктов, максимальная нагрузка. Какой вес стойки, сможет ли собрать ее промоутер. Отвечаем, да. Они легко собираются, вес выдерживают любой, хоть 50 кг на каждую полку. Стеллаж весит 2-3 кг, если с максимальной нагрузкой на полку, то порядка 6-8 кг. Это хороший вес для такого вида оборудования. Также мы снабжаем их полкодержателями, ценникодержателями и шелфбанерами, шелфтокерами. Это уже отдельный продукт.
Клееные фанерные конструкции — Производство конструкций из дерева
Клееные фанерные конструкции
Категория:
Производство конструкций из дерева
Клееные фанерные конструкции
Наиболее распространены клееные фанерные балки двутаврового и коробчатого сечения с параллельными поясами. Реже изготовляют односкатные балки и двускатные. Пролет балок 9… 18 м. Для стенок применяют водостойкую фанеру толщиной 6…12 мм, а для поясов — пиломатериалы первого и второго сортов толщиной не более 5 см. Сплошная фанерная стенка обеспечивает жесткую связь между поясами и воспринимает сдвигающие усилия. Волокна рубашек фанеры направляют вдоль поясов, что увеличивает несущую способность балок и позволяет применять фанерные элементы, стыкованные «на ус». Балки коробчатого сечения используют для покрытия выставочных помещений, павильонов, кафе, а также для устройства легких мостов.
В балках двутаврового и коробчатого сечения необходимо обеспечивать устойчивость стенки постановкой ребер жесткости и предусматривать меры против скручивания. Во избежание отрыва поясов от стенки вследствие влажностных деформаций в досках поясов делают продольные неглубокие прорези.
Рис. 1. Схемы металлодеревянных ферм с верхними поясами из клееных блоков: а — треугольной; б — с параллельными поясами; в—пятиугольной двускатной; г — сегментной; д — многоугольной
Рис. 2. Схемы фанерных балок
Рис. 3. Балки с волнистой фанерной стенкой (а) и собранная из них треугольная арка с затяжкой (б)
Рис. 4. Схема клееных фанерных рам: а — двутаврового сечения с монолитным карнизным узлом; б — коробчатого сечения со сборным узлом
Фанерные балки коробчатого сечения применяют для перекрытия пролетов до 18 м. Каркас большепролетных балок выполняют в виде решетчатой фермы, обклеиваемой с обеих сторон фанерой.
Устойчивость фанерных балок значительно повышается, если стенка имеет волнистую форму. К достоинствам таких балок относятся малая масса при значительной несущей способности, минимальный расход материалов, возможность поточного изготовления, легкость транспортирования и монтажа. В балках с волнистой сгенкой не используют металлические крепежные детали, поэтому их можно обрабатывать антисептиками и антипиренами, не опасаясь коррозии. Пояса балок соединяют с волнистой стенкой путем ее заклинивания в волнообразно выбранных пазах, смазанных клеем. Балки с фанерной стенкой изготовляют пролетом 6…9 м.
Рис. 4. Трехшарнирные фанерные рамы коробчатого сечения
Для перекрытия пролетов 12… 18 м применяют фанерные рамы двутаврового или коробчатого сечения. Рамы собирают по трехшарнирной схеме, причем конструкция карнизного узла может быть сборной или монолитной. При сборном решении в поясах рам двутаврового сечения закрепляют стальную арматуру (стержни, полосы, профили) с выпусками, которые соединяются механическими средствами. При монолитном решении пояса изгибают или соединяют на клею при помощи гнутых вставок из шпона или тонких досок. Концы вставок соединяют с поясами зубчатым шипом.
В рамах коробчатого сечения карнизный узел делают, как правило, жестким. При наклейке фанеры на каркас в зоне карнизного угла стыки листа располагают возможно дальше от его середины, а волокна рубашек направляют вдоль ригеля для лучшего восприятия изгибающих усилий. Фанеру применяют водостойкую, толщиной 8…12 мм.
Из клееных фанерных элементов двутаврового сечения собирают, кроме тогд, трехшарнирные арки треугольного или кругового (из сегментов) очертания пролетом 15…30 м.
Рис. 6. Пространственные конструкции из фанеры
Эффективными фанерными конструкциями являются пространственные оболочки. Обладая весьма малой массой, они в то же время очень устойчивы. Из всех форм оболочек наиболее распространенными являются гиперболические оболочки (прямолинейная образующая, простой отвод воды, малая деформируемость). Гиперболические клееные фанерные оболочки конструируются из скрученных фанерных элементов одного типоразмера длиной, равной пролету оболочки. Фанерный элемент представляет собой деревянный каркас, обклеенный с одной стороны водостойкой фанерой.
Из клееных фанерных элементов кругового очертания собирают цилиндрические и стрельчатые своды коробчатого сечения. Элемент свода представляет собой панель с криволинейными клееными продольными ребрами высотой до 100 мм, к которым с обеих сторон приклеивают водостойкую фанеру толщиной 6…8 мм. Для обеспечения устойчивости сжатых верхних листов фанеры между продольными ребрами ставят фанерные диафрагмы. В ячейки между ребрами и диафрагмами укладывают блоки пенопласта. Ниж-ные торцы панелей опираются на фундамент, верхние соединяются в коньке встык с помощью накладок. Чередуя панели разного радиуса кривизны, можно получить серповидные вертикальные проемы, остекление которых образует световые фонари.
К пространственным фанерным конструкциям относятся также элементы сборных зернохранилищ и силосов для минеральных удобрений. Это кольца диаметром 3…4 м или квадратные призмы со стороной 3…4 м с манжетами для болтовых соединений. Кольца собирают в цилиндрическую или коробчатую башню высотой до 4…5 м. Стенки квадратных элементов представляют собой ребристые панели с обшивками из водостойкой фанеры толщиной 10 мм, приклеенной к продольным ребрам. Для образования пространственной конструкции панели соединяют в узлах стальными штырями, вклеенными в отверстия в ребрах под углом 45° эпоксидно-цементным клеем.
Пространственные конструкции (своды) могут быть образованы кленными фанерными косяками. Это плоские элементы коробчатого сечения с криволинейным верхним поясом, собираемые на болтах в решетчатый свод. Фанеру толщиной 10 мм приклеивают к деревянным брускам, расставленным с учетом размеров листа фанеры так, чтобы стыки попадали на кромку бруска.
Реклама:
Читать далее:
Конструкции из древесных плит
Статьи по теме:
КЛЕЕФАНЕРНАЯ БАЛОЧНАЯ КОНСТРУКЦИИ С Х-ОБРАЗНОЙ ФАНЕРНОЙ СТЕНКОЙ И ПАЗЛОВЫМИ СОЕДИНЕНИЯМИ ФАНЕРЫ Д-р техн. наук В.В. Фурсов, инж. А.Н. Бидаков
Буді вельні м атеріали , констр укці ї і спор уди
Збірник наукових праць УкрДАЗТ, 2014, вип. 148, ч. 2
131
working hours during production. Cross ribs absence or at least significant reduction of ribs quantity
substantially induce manufacturability growth of production of glued thin-webbed beams.
The primary test was carried out for the new type of plywood connections with different geometry
configurations of elements of the jointed parts and called “puzzle joints”.
Key words: thin-webbed beam, plywood web, effective decisions, puzzle joints of plywood.
Вступление. Создание новых
эффективных форм строительных конструкций
становится приоритетным направлением для
решения многих задач и проблем в
существующих конструктивных решениях
несущих элементов зданий и сооружений.
Клеефанерная Х-образная балка является
первым результатом на пути создания
безреберных конструкций за счет кривизны
фанерных элементов балочной конструкции.
Постановка проблемы. Среди
множества типов существующих балок из
древесины и древесных материалов, наиболее
экономичными по расходу материала являются
балочные клеефанерные конструкции с
плоскими стенками. Недостаток таких балок
заключается в необходимости обеспечения
устойчивости стенок, что требует постановки
дополнительных поперечных ребер, плотно
приторцованных к поясам. Этот процесс
составляет около 50% от всего объема
трудозатрат по их изготовлению. Отсутствие
поперечных ребер, или уменьшение их
количества, может резко повысить
технологичность изготовления клеефанерных
балок. Разработанная на кафедре МДК ХНУСА
и защищенная патентом балка с Х-образной
фанерной стенкой существенно снижает
недостатки клеефанерных балок, что было
подтверждено их испытаниями.
Анализ последних исследований и
публикаций. Известно несколько
конструктивных решений, в которых фанера
используется в качестве стенки: в
клеефанерных балках, рамах и арках. В них
применяют двутавровые поперечные сечения с
одной плоской или волнистой фанерными
стенками, а также в виде коробки с двумя
стенками.
Среди отечественных специалистов,
значительные экспериментальные и
аналитические исследования клеефанерных
балок принадлежат таким исследователям как:
Дмитриев П. А., Лобанов Ю.А., Осипов Ю.К.,
Большаков В.В., Макаров Г.П., Кириленко В. Ф.
[2-4] и др. В настоящее время большое
внимание к фанерным конструкциям уделяется
в работах немецких ученых, в особенности
школы профессора Blaß, H. J., таких как Frese,
M., Glos [6-7], Flaig M. [8], и др. Группой
Японских ученых под руководством Hiroshi
Yoshihara [9-12] проведены испытания, в
которых исследованы упругие характеристики
фанеры, а также предложены новые более
точные методы их определения. Например,
разработаны технические рекомендации для
определения свойств фанеры при сжатии
образцов, так называемым методом IITRI
(Illinois Institute of Technology Research Institute,
USA), несмотря на уже существующие
американские рекомендации по подобным
испытания по ASTM D 3501-94 (ASTM 1994).
Разработка и конструирование Х-
образной балки проходила с учетом данных
авиастроителей первой половины ХХ века. К
примеру, штурмовик Ил-2 представлял собой
моноплан с нижним расположением крыла у
которого обшивка хвостовой части фезюляжа и
крыльев выполнялись из фанеры. Силовой
каркас крыла (рис. 1), состоящий из
лонжеронов, стрингеров и нервюр выполнялся
из фанеры и дерева, или из дюралюминия.
Так как форма обшивки крыльев имеет
изогнутую форму, то конструирование таких
балок основывалось на данных исследователей
ЦАГИ им. Жуковского, а именно:
В.М. Стригунов, А.Ю. Ромашевский,
Г.А. Олейников, Г.Г. Ростовцев, М.Л. Лурье и
др. сделали весомый вклад в теоретические и
экспериментальные исследования различных
тонкостенных балок с параллельными поясами,
а также подкрепленных и неподкрепленных
обшивок работающих на сжатие. Такие
наработки способствовали критической оценки
и анализу проведенных исследований Х-
образной клеефанерной балки.
Методика проведения экспериментов.
В лаборатории строительных конструкций
(ХНУСА) проводились испытания нового типа
клеефанерных балок с изогнутыми фанерными
стенками и дощатыми клееными поясами.
Соединение фанерных стенок с поясами балок
Каркас дивана. Диваны из ДСП. Диваны из фанеры. Диван на металлокаркасе.
Мягкая мебель должна быть не только красивой, но также иметь крепкий и надежный каркас. Каркас является основным элементом конструкции дивана, базой для крепления других частей. Многочисленные раскладывания дивана или активные детские игры — ничто не должно мешать дивану служить долго!
Каркас может быть изготовлен из металла, натурального дерева, фанеры, оргалита, древесностружечной плиты (ДСП) или ламинированной ДСП. Не зависимо от материала — диванный каркас должен быть качественным. Если это деревянный каркас, то древесина должна быть без сучков и хорошо просушена. Детали металлического каркаса должны иметь антикоррозийное покрытие. Каркас из ДСП должен быть покрыт специальной краской, препятствующей выделению вредных веществ (формальдегидных смол).
Диваны с каркасами из ЛДСП
Пример неламинированной ДСП
Пример подлокотников из ЛДСП
Диваны с каркасом из ЛДСП — самые дешевые и менее надежные, чем с металлическими или деревянными. Однако, ЛДСП имеет эстетичный внешний вид и легко подвергается влажной уборке. Каркас дивана из ДСП тяжелее деревянного, обычно имеет толщину 16 мм. При производстве диванов ЛДСП часто комбинируют с деревом.
Диваны с каркасом из фанеры
Пример листовой фанеры
Пример каркаса из фанеры
Фанерные каркасы диванов обладают прочностью и легкостью, толщина каркаса обычно 12-25 мм. Диваны с каркасом из фанеры стоят дороже моделей из ДСП и натурального дерева.
Элементы конструкции каркаса из фанеры соединяются между собой мебельными скобами, которые изготавливаются из стальной проволоки в виде буквы П и дополнительно проклеиваются специальным мебельным клеем, что обеспечивает высокую прочность и долговечность соединений каркаса.
Диваны из массива
Каркас из натуральной древесины (ель, сосна, дуб, орех, ясень) обычно используется в качестве направляющих для уменьшения износа, а также для придания прочности в ответственных местах конструкций.
Однако, как правило диваны с каркасом из массива стоят намного дороже, крайне непрактичны в применении, и не подходят для ежедневного использования. Данные модели мягкой мебели редко имеют механизм трансформации их использование в качестве кровати практически не возможно. Однако, если Вы предпочитаете классический стиль мебели, то вм стоит остановится именно накаркасе дивана из массива.
Диваны с металлическим каркасом
Существуют конструкции диваны, основания которых состоят из рамы и деревянных ортопедических лат (или изогнутых перекладин), обеспечивающих «подпружинивающий» эффект.
Латы крепятся к раме с помощью латодержателей. Каучуковые латодержатели — наиболее прочные, так как они имеют амортизатор, дающий гибкой планке свободу движений, что, в свою очередь, помогает основанию выдерживать большой вес. Кроме того, наличие таких латодержателей гарантирует отсутствие скрипа, что также немаловажно.
Здесь можно посмотреть все диваны на металлокаркасе с ортопедическим основанием….
Разновидности металлокаркаса:
1. Собственно металлокаркас — диваны с механизмом клик-кляк, где весь диван состоит из металла.
2. Комбинированный металлокаркас — диваны с механизмом пантограф или тик-так — это модели, где только раскладываемая часть состоит из металла, а остальное – из дерева, фанеры и ЛДСП
Данный механизм — это разновидность еврокнижки, который можно разложить так легко, что это смоет сделать даже ребенок. Суть металлокаркаса в том, что он как раз и помогает раскладыванию.
Трансформация осуществляется путем «шагания» дивана вперед. При этом вы не повредите напольное покрытие.
Также существует металлоокаркас в выкатных диванах на роликах: где он крепится к каркасу дивана и упрощает раскладывание.
Пример дивана Наташа 190 см…
Почти всегда подъемный механизм диваных ящиков состоит из металла. На примере дивана Наташа 150 см.
Что можно сделать из фанеры. 24 Мастер-класса
от Aleksey | Поделки Декор Мастерская Мебель Дешево Аксессуары | Понедельник, 02 июля 2018
Подпишитесь на Make-Self.net в Facebook и читайте наши статьи первыми. |
Мода на экологически чистые материалы плавно перетекла из 2015 года в 2016-й. Однако в рейтинге востребованности самих материалов произошли некоторые изменения. Так, например, вместо натурального дерева дизайнеры всё чаще стали использовать обычную фанеру. Сегодня из фанеры создают мебель, отделку, сантехнику и даже фасады зданий. Обычный доступный материал, к которому раньше относились снисходительно, неожиданно оказался на пике популярности.
В эпоху минимализма, природных мотивов и естественности фанера как нельзя лучше «пришлась ко двору». Ещё совсем недавно этот материал считался безликим, неприглядным и слишком дешёвым на вид. При изготовлении мебели фанеру зачастую маскировали деревянным шпоном. Только в последнее время дизайнеры наконец-то обратили внимание на изящный ненавязчивый рисунок, свойственный её поверхности. И сегодня, наряду с оголёнными кирпичными стенами и ничем не покрытыми бетонными полами, в моде — отделка и мебель из натуральной фанеры, без отделки и прикрас.
Фанера — идеальный вариант для изготовления мебели. Помимо прочности и экологичности, она обладает таким немаловажным качеством, как простота резки и конструирования. В отличие от деревянных досок фанерным плитам можно придать любую форму: ломаную, закруглённую. Этот материал не ограничивает фантазию дизайнера, а наоборот, стимулирует его к смелым творческим экспериментам.
1. Подставка для корреспонденции.
Подробное описание тут.
2. Оригинальный стол из фанеры.
Подробное описание тут. Вам также может быть интересно — 25 Примеров как самостоятельно сделать журнальный стол.
3. Настольный органайзер.
Подробное описание тут.
4. Простой диванчик из фанеры.
Подробное описание тут. Вам также может быть интересно — 36 Примеров как самостоятельно сделать диван.
5. Современное зеркало на фанерной основе.
Подробное описание тут. Вам также может быть интересно — 11 Способов сделать самостоятельно уникальное зеркало.
6. Удивительные полочки.
Подробное описание тут.
7. Подставка для аксессуаров.
Подробное описание тут.
8. Простые стеллажи из фанеры.
Вам также может быть интересно — Книжный стеллаж из деревянного бруса.
9. Основа для галереи.
Подробное описание тут. Вам также может быть интересно — 25 Уникальных идей настенной галереи.
10. Компактный органайзер.
Подробное описание тут.
11. Табурет из фанеры.
Подробное описание тут.
12. Подставка для украшений.
Подробное описание тут.
13. «Мини-коттедж» для ребенка.
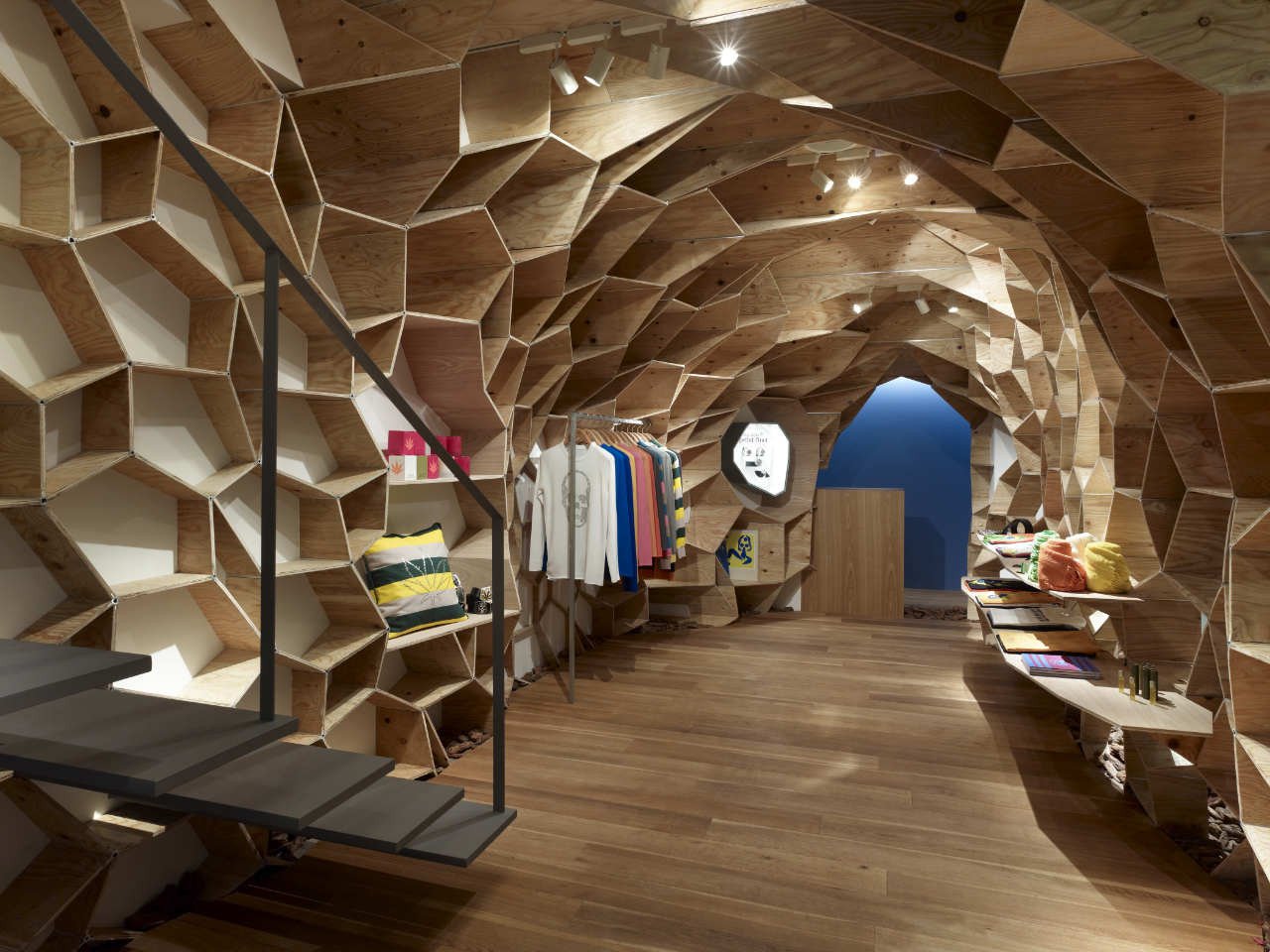
Подробное описание тут.
14. Геометрический домик для собаки.
Подробное описание тут. Вам также может быть интересно — 25 Потрясающих домиков для собаки или 30 Домиков для кошек.
15. Элемент декора из фанеры.
Подробное описание тут.
16. Оригинальная картина.
Подробное описание тут.
17. Скамейка в прихожую из фанеры.
Подробное описание тут. Вам также может быть интересно — 30 Примеров как обустроить маленькую прихожую.
18. Тумба под телевизор.
Подробное описание тут.
19. Фартук из фанеры.
Подробное описание тут. Вам также может быть интересно — 80 Фантастических примеров кухонного фартука.
20. Необычная тумба из фанеры.
Подробное описание тут. Вам также может быть интересно — как самостоятельно сделать прикроватную тумбу.
21. Портативный настенный органайзер.
Подробное описание тут.
22. Модульные полки из фанеры.
Подробное описание тут.
23. Светящееся картина.
24. Компактный столик.
Подробное описание тут. Вам также может быть интересно — 25 Примеров как самостоятельно сделать журнальный стол.
Бонус. 25 Примеров мебели из фанеры
Полезные короткие видео от Make-Self.net
Подписывайтесь на наш уютный Telegram канал
СВЕЖИЕ СТАТЬИ
ПОПУЛЯРНЫЕ СТАТЬИ
Изготовление конструкций из досок, фанеры и древесных плит
Категория: Деревянные конструкции
Изготовление конструкций из досок, фанеры и древесных плит
Клееные дощатые конструкции изготовляют в специально оборудованных цехах, состоящих из нескольких отделений или участков. Сначала высушенные пиломатериалы поступают на участок торцовки, где из досок вырезают дефектные места и недопустимые пороки древесины. Торцовку выполняют на станках поперечной распиловки ЦПА-40; Ц-6-2 и др. Затем проводят продольную распиловку, после которой пласти досок фрезеруют для дополнительного выявления пороков древесины.
Следующая операция — фрезерование шипов, выполняемая на шипорезных или фрезерных станках, работающих самостоятельно или входящих в поточные линии. Рабочим органом станков являются специально изготовленные фрезы. Группировка фрез на шпинделе зависит от направления зубчатых шипов относительно пласти заготовок. Шипы можно нарезать параллельно пласти или поперек пласти. В последнем случае прочность зубчатого стыка увеличивается.
Для вырезки зубчатых шипов рекомендуются многошпиндельные станки Ш015Г-5 и Ш010-4 (рамные односторонние), ШД-10-3 (рамный двусторонний), ШПА-40 (шипорезный для прямого шипа).
После нарезки зубчатых шипов заготовки стыкуют для получения длинных досок (лент), которые затем разрезают на заготовки необходимой длины при помощи торцовочного станка и собирают в пакет. Доски, образующие ленту, стыкуют в торцевом прессе при давлении 1,5—10 МПа, зависящем от формы и размеров шипового соединения. На период отверждения клея ленты должны находиться в неподвижном состоянии несколько часов. Однако в некоторых случаях благодаря самозаклиниванию зубчатых соединений достаточно приложить кратковременное (2—3 с) давление и затем фрезеровать ленты. Если заготовки стыкуют при нагревании, время выдержки стыка под давлением составляет 1—2 мин.
Рис. 1. Планировка цеха клееных дощатых конструкций мощностью 3 тыс.м1 конструкций в год 1 — тележка для пиломатериалов; 2,6,14,17,19 — торцовочные станки; 3 — круглопильный станок; 4,8,16 — рейсмусовые станки; 5, 12 — шипорезные станки; 7 — рольганг; 9 — камера ускоренного отверждения кля; 10 — установка продольного стыкования досок; 11 — клеевые вальцы; 13 — гидравлический пресс; 15 — площадка выдержки запрессованных пакетов; 18 — станок для продольной распиловки клееных блоков; 20 — испытательный стенд
Рис. 2. Фреза для нарезки зубчатых шипов (а) и схемы нарезки торцов досок зубчатым шипом параллельно пласти (б) и поперек пласти (в)
Кроме устройств, соединяющих доски на зубчатый шип в неподвижном положении, применяют установки непрерывного действия, в которых склеивание происходит в движении. В них давление, необходимое для запрессовки соединений, создается усилием подачи на входе и сопротивлением трения на выходе. Производительность таких установок 4—6 соединений в минуту.
После необходимой для отверждения клея выдержки стыкованные доски подают на обработку к рейсмусовому станку. Фрезерование проводится с двух сторон. Точность обработки должна обеспечивать шероховатость поверхности в пределах 1—2 класса (максимальная высота неровностей 100—300 мкм). Доски обрабатывают в порядке, обратном укладке слоев в пакет, чтобы удобнее было наносить клей и быстрее загружать , пресс.
Клей на поверхность досок наносят механизированными клеевыми вальцами с одной или двух сторон ровным слоем с расходом 0,2—0,6 кг/м2 (в зависимости от вязкости клея и пористости древесины). Толщину клеевого шва и, соответственно, расход клея следует ограничивать нормами, установленными опытным путем. Неконтролируемое увеличение толщины клеевого шва вызывает внутренние напряжения, снижающие прочность соединений.
Практически толщина клеевого шва колеблется от 0,1 до 0,8 мм, в то время как максимальная прочность обеспечивается при толщине клеевой прослойки 0,1—0,2 мм. Чем толще слой клея, тем большее усилие запрессовки требуется для равномерного распределения клея в шве. Запрессовку проводят возможно быстрее, так как жизнеспособность клеев ограничена. Поэтому лучше загружать в пресс сразу целый пакет.
Винтовой способ запрессовки в горизонтальных и вертикальных ваймовых прессах применяют при склеивании прямолинейных и криволинейных (гнутых) блоков и элементов прямоугольного сечения. В горизонтальных ваймовых прессах доски с нанесенным на них клеем укладывают ребром на выверенные по горизонтали брусья и затем весь пакет прижимают винтовыми стяжками к укрепленным в полу стойкам, расставленным по прямой линии или по кривой заданного очертания. Кривизна задается с поправкой на последующее распрямление клеевых блоков, освобожденных от стяжек. Наименьший радиус зависит от толщины досок и обычно не превышает 10 м. Запрессовку начинают от середины пакета; для ее ускорения используют электрические гайковерты, оттарированные на заданный крутящий момент. Скорость гнутья 4—6°/мин. Удельное давление запрессовки 0,5—0,6 МПа.
После запрессовки удельное давление перераспределяется (снижается) вследствие пластических деформаций древесины, выдавливания или впитывания клея в доски; поэтому винты периодически подтягивают. Время выдержки пакета в прессе в зависимости от температуры воздуха в цехе составляет 6—24 ч. При склеивании с нагреванием время выдержки сокращается до 3—4,5 ч. Чтобы повысить производительность установок, в одном горизонтальном ваймовом прессе можно запрессовывать несколько пакетов, расположенных один над другим и разделенных прокладками.
В вертикальных ваймовых прессах доски укладывают плашмя на прямолинейные или криволинейные цулаги и стягивают пакет винтами. Для увеличения производительности вертикальные ваймовые прессы делают двухсекционными, запрессовывая одновременно два рядом расположенных пакета. В подвижном ваймовом вертикальном прессе (пресс-вагонетке) запрессовывают несколько прямолинейных пакетов и затем подают в камеру, где пакеты нагреваются для ускорения склеивания. Температура нагревания 50—90 °С. При нагревании до 80—90 °С влажность воздуха должна быть 74—78%, что обеспечивает влажность древесины 10%.
Запрессованные в вертикальных гидравлических прессах пакеты выдерживают до полного отверждения клея либо пакет, зафиксированный в зажимах под заданным давлением, извлекают из пресса и ставят на площадку для выдержки и отверждения клея при температуре цеха или при конвективном нагревании.
В последнем случае производительность гидравлического пресса значительно больше.
После выдержки в прессе клееные элементы поступают на обработку, которая заключается в отторцовке изделий по шаблону, фрезеровании боковых поверхностей, фрезеровании выемок, сверлении отверстий, а также в защите от увлажнения, загнивания и возгорания. Перед обработкой элементы выдерживают в цехе 1—2 сут для достижения достаточной прочности клеевого шва. Перемещать изделия по цеху или в другой цех можно также при условии достаточного отверждения клея. Для перемещения используют тельферы или тележки. Клееные изделия обрабатывают на столах длиной 10—15 м или на специальных стапелях. При обработке следует обращать внимание на монтажные гвозди в изделиях, чтобы не повредить рабочие части инструментов. Затвердевшие потеки клея, попадая на режущие части, быстро затупляют их, поэтому рекомендуется применять ножи из высокопрочной стали.
При сверлении отверстий пользуются шаблоном с отверстиями, расположенными соответственно разметке металлических накладок, шайб и т.п. Шаблон представляет собой деревянную или фанерную плиту, в отверстия которой вставлены металлические втулки с пружинными бойками. Ударяя по шляпке бойка молотком, размечают центры отверстий в клееном изделии. Опиливая стороны длинных изделий, особенно при косых резах, циркульную пилу перемещают по специальному рельсу. Криволинейные пропилы делают ленточными пилами.
Перед отправкой потребителю клееные изделия защищают от увлажнения и механических повреждений, возможных при перевозке и монтаже. Для защиты используют олифу, масляные и синтетические краски с различными наполнителями. Если необходимо сохранить натуральный цвет и текстуру древесины, клееные блоки покрывают прозрачными лаками — полиуретано-вым, полиэфирным. Торцы конструкций обмазывают водостойкими пастами на основе жидкого тиокола, каучуковых латексов или кремнийорганических эластомеров. При перевозке такие конструкции обертывают в прочную бумагу или полиэтиленовую пленку.
Клееные фанерные конструкции изготовляют в специализированных цехах и построечных мастерских, имеющих необходимое деревообрабатывающее оборудование. Доски каркаса или поясов балок строгают с припуском на дальнейшую обработку, вырезают дефектные участки на торцовочных станках, соединяют зубчатым шипом торцы, раскраивают ленты на отрезки заданной длины и строгают их в размер. Листы фанеры отбирают по сортам, намечая лучшие в более напряженные зоны конструкции. Затем листы размечают по шаблону и вырезают из них элементы заданной формы. При необходимости большей длины элементов, чтобы не производить стыковку в самой конструкции, края листов фанеры сращивают на ус в специальных усовочных станках.
При изготовлении балок или рам двутаврового сечения элементы поясов раскладывают на рабочей площадке в соответствии с проектной схемой или по шаблону и временно закрепляют. Доски поясов, непосредственно примыкающие к фанере, укладывают двойным рядом, с небольшим зазором между продольными кромками для снижения влияния влажностных деформаций на клеевой шов. Число слоев досок, образующих пояс, должно быть не более трех. При таком составном поясе сначала подшивают фанеру гвоздями к двойному ряду на клею, затем наслаивают остальные доски пояса. Клей на доски поясов наносят ручными клеевыми вальцами.
Подшивку фанеры к поясам, наслаивание досок поясов, прикрепление ребер жесткости и общую запрессовку всех элементов в единую конструкцию выполняют монтажными гвоздями. Размеры и расстановка этих гвоздей зависят от толщины фанеры, числа слоев досок в поясах, степени покороб-ленности досок поясов, качества обработки пиломатериалов и фанеры. Для подшивки фанеры к первому слою досок пояса применяют гвозди диаметром 2,3 мм, длиной 50 мм при расстоянии между ними 140—180 мм. Общую запрессовку поясов и ребер жесткости в единую конструкцию выполняют гвоздями диаметром 3,5—4 мм длиной 90—110 мм при расстоянии между ними 280—360 мм. Для изготовления клееных фанерных балок двутаврового сечения с дощатыми поясами применяют рамные винтовые прессы, работающие по принципу вертикального вай-мового пресса.
Изготовление балок с волнистой фанерной стенкой осуществляется непрерывным способом в специализированных цехах (рис. 8.3). Доски поясов, стыкованные зубчатым шипом, в виде двух лент, поставленных на ребро, проходят через фрезерный станок, в котором шпиндели совершают боковые движения, благодаря чему в лентах вырезаются волнообразные пазы конического профиля. В эти пазы вдавливается непрерывная фанерная лента; она изгибается волнообразно роликами и защемляется в пазах путем сближения поясов протягивающим устройством. Предварительно кромки фанерной ленты покрывают клеем. Для ускорения склеивания швы прогревают инфракрасными излучателями или токами высокой частоты. Усилия, возникающие при изгибе фанеры в пазах, создают давление, необходимое для склеивания фанеры со стенками паза. Получаемый непрерывно профильный элемент с волнообразной стенкой разрезается на балки длиной 6—9 м.
Рис. 3. Планировка цеха клееных фанерных балок с волнистой фанерной стенкой 1 — готовая продукция; 2 — склад фанеры; 3 — фанерные заготовки; 4 — круглопильный станок для фанеры; 5 — усовочный станок; 6 — агрегат для склеивания фанерных заготовок в ленту с электрическим обогревом; 7 — фанерные ленты; 8 — установка для подачи фанерной ленты; 9 — фреза для обработки кромок фанерной ленты; 10 — установка для нанесения клея и придания волнообразной формы ленте; 11 — дощатые пояса балок; 12 — линия склеивания поясов по длине; 13 — шипорезный станок; 14 — агрегат для запрессовки фанерной ленты в дощатые пояса; 15 — пиломатериалы; 16 — сушильная камера
Щитовые фанерные конструкции изготовляют с гвоздевой запрессовкой либо в одноэтажных гидравлических или пневматических прессах горячего или холодного склеивания. Гвоздевая запрессовка более целесообразна при изготовлении крупноразмерных щитов. Гвозди применяют диаметром 2— 2,5 мм длиной 40—50 мм с установкой их через 150—200 мм. Расход гвоздей снижается, если фанеру прижимать к каркасу при помощи деревянных брусков на более мощных гвоздях.
После отверждения клея эти бруски вместе с гвоздями отрывают. Для конструкций, где непроклеи в углах недопустимы, шаг расстановки гвоздей уменьшают вдвое и также применяют прижимные шаблоны.
При обшивке каркаса фанеру направляют волокнами вдоль большей стороны щита. В этом случае расстояние между элементами каркаса, направленными поперек волокон рубашек фанеры, должно быть не более 50 толщин листа. Клей на поверхность ребер наносят валиками, кистями или распылителями. Во избежание втягивания листов фанеры в ячейки каркаса рекомендуется использовать клеи, не содержащие воды, например клей ВИАМ-Б-3. При склеивании холодным способом в прессах можно укладывать сразу по нескольку щитов с общей высотой пакета до 1 м. Удельное давление запрессовки такого пакета должно быть не менее 1,4—1,5МПа в расчете на площадь ребер каркаса.
Изготовление конструкций из цементно-стружеч-ных плит — это изготовление панелей наружных стен и перегородок на деревянном каркасе, плит перекрытий, деталей сборных полов, санитарно-технических кабин, вентиляционных коробов и др. На технологию изготовления конструкций из плит влияют такие показатели как твердость (не менее 45 МПа), сопротивление выдергиванию шурупов (60 Н/мм), изменение линейных размеров в плоскости листа при увлажнении (0,3%). Отдельные размеры листов цементно-стружечных плит (длина 3200 мм, ширина 1250 мм) расходятся с принятым в строительстве модулем 300. Требуется дополнительная разрезка таких листов.
При изготовлении панельных перекрытий плиты прибивают или приклеивают к деревянному каркасу с заполнением пространства между минераловатным или пенопластовым утеплителем. Панели перекрытий могут выполняться также на стальном каркасе (элементы профилированного настила) с заполнением гофров и промежутков заливочным пенопластом. Для уплотнения стыков предусматривается крепление упругих прокладок, вставка шпонок в пазы крайних ребер, наклейка на место стыка герметизирующих лент и тканей.
Панели перегородок также изготовляют на деревянном каркасе, к которому плиты крепятся шурупами. Крайние ребра имеют выступ за габариты листа, а на противоположной кромке — впадину для сборки перегородок по схеме «шпунт — гребень».
Кромки панелей примыкают к несущим стенам. Их оборудуют скобами для крепления или в них делают паз, который при монтаже входит в вертикально прибитую к стене рейку.
Цементно-стружечные плиты раскраивают на заготовки на форматно-обрезном станке ЦТЗФ-2 или на станке с программным управлением ЦТМФ. Используют пилы дисковые с твердосплавными пластинами при скорости резания 25-35 м/с и подаче 0,09—0,12 мм на зуб пилы, плоские ножи и сборные фрезы — для фрезерования, цепочки фрезерные для выборки гнезд и пазов на цепнодолбежных станках. По длине плиты соединяют зубчатым шипом или с помощью односторонних накладок. Отверстия для гвоздей и шурупов сверлят зенкерами или твердосплавными спиральными сверлами. Гвозди вдавливают гидравлическими устройствами, шурупы ввертывают электроинструментом. Для склеивания цементно-стружечных плит с деревянным каркасом рекомендуется клей ФРФ-50М. Сборку панелей при склеивании ведут на сборочных конвейерах, производящих фиксацию, переворачивание и перемещение пакета. Склеивание происходит под давлением 0,2—0,3 МПа при равномерном контакте плит пресса и поверхности панели. Допускается контактное нагревание до 60—120°С, сокращающее выдержку изделий в прессе до 1,5—3 мин на 1 мм толщины цементно-стружечной плиты.
Клееные элементы коробчатого сечения из цементно-стру-жечных плит изготовляют на поточных автоматизированных линиях, выполняющих следующие операции: укладку липкой ленты с обратной стороны плит; выборку в плитах продольных пазов; нанесение на поверхность пазов клея; нагревание его лучевым способом; формирование коробчатого элемента; выдержку его под давлением до разборной прочности клеевого шва.
При изготовлении балок с деревянными поясам стенки плиты крепят к поясам клеегвоздевым способом с забивкой гвоздей пневмопистолетом на поточных линиях производительностью 11, 15, 20 м/мин.
Деревянные конструкции — Изготовление конструкций из досок, фанеры и древесных плит
Материал конструкции конкретных пригородных слоя опалубки цена пленки, с которыми сталкиваются фанеры
Пленки, с которыми сталкиваются фанеры 


Пленки, с которыми сталкиваются фанера является конкретным shuttering фанера, с гладкой, двусторонняя phenolic наложение пленки и свернутые края. Это также является универсальной и не нуждается в обслуживании оболочка панель для транспортной отрасли и сельского хозяйства. 


Основание фанеры: Тополь/березы/комби/из твердых пород дерева core 
Емкость для клея: В. В. П. Клея (Погода/ кипятить) 
Пленка цвет пленки, с которыми сталкиваются фанеры: Темно-коричневый, черный пленки. Другие цвета как желтый, зеленый, серый, светло коричневого цвета могут быть специальные заказать. 

Толщина пленки, с которыми сталкиваются фанеры: 
Мм 4, 6, 5 9 12 15 18 21 24 27 30 

Размер пленки, с которыми сталкиваются фанеры: 

1200 1200/ 1800/ 2400/ 2650/ 2700/ 3000/ 3660мм 
1200 1220/ 1525/ 2440/ 3050/ 3660мм 
1250 1250/ 2500мм 
1500 1500/ 1800/ 2400/ 2700/ 3000/ 3600мм 
1525 1525/ 2440/ 3050/ 3660мм 
1875 1525/ 2440/ 3050/ 3660/ 3700мм 

Другие размеры по заказу. Максимальная Стандартная толщина 40 мм. 
Первое измерение указывается ориентация на поверхности зерна из шпона. Фанера также может быть специальным заказан с продольной категория ориентации. 

Стандарт качества пленки, с которыми сталкиваются фанеры: EN 13986: 2004 
Структурных фанеры в внешних условий (EN636-3S) в соответствии с EN 636 
Структурных фанеры в таких внутренних условий (EN636-2S) в соответствии с EN 636 
Структурных фанеры в сухих условиях (EN636-1S) в соответствии с EN 636 
Все с формальдегида класса E1. 

Применение: 
Гладкие конкретную форму, кассета, транспортное оборудование контейнеров, со стороны прицепа пк, прицепов, раздвижные двери.
Размер | 
Упаковка | 
Кол-во/40HQ |

2440X1220X9мм | 
Поддон | 
53.05m3 |

2440X1220X12мм | 
Поддон | |

2440X1220X15мм | 
Поддон | |

2440X1220X18мм | 
Поддон | |

2440X1220X21мм | 
Поддон | |

2500X1250X9мм | 
Поддон | |

2500X1250X12мм | 
Поддон | |

2500X1250X15мм | 
Поддон | |

2500X1250X18мм | 
Поддон | |

2500X1250X21мм | 
Поддон | |

3000X1500X15мм | 
Поддон | |

3000X1500X18мм | 
Поддон | |

3000X1500X21мм | 
Поддон |
Фанера — Проектирование зданий
Фанера (иногда называемая просто «фанера») представляет собой конструкционный листовой лесоматериал, который широко используется в строительстве. Он изготавливается из трех или более тонких слоев деревянного шпона или «слоев», которые склеиваются вместе, образуя более толстый плоский лист. Он экономичен, может изготавливаться с точными размерами и относительно устойчив к деформации и растрескиванию.
Некоторые из наиболее распространенных применений фанеры включают:
Типы фанеры включают:
Фанера изготавливается из хвойных пород (таких как пихта Дугласа, сосна и красное дерево), лиственных пород (таких как ясень, клен и красное дерево) или их комбинации.
Древесина, используемая для изготовления фанеры , готовится путем пропаривания или погружения в горячую воду. Затем на токарном станке его разрезают на тонкие слои толщиной от 1 до 4 мм. Затем из него формируют большие листы.
Фанера состоит из лицевой стороны (поверхность, которая видна после установки), тыльной стороны и сердцевины (которая находится между лицевой и тыльной стороной). Слои склеиваются с помощью сильного клея, обычно фенола или мочевиноформальдегидной смолы.
Каждый слой фанеры ориентирован волокнами древесины перпендикулярно соседнему слою, повернутыми друг к другу на угол до 90 градусов.Это называется «поперечное шлифование», и именно это отличает фанеру от клееного бруса (LVL). В LVL направление слоев одинаковое, тогда как в фанере направление слоев чередуется. Обычно используется нечетное количество слоев, чтобы лист был сбалансирован, и это помогает уменьшить коробление.
Поперечное шлифование снижает склонность фанеры к расщеплению при прибивании гвоздями по краям. Он также уменьшает расширение и усадку, что улучшает стабильность его размеров и придает панелям постоянную прочность во всех направлениях.
Можно изготовить композитную фанеру , когда требуются толстые листы. В этом случае используется сердцевина из массивных деревянных брусков или ДСП с деревянным шпоном для лицевой и тыльной сторон.
Прочность облицовки лицевой и тыльной сторон можно повысить за счет добавления тонкого внешнего слоя, устойчивого к влаге, истиранию и коррозии, а также облегчающего нанесение краски и красителя. Некоторые из материалов, которые можно использовать, включают пластик, пропитанную смолой бумагу, ткань, пластик и металл.
Фанера обладает несколькими свойствами, которые делают ее полезным и популярным строительным материалом.
[править] Высокая прочность
Фанера сочетает в себе структурную прочность древесины, из которой она изготовлена, со свойствами, полученными благодаря ее многослойному дизайну. Поперечное зернение позволяет листу сопротивляться расщеплению и обеспечивает равномерную прочность для повышения стабильности.
[править] Высокий сдвиг панели
Нечетное количество слоев шпона, входящих в состав фанеры , означает, что она устойчива к изгибу.Увеличивая сдвиг панели фанеры , ее можно использовать в раскосных панелях и сборных балках.
[править] Гибкость
Фанера может быть изготовлена в соответствии с более широким диапазоном требований, чем пиломатериалы. Толщина шпона может варьироваться от нескольких миллиметров до нескольких дюймов, а количество используемых шпонов может быть увеличено по мере необходимости с точки зрения прочности.
[править] Влагостойкость
Фанера относительно устойчива к влаге и влаге благодаря типу клея, используемого в процессе скрепления.Это может сделать его подходящим для наружного использования, такого как облицовка, навесы, бетонная опалубка и морское строительство. Благодаря перекрестному ламинированию шпон не деформируется, не сжимается и не расширяется под воздействием воды и температуры.
[править] Химическая и огнестойкость
Фанера может быть обработана консервантами, которые делают ее устойчивой к коррозии при воздействии химикатов. Химические покрытия также могут повысить огнестойкость фанеры .
[править] Ударопрочность
Поперечное ламинирование придает фанере высокую прочность на растяжение, что позволяет ей выдерживать перегрузки, вдвое превышающие номинальную нагрузку. Это делает его пригодным для использования в системах полов и опалубке.
[править] Изоляция
Высокие тепло- и звукоизоляционные свойства фанеры делают ее пригодной для полов, потолков, кровли и облицовки стен.
Фанера — Проектирование зданий
Фанера (иногда называемая просто «фанера») представляет собой конструкционный листовой лесоматериал, который широко используется в строительстве.Он изготавливается из трех или более тонких слоев деревянного шпона или «слоев», которые склеиваются вместе, образуя более толстый плоский лист. Он экономичен, может изготавливаться с точными размерами и относительно устойчив к деформации и растрескиванию.
Некоторые из наиболее распространенных применений фанеры включают:
Типы фанеры включают:
Фанера изготавливается из хвойных пород (таких как пихта Дугласа, сосна и красное дерево), лиственных пород (таких как ясень, клен и красное дерево) или их комбинации.
Древесина, используемая для изготовления фанеры , готовится путем пропаривания или погружения в горячую воду. Затем на токарном станке его разрезают на тонкие слои толщиной от 1 до 4 мм. Затем из него формируют большие листы.
Фанера состоит из лицевой стороны (поверхность, которая видна после установки), тыльной стороны и сердцевины (которая находится между лицевой и тыльной стороной). Слои склеиваются с помощью сильного клея, обычно фенола или мочевиноформальдегидной смолы.
Каждый слой фанеры ориентирован волокнами древесины перпендикулярно соседнему слою, повернутыми друг к другу на угол до 90 градусов.Это называется «поперечное шлифование», и именно это отличает фанеру от клееного бруса (LVL). В LVL направление слоев одинаковое, тогда как в фанере направление слоев чередуется. Обычно используется нечетное количество слоев, чтобы лист был сбалансирован, и это помогает уменьшить коробление.
Поперечное шлифование снижает склонность фанеры к расщеплению при прибивании гвоздями по краям. Он также уменьшает расширение и усадку, что улучшает стабильность его размеров и придает панелям постоянную прочность во всех направлениях.
Можно изготовить композитную фанеру , когда требуются толстые листы. В этом случае используется сердцевина из массивных деревянных брусков или ДСП с деревянным шпоном для лицевой и тыльной сторон.
Прочность облицовки лицевой и тыльной сторон можно повысить за счет добавления тонкого внешнего слоя, устойчивого к влаге, истиранию и коррозии, а также облегчающего нанесение краски и красителя. Некоторые из материалов, которые можно использовать, включают пластик, пропитанную смолой бумагу, ткань, пластик и металл.
Фанера обладает несколькими свойствами, которые делают ее полезным и популярным строительным материалом.
[править] Высокая прочность
Фанера сочетает в себе структурную прочность древесины, из которой она изготовлена, со свойствами, полученными благодаря ее многослойному дизайну. Поперечное зернение позволяет листу сопротивляться расщеплению и обеспечивает равномерную прочность для повышения стабильности.
[править] Высокий сдвиг панели
Нечетное количество слоев шпона, входящих в состав фанеры , означает, что она устойчива к изгибу.Увеличивая сдвиг панели фанеры , ее можно использовать в раскосных панелях и сборных балках.
[править] Гибкость
Фанера может быть изготовлена в соответствии с более широким диапазоном требований, чем пиломатериалы. Толщина шпона может варьироваться от нескольких миллиметров до нескольких дюймов, а количество используемых шпонов может быть увеличено по мере необходимости с точки зрения прочности.
[править] Влагостойкость
Фанера относительно устойчива к влаге и влаге благодаря типу клея, используемого в процессе скрепления.Это может сделать его подходящим для наружного использования, такого как облицовка, навесы, бетонная опалубка и морское строительство. Благодаря перекрестному ламинированию шпон не деформируется, не сжимается и не расширяется под воздействием воды и температуры.
[править] Химическая и огнестойкость
Фанера может быть обработана консервантами, которые делают ее устойчивой к коррозии при воздействии химикатов. Химические покрытия также могут повысить огнестойкость фанеры .
[править] Ударопрочность
Поперечное ламинирование придает фанере высокую прочность на растяжение, что позволяет ей выдерживать перегрузки, вдвое превышающие номинальную нагрузку. Это делает его пригодным для использования в системах полов и опалубке.
[править] Изоляция
Высокие тепло- и звукоизоляционные свойства фанеры делают ее пригодной для полов, потолков, кровли и облицовки стен.
Фанера — Проектирование зданий
Фанера (иногда называемая просто «фанера») представляет собой конструкционный листовой лесоматериал, который широко используется в строительстве. Он изготавливается из трех или более тонких слоев деревянного шпона или «слоев», которые склеиваются вместе, образуя более толстый плоский лист. Он экономичен, может изготавливаться с точными размерами и относительно устойчив к деформации и растрескиванию.
Некоторые из наиболее распространенных применений фанеры включают:
Типы фанеры включают:
Фанера изготавливается из хвойных пород (таких как пихта Дугласа, сосна и красное дерево), лиственных пород (таких как ясень, клен и красное дерево) или их комбинации.
Древесина, используемая для изготовления фанеры , готовится путем пропаривания или погружения в горячую воду. Затем на токарном станке его разрезают на тонкие слои толщиной от 1 до 4 мм. Затем из него формируют большие листы.
Фанера состоит из лицевой стороны (поверхность, которая видна после установки), тыльной стороны и сердцевины (которая находится между лицевой и тыльной стороной). Слои склеиваются с помощью сильного клея, обычно фенола или мочевиноформальдегидной смолы.
Каждый слой фанеры ориентирован волокнами древесины перпендикулярно соседнему слою, повернутыми друг к другу на угол до 90 градусов.Это называется «поперечное шлифование», и именно это отличает фанеру от клееного бруса (LVL). В LVL направление слоев одинаковое, тогда как в фанере направление слоев чередуется. Обычно используется нечетное количество слоев, чтобы лист был сбалансирован, и это помогает уменьшить коробление.
Поперечное шлифование снижает склонность фанеры к расщеплению при прибивании гвоздями по краям. Он также уменьшает расширение и усадку, что улучшает стабильность его размеров и придает панелям постоянную прочность во всех направлениях.
Можно изготовить композитную фанеру , когда требуются толстые листы. В этом случае используется сердцевина из массивных деревянных брусков или ДСП с деревянным шпоном для лицевой и тыльной сторон.
Прочность облицовки лицевой и тыльной сторон можно повысить за счет добавления тонкого внешнего слоя, устойчивого к влаге, истиранию и коррозии, а также облегчающего нанесение краски и красителя. Некоторые из материалов, которые можно использовать, включают пластик, пропитанную смолой бумагу, ткань, пластик и металл.
Фанера обладает несколькими свойствами, которые делают ее полезным и популярным строительным материалом.
[править] Высокая прочность
Фанера сочетает в себе структурную прочность древесины, из которой она изготовлена, со свойствами, полученными благодаря ее многослойному дизайну. Поперечное зернение позволяет листу сопротивляться расщеплению и обеспечивает равномерную прочность для повышения стабильности.
[править] Высокий сдвиг панели
Нечетное количество слоев шпона, входящих в состав фанеры , означает, что она устойчива к изгибу.Увеличивая сдвиг панели фанеры , ее можно использовать в раскосных панелях и сборных балках.
[править] Гибкость
Фанера может быть изготовлена в соответствии с более широким диапазоном требований, чем пиломатериалы. Толщина шпона может варьироваться от нескольких миллиметров до нескольких дюймов, а количество используемых шпонов может быть увеличено по мере необходимости с точки зрения прочности.
[править] Влагостойкость
Фанера относительно устойчива к влаге и влаге благодаря типу клея, используемого в процессе скрепления.Это может сделать его подходящим для наружного использования, такого как облицовка, навесы, бетонная опалубка и морское строительство. Благодаря перекрестному ламинированию шпон не деформируется, не сжимается и не расширяется под воздействием воды и температуры.
[править] Химическая и огнестойкость
Фанера может быть обработана консервантами, которые делают ее устойчивой к коррозии при воздействии химикатов. Химические покрытия также могут повысить огнестойкость фанеры .
[править] Ударопрочность
Поперечное ламинирование придает фанере высокую прочность на растяжение, что позволяет ей выдерживать перегрузки, вдвое превышающие номинальную нагрузку. Это делает его пригодным для использования в системах полов и опалубке.
[править] Изоляция
Высокие тепло- и звукоизоляционные свойства фанеры делают ее пригодной для полов, потолков, кровли и облицовки стен.
Фанера — Проектирование зданий
Фанера (иногда называемая просто «фанера») представляет собой конструкционный листовой лесоматериал, который широко используется в строительстве.Он изготавливается из трех или более тонких слоев деревянного шпона или «слоев», которые склеиваются вместе, образуя более толстый плоский лист. Он экономичен, может изготавливаться с точными размерами и относительно устойчив к деформации и растрескиванию.
Некоторые из наиболее распространенных применений фанеры включают:
Типы фанеры включают:
Фанера изготавливается из хвойных пород (таких как пихта Дугласа, сосна и красное дерево), лиственных пород (таких как ясень, клен и красное дерево) или их комбинации.
Древесина, используемая для изготовления фанеры , готовится путем пропаривания или погружения в горячую воду. Затем на токарном станке его разрезают на тонкие слои толщиной от 1 до 4 мм. Затем из него формируют большие листы.
Фанера состоит из лицевой стороны (поверхность, которая видна после установки), тыльной стороны и сердцевины (которая находится между лицевой и тыльной стороной). Слои склеиваются с помощью сильного клея, обычно фенола или мочевиноформальдегидной смолы.
Каждый слой фанеры ориентирован волокнами древесины перпендикулярно соседнему слою, повернутыми друг к другу на угол до 90 градусов.Это называется «поперечное шлифование», и именно это отличает фанеру от клееного бруса (LVL). В LVL направление слоев одинаковое, тогда как в фанере направление слоев чередуется. Обычно используется нечетное количество слоев, чтобы лист был сбалансирован, и это помогает уменьшить коробление.
Поперечное шлифование снижает склонность фанеры к расщеплению при прибивании гвоздями по краям. Он также уменьшает расширение и усадку, что улучшает стабильность его размеров и придает панелям постоянную прочность во всех направлениях.
Можно изготовить композитную фанеру , когда требуются толстые листы. В этом случае используется сердцевина из массивных деревянных брусков или ДСП с деревянным шпоном для лицевой и тыльной сторон.
Прочность облицовки лицевой и тыльной сторон можно повысить за счет добавления тонкого внешнего слоя, устойчивого к влаге, истиранию и коррозии, а также облегчающего нанесение краски и красителя. Некоторые из материалов, которые можно использовать, включают пластик, пропитанную смолой бумагу, ткань, пластик и металл.
Фанера обладает несколькими свойствами, которые делают ее полезным и популярным строительным материалом.
[править] Высокая прочность
Фанера сочетает в себе структурную прочность древесины, из которой она изготовлена, со свойствами, полученными благодаря ее многослойному дизайну. Поперечное зернение позволяет листу сопротивляться расщеплению и обеспечивает равномерную прочность для повышения стабильности.
[править] Высокий сдвиг панели
Нечетное количество слоев шпона, входящих в состав фанеры , означает, что она устойчива к изгибу.Увеличивая сдвиг панели фанеры , ее можно использовать в раскосных панелях и сборных балках.
[править] Гибкость
Фанера может быть изготовлена в соответствии с более широким диапазоном требований, чем пиломатериалы. Толщина шпона может варьироваться от нескольких миллиметров до нескольких дюймов, а количество используемых шпонов может быть увеличено по мере необходимости с точки зрения прочности.
[править] Влагостойкость
Фанера относительно устойчива к влаге и влаге благодаря типу клея, используемого в процессе скрепления.Это может сделать его подходящим для наружного использования, такого как облицовка, навесы, бетонная опалубка и морское строительство. Благодаря перекрестному ламинированию шпон не деформируется, не сжимается и не расширяется под воздействием воды и температуры.
[править] Химическая и огнестойкость
Фанера может быть обработана консервантами, которые делают ее устойчивой к коррозии при воздействии химикатов. Химические покрытия также могут повысить огнестойкость фанеры .
[править] Ударопрочность
Поперечное ламинирование придает фанере высокую прочность на растяжение, что позволяет ей выдерживать перегрузки, вдвое превышающие номинальную нагрузку. Это делает его пригодным для использования в системах полов и опалубке.
[править] Изоляция
Высокие тепло- и звукоизоляционные свойства фанеры делают ее пригодной для полов, потолков, кровли и облицовки стен.
APA – Ассоциация производителей инженерной древесины
Оригинальный продукт из искусственной древесины
Основы из фанеры
Фанера на протяжении десятилетий является одним из самых признанных и надежных материалов для деревянного строительства. Фанерные панели, изготовленные из тонких листов поперечно-ламинированного шпона и склеенных под воздействием тепла и давления с помощью сильного клея, обладают превосходной размерной стабильностью и отличным соотношением прочности к весу, а также обладают высокой устойчивостью к ударам, химическим веществам и изменениям температуры и влажности окружающей среды. . Фанера, производимая заводами-членами APA, доступна в самых разных классах внешнего вида, от гладких, натуральных поверхностей, подходящих для отделочных работ, до более экономичных сортов, используемых для обшивки.Имея более дюжины распространенных толщин и более двадцати различных сортов, фанера хорошо подходит для множества требовательных применений.
Общие области применения фанеры
Фанера под торговой маркой APA подходит для различных конечных применений, включая черновой пол, однослойный пол, обшивку стен и крыши, обшивку потолка/палубы, конструкционные изолированные панели, морское применение, сайдинг, перегородки из деревянных двутавровых балок, опалубку бетона, поддоны, промышленные контейнеры, антресоли и мебель.
Категории характеристик панели
5/16, 3/8, 15/32, 1/2, 19/32, 5/8, 23/32, 3/4, 7/8, 1, 1-1/8.
Размеры панели
4 x 8 футов, 4 x 9 футов, 4 x 10 футов
Знак качества APA
Товарные знакиAPA появляются только на продуктах, произведенных заводами-членами APA. Знак означает, что качество панели подлежит проверке посредством аудита APA — процедуры, разработанной для обеспечения соответствия производства стандартам производительности APA или стандарту, указанному в знаке.
Фанерные публикации
Справочник по продукту: Шлифованная фанера
Описывает технические характеристики, преимущества, области применения и рекомендации по отделке шлифованной фанеры. Включает примеры товарных знаков и пояснения.
Скачать >
Руководство по продукту
: Панели с рейтингом производительности
Описывает стандарты производительности для конструкционных деревянных панелей и составов различных типов панелей APA с обозначениями Performance Rated для обшивки с рейтингом APA, Sturd-I-Floor с рейтингом APA и сайдинга с рейтингом APA. В нем также описаны типичные области применения, в которых используются панели с рейтингом производительности, и представлена обновленная информация о товарных знаках и категориях производительности.
Скачать >
Библиотека ресурсов
Доступ к полному списку публикаций APA о фанере в библиотеке ресурсов APA.
Разница между конструкционной и неконструкционной фанерой ⋆ 🌲 ThePlywood.com
Термин «фанера» на самом деле является очень общим термином, хотя то, что большинство из нас считает фанерой, представляет собой конструкционное деревянное изделие, изготовленное из ламинированного шпона, в котором смежные слои уложены перпендикулярно друг другу.Тем не менее, если это фанера, то же самое можно сказать и о OSB, MDF и ряде других листовых инженерных изделий, которые не вписываются в образ традиционной фанеры.
Фанерабывает разных типов и может быть классифицирована по-разному. Среди этих способов мы сталкиваемся с терминами «структурный» и «неструктурный». Хотя может показаться, что это не имеет большого значения, на самом деле это не так. В то время как структурная фанера может использоваться для неструктурных приложений, не рекомендуется использовать неструктурную фанеру там, где требуется конструкционная фанера.
Для сравнения конструкционной и неконструкционной фанеры мы говорим о традиционных фанерных изделиях, а не о ДСП, ДСП или ДВП. Все виды фанеры бывают конструкционными или неконструкционными, в зависимости от их предполагаемого использования.
Так в чем разница?
Когда мы говорим о разнице между конструкционной и неконструкционной фанерой, мы не говорим о разных породах древесины, хотя в некоторых случаях могут быть различия в используемой древесине.Вместо этого мы говорим о различиях в типах клеев, используемых для скрепления слоев дерева. Это критическая разница, потому что некоторые типы клеев более устойчивы к атмосферным воздействиям, чем другие.
Когда мы говорим о конструкционной фанере, мы в основном имеем в виду плиты для наружных работ с клеями, которые могут выдерживать некоторое воздействие влаги и перепадов температуры. В них используются клеи A-Bond или B-Bond. Клеи, относящиеся к категории A-Bond, изготавливаются из фенолоформальдегидной смолы, а клеи, относящиеся к категории B-Bond, используют меламин-мочевину-формальдегид.Из этих двух материалов A-Bond более влагостойкий, чем B-Bond.
С другой стороны, неструктурные фанерные панели изготавливаются из клеев C-Bond и D-Bond; карбамидоформальдегидные смолы. Они не подходят для наружных работ, так как такие клеи портятся под воздействием влаги и перепадов температуры.
На более очевидной основе существуют определенные категории фанеры, которые явно относятся к конструкционной фанере. К ним относятся фанера для наружных работ, фанера RTD, фанера BWP и фанера, обработанная давлением.Все они были разработаны с целью придания фанере хотя бы некоторой степени влаго- и термостойкости. С другой стороны, изделия из декоративной фанеры, предназначенные для применений, где важен внешний вид, например, фанера из твердой древесины, явно не являются конструкционной фанерой.
Области применения, требующие конструкционной фанеры
Большая часть фанеры, используемой в жилищном строительстве, является структурной фанерой. Проще говоря, все, что вы можете найти, где строительные нормы и правила определяют материалы фанеры и толщину материала, требует конструкционной фанеры, особенно если эти материалы могут в конечном итоге подвергнуться воздействию дождя до того, как дом будет высушен.Это включает в себя пол, обшивку стен и обшивку крыши.
Вы также найдете конструкционную фанеру, используемую в местах, которые могут не указываться в строительных нормах, но все же являются частью конструкции дома, например, для крепления крыш и полов. Если вы сделаете свои собственные фермы, используя фанерные косынки, чтобы скрепить вместе 2 x 4 дюйма, тогда вам подойдет конструкционная фанера.
Но это не единственные места, где вы можете использовать конструкционную фанеру. Он одинаково полезен для упаковки ящиков, ящиков для хранения, навесов для хранения, уличной мебели и детского игрового оборудования на открытом воздухе, такого как игровой домик.
Области применения, где уместна неструктурная фанера
Обычно существует разница между типами неструктурной фанеры C-Bond и D-Bond. По большей части фанера C-Bond обеспечивает более чистую отделку с меньшим количеством сучков и других дефектов. Из этих двух материалов фанера C-Bond обладает более высокой влагостойкостью, чем D-Bond, хотя и не считается влагостойкой продукцией.
Любые отделочные работы, при которых видна фанера, вероятно, потребуют использования неконструкционной фанеры, поскольку конструкционная фанера не производится с учетом эстетических требований.Вне зависимости от того, идет ли речь о фанере лиственных пород или о фанере хвойных пород класса АВ, основное внимание уделяется готовой лицевой поверхности, а не термостойкости или влагостойкости изделия.
Морская фанера по сравнению с другой конструкционной фанерой
Люди постоянно неправильно понимают разницу между морской фанерой и другими конструкционными изделиями из фанеры. Хотя морская фанера считается конструкционной фанерой, не вся конструкционная фанера считается морской фанерой. Чтобы считаться морской фанерой, она должна соответствовать очень специфическому набору критериев.
К морской фанере предъявляются три основных требования, которые отличают ее от другой конструкционной фанеры. Во-первых, во внутренних слоях шпона не допускается наличие пустот. Пустоты могут стать причиной расслаивания, особенно когда они заполняются влагой. Во-вторых, морская фанера должна изготавливаться с использованием водостойкого клея. Наконец, для морской фанеры требуется лицевой шпон более высокого качества, чем тот, который обычно встречается для конструкционной фанеры для наружных работ.
Большая часть морской фанеры будет производиться в соответствии со стандартом WBP (устойчивость к кипячению в воде), хотя это не является обязательным требованием.Даже морская фанера, не имеющая рейтинга WBP, вероятно, будет соответствовать этому требованию; это просто означает, что производитель не потратил деньги на тестирование своего продукта.
Хотя морская фанера изначально была разработана для использования в судостроении, она нашла применение и во многих других областях. Высокая устойчивость к влаге, которую предлагает эта фанера, делает ее идеальным выбором для широкого спектра применений, от полов в автобусах до садовой мебели.
Различные типы фанеры, сложенные вместеFormly vs.Морская фанера
Другим специфическим изделием из конструкционной фанеры является формаль. Этот фанерный продукт поднимает идею влагостойкой фанеры на новый уровень, поскольку он используется там, где он всегда будет в контакте с влагой.
Formly — это специализированный продукт из фанеры, предназначенный для изготовления бетонных форм. Для использования в этом приложении фанера должна быть не только очень влагостойкой, но и иметь водонепроницаемое внешнее покрытие, которое позволит легко отделить ее от затвердевающего бетона.До появления формы это достигалось за счет использования фанеры с высокой влагостойкостью, такой как морская фанера, и покрытия ее маслом, обычно отработанным моторным маслом.
Сегодняшний формпли — это фанера из хвойных пород для наружных работ, состоящая из большого количества слоев, скрепленных клеем типа А или В. Лицевая и обратная стороны шпона покрыты бумагой, пропитанной фенольной смолой, что придает ей гладкую поверхность, к которой бетон не прилипает. Он не соответствует трем требованиям к фанере морского класса, но в некоторых отношениях может считаться превосходящим их.
Привлекательный внешний вид формы делает ее полезной не только для изготовления бетонных форм. Это включает в себя изготовление кухонных шкафов и мебели. Производители извлекли выгоду из этого, изготовив формы в различных цветах.
10 нетрадиционных фанерных проектов, которые показывают светлое будущее материалов 20-го века
10 нетрадиционных фанерных проектов, которые показывают светлое будущее материалов 20-го века
© James Dow Sharehare-
Facebook
-
Twitter
-
Pinterest
-
Whatsapp
-
Почта
Или
https://www.archdaily.com/898644/10-нетрадиционные-фанерные-проекты-которые-показывают-светлое-будущее-20-го века-материалы+ 27
С 1928 года фанера продается в стандартных листах шириной 4 фута. основным продуктом обычного строительства на протяжении почти столетия. Прочные, легко режущиеся, легкие и способные создавать эффективный барьер, фанера и другие инженерные панели, такие как OSB, ДСП и МДФ, широко распространены, особенно для их использования в качестве материала для обшивки в воздушных шарах и строительных системах деревянного каркаса.Лодки, самолеты и даже автомобильные рамы исторически строились из фанеры, предшествующей (или заменяющей) стали, алюминию и стекловолокну. Как простой материал, с которым можно манипулировать и формировать самыми разными способами, листовая фанера также использовалась в мебели и архитектурных проектах модернистами, включая Чарльза и Рэя Имза, Ээро Сааринена, Алвара Аалто и Марселя Брейера.
Инсталляция TWIST на выставке Timber Expo, Бирмингем, NEC.. Изображение © Patrick TanhuancoТехнологии деревообработки, основанные на склеивании тонких досок пиломатериалов, восходят к Древнему Египту, но современные листы фанеры стали возможными только с середины 1800-х годов, когда Иммануил Нобель (отец изобретателя динамита и лауреата премии Альфреда Нобеля) изобрел токарно-карусельный станок.Этот фрезерный инструмент перерабатывал сырую древесину в сырье для фанеры, расчищая целые бревна на тонкие листы шпона (подобно рулону туалетной бумаги, вытягиваемому из картонной трубки). По сей день фанера производится путем укладки слоев шпона, склеивания их вместе, а затем соединения их в прессе с ориентацией волокон каждого слоя, повернутой на 90 градусов по отношению к слою под ним или над ним, для равномерной прочности по каждому измерению. лист. Другие инженерные листы изготавливаются из древесных частиц разного размера и ориентации, а не из листов шпона, но аналогичным образом склеиваются и прессуются.
© Jason MandellaСегодня инженерные деревянные листы используются в строительстве любого масштаба, но этот материал также получил клеймо визуального символа городской упадка. Его обычно используют для заклеивания разбитых окон и дверей заброшенных домов; практика, которая была проблематизирована на основе эстетики и предупреждения преступности. Теперь FEMA рекомендует использовать вместо них прозрачную пластиковую пленку, а штат Огайо и город Феникс, штат Аризона, даже запретили использование фанеры для обшивки пустующих зданий.Однако современные технологии проектирования создали новое будущее для фанеры как архитектурного материала, и дизайнеры внезапно открывают для себя захватывающие новые способы создания конструкций из фанеры.
© Marcin DondajewskiНа протяжении большей части истории своего использования фанера обычно использовалась как целые листы или разрезалась на все еще прямоугольные неполные листы с помощью панельной пилы, настольной пилы или циркулярной пилы. Однако с относительно недавним изобретением фрезерования с ЧПУ и аналогичных компьютеризированных методов резки стало возможным многократно вырезать листы искусственной древесины в строго контролируемые геометрически совершенные формы с точностью, с которой ручная резка никогда не сможет сравниться.Это открыло мир новых способов использования деревянных листов в проектах, создавая возможности для превращения плоского материала в трехмерные формы путем укладки листов в виде параллельных плоскостей или сшивания их вместе. Фрезерные станки с ЧПУ также могут превращать древесные листы в перфорированные или перфорированные экраны, вырезанные по тщательно разработанным шаблонам, и дизайнеры обнаружили, что стратегические разрезы или пропилы могут позволить листам изгибаться и скручиваться стабильным и контролируемым образом для создания скульптурных форм и удобства обмена Файлы САПР позволяют создавать концепции зданий с открытым исходным кодом, такие как WikiHouse.
Предоставлено AREA и лабораторией Electrotexture Lab. Эти толстые панели, отформованные вместе из досок из цельного пиломатериала, а не из тонкого шпона фанеры, обещают несущую способность железобетона, сохраняя при этом преимущества устойчивости натуральной древесины. В то время как CLT, древесно-пластиковые гибриды и обещание революционных новых продуктов, таких как прозрачная древесина, могут выглядеть как будущее строительных материалов, эти проекты показывают, как творческие подходы к дизайну и новаторское использование современных технологий сделали инженерные деревянные листы жизненно важным материалом.