Как и из чего делают фанеру?, Советы и статьи от Стройка Снаб
Как и из чего делают фанеру?
Самая лучшая фанера получается именно из берёзы и делают ее только в России. Это древесина настолько ценная, что брёвна хранящиеся на бирже защищают даже от солнечного света, чтобы ультрафиолет не выслушивал торцы деревьев. На завод берёза попадает виде распиленных на равные части брёвен. Из них формируют нечто вроде вязанки, схваченной массивными металлическими цепями. Огромную кипу осторожно перемещают в бассейн с очень горячей водой. Здесь древесину основательно пропаривают. Бурая пена — деготь, который выделяет берёза, он защищает дерево от гниения, а также используется для приготовления знаменитой мази Вишневского. Спустя несколько часов почерневшие бревна выгружают из бассейна и оставляют, чтобы выровнять температуру. Тепло должно переместиться от коры к самому ядру. Берёза порода настолько плотная и тяжелая, что даже тонет в воде зато, если древесину распарить она станет мягкой и пластичной. Чуть позже вы поймете для чего её размягчают. Теперь начинается самое интересное. Чурак отправляется на лущильный станок, здесь брёвна вращаются вокруг своей оси. А лущильный нож срезает с них кору и снимает с древесины широкую стружку двигаясь по архимедовой спирали. В 300-ом году до нашей эры Архимед вывел формулу идеальной спирали, она должна вращаться вокруг точки с каждым новым витком приближаясь к ней на одинаковое расстояние. Похожим принципом пользуются паук когда плетёт свою паутину. Архимедова спираль позволяет срезать с бревна идеально ровный слой древесины. Представьте, что обычный карандаш это ствол дерева, а канцелярская точилка лущильный нож. Процесс лущения выглядит почти так же как заточка карандаша, правда стружка срезается не с кончика, а со всего цилиндра. Стружка снятая с бревна называется шпон. С одного чурака получается Лента шпона длиной в 16 метров. Древесина все еще влажная и теплая ,если бревно не пропаривать , драгоценная стружка при лущении будет рваться и ломаться. Кстати, только из российской берёзы делают самый тонкий шпон в мире толщиной всего в 1 мм. Например в Америке, где березы не растут фанеру производят из сосны и пихты , а из такой мягкой хвойной древесины тонкого шпона не получается. Снятую с березы стружку раскраивают на гильотине, а затем отправляют в газовую сушилку. Потоки горячего воздуха удаляют из древесины лишнюю влагу, чтобы будущая фанера не расслаивалась и не пузырилась. Первые листы фанеры были сделаны в пятнадцатом веке до нашей эры древними египтянами. Они научились делать подобие фанеры от безысходности. Лесов в Египте всегда не хватало, поэтому дерево привозилось из далека и стоило очень-очень дорого. Что же делает фанеру настолько прочной? Мы уже выяснили как с березовых бревен пропаренных в бассейне с кипятком снимают стружку. Именно из этих тончайших листов шпона толщиной чуть больше миллиметра будут делать крепкие листы фанеры. Если на древесине остался след от сучка, березовый шпон отправляют в пачиночный станок. Машина вырубает дефект и мгновенно ставит на его место аккуратную заплатку.
А вот теперь ключевой момент — сборка фанеры. Для листа толщиной в сантиметр нужно склеить семь слоёв березового шпона. Такой способ склеивания фанеры из нескольких листов в конце 19 века называли «русским». Раньше для склеивания использовали состав на основе казеина — молочного белка. Его получали из молока и сыра. Казеиновая фанера была прочной, но сильно впитывала влагу и промокала. Сегодня шпон склеивают с помощью формальдегидной смолы. Благодаря ей Фанера становится влагостойкой. Обычная мука делает смолу гуще а древесину прочнее. Мел не позволяет клею проникать на поверхность и портить товарный вид. У фанеры всегда нечетное число слоев. Клеем пропитываются лишь четные листы шпона, которые при сборке чередуются с нечетными сухими. Но самое главное все слои взаимно перпендикулярны. Именно это делает фанеру такой прочной. У одного листа шпона волокна расположены вдоль, у следующего поперёк. Слой за слоем фанера увеличивает ударную вязкость, способность поглощать механическую энергию. Перекрестное расположение листов делает древесину устойчивой к деформации. Собранные в пакеты слои шпона на несколько минут отправляют в холодный пресс где сухие и проклеенные листы схватываются друг с другом. Это подготовительный этап перед горячим прессованием. Каждый лист будущей фанеры загружают в подъемник, который транспортирует их в 20-ти пролетный горячий пресс. На каждом его этаже размещается фанерный полуфабрикат. Под большим давлением шпон накрепко склеивается друг с другом. Из-за высокой температуры клей даже и кипит, а фанера испускает горячий пар. Всего за 10 минут бутерброд из тончайшей березовой стружки и клея превращается в сверхпрочный материал, который в течение суток будет остывать. За это время завершится процесс полимеризации клея. Теперь остается лишь обрезать неровные края шпона и придать изделию привычный вид. Сложно поверить, что обычная фанера, на которой многие в детстве катались с горки на самом деле уникальный сверхпрочный материал. Вы удивитесь, но из древесины можно сделать нечто еще более прочное, например, древесно-слоистый пластик. Его называют бакелитовой фанеры или Дельта древесиной. Она настолько прочная, что может заменить бронзу. Из бакелитовой фанеры делают подшипники скольжения и бесшумные зубчатые передачи. Дельта-древесина сопротивляется любому виду деформации, не скалывается, не ломается и не растягивается. Прочным как цветные металлы дерево становится благодаря бакелитовому лаку. Он делает материал почти неуязвимым и можно пользоваться даже под водой. Обычный березовый шпон покрывается лаком с обеих сторон и отправляется в сушилку. Здесь при температуре 100 градусов он полностью впитывается в древесину. Если в обычной фанере клей нанесен лишь на чётные слои, то у древесного пластика лаком пропитан каждый лист шпона. Пласты разделяют металлическими листами и отправляют под пресс. Он часами сжимает Дельта-древесину оказывает давление в 6 раз сильнее чем на обычную фанеру. Кстати, количество слоев у древесного пластика доходит до сотни.
Стройка-Снаб интернет гипермаркет предлагает фанеры разных видов и качеств. На нашем сайте Вы можете приобрести фанеры фк, фсф, фоф, дсп, двп, осп 3, osb 3, ламинированную фанеру и многое другое. Фанера является прочным листовым материалом применяемым в мебельном производстве и в строительстве. Изготавливаются фанеры из хвойных и лиственных пород древесины. Виды фанер разделяются в зависимости от степени обработки материала, могут быть шлифованные и нешлифованные.
Покупая фанеры очень важным аспектом является учет сорта, качества обработки и толщину. Шлифованная фанера применима в строительно монтажных и отделочных работах, имеет красивую гладкую текстуру, благодаря чему имеет большой спрос в мебельном производстве. Шлифованная фанера легка в обработке, обладает водоотталкивающим свойствам и имеет твердую поверхность. Все эти преимущества данному материалу позволяют иметь огромный спрос при любом строительстве.
Дзержинский, Нахабино, Звенигород, Голицыно, Сходня.
ПЕРЕЙТИ В КАТАЛОГ ТОВАРОВ→
порода древесины, количество слоёв шпона, клей
Каждый строительный материал имеет какую-то классификацию – деление по ряду технических характеристик, совокупность которых определяет целесообразность его использования для решения каких-то частных конкретных задач. Фанера в этом плане не является исключением – в настоящее время производится довольно много ее разновидностей и разные виды используются в разных целях. Чтобы определить, какой именно тип фанеры нужен в конкретном случае, нужно знать основные критерии, по которым она классифицируется.
Порода древесины для изготовления фанеры
Самый первый признак, по которому этот материал делится на разные виды – порода древесины, которая использовалась при нарезке шпона. В основном его производство осуществляется из березы или из хвойных пород – пихта, сосна, ель. На практике часто применяются оба сорта, тогда тип фанеры определяется по материалу ее лицевых слоев. Так, если сердцевина сделана из хвойных пород, но снаружи она облицована слоями из березы, то такая фанера будет называться березовой. Поскольку древесина березы в сравнении с хвойными породами является относительно дорогой, то большую часть фанеры, производимой у нас в стране, составляет фанера хвойная, а большинство березовой имеет именно такую структуру – середина у нее делается из шпона, нарезанного из сосны или ели.


В некоторых случаях для повышения эстетических свойств изделия наружные слои делаются из более благородных пород дерева – например, из кедра. Такая продукция используется сугубо в декоративных целях, она идет на изготовление мебели и применяется во внутренней отделке помещений.
Количество слоёв шпона
Второй критерий – количество слоев шпона. Оно начинается с трех, при этом оно всегда нечетное. Это объясняется особенностями производства фанеры – для увеличения механической прочности листа направление волокон листов шпона при укладке чередуется, а нечетность позволяет сохранять одинаковый внешний вид с обеих сторон. Исключение составляет четырехслойная – у нее направление волокон двух внутренних слоев совпадает, а наружные укладываются перпендикулярно внутренним. На заводах по производству фанеры необходимая толщина фанеры достигается только соединением нужного количества слоёв шпона.
Клей
Третий важный критерий – пропитка или клей. Крепкая износостойкая фанера получается в результате использования клеящего состава на основе формальдегидных смол. Это фанера ФСФ, цена которой относительно невысока, что делает ее очень популярным материалом в строительной сфере. Фанера ФК пропитывается карбамидным клеем. Она имеет меньшую влагостойкость, чем ФСФ, что ограничивает возможности ее применения для наружных работ, но она более экологична, что позволяет использовать ее при внутренней отделке. Заметим, что фанера ФК также немного дешевле фанеры марки ФСФ. Есть еще множество видов пропитки, предназначенных для создания фанеры, эксплуатируемой в условиях жесткого климата или повышенной влажности, но эти две являются самыми популярными.
Производство фанеры — как всё организовано, процесс производства
Фанера это многослойный строительный материал, изготавливается путём склеивания специально подготовленного шпона.
Место, где производят фанеру, т. е. фанерный завод, называют ещё и «биржей». Только в обороте здесь не ценные бумаги и валюта, а брёвна. Берёза, сосна, ель.
Вот они как раз и являются ценностью. Укрывают их в том числе и от солнечного света — чтобы ультрафиолетовые лучи не высушивали торцы брёвен.
Возьмем, для примера, берёзу — фанера из неё получается самой прочной.
На завод дерево попадает в виде распиленных на равные части брёвен — чураков. Из них формируют нечто вроде вязанки, «перевязанных» массивными металлическими цепями.
Эту огромную «вязанку» осторожно перемещают в бассейн с очень горячей водой. Здесь древесину основательно пропаривают.
При этом на поверхности дерева появляется бурая пена. Это — деготь, который выделяет береза. Он защищает дерево от гниения. А также используется при изготовлении знаменитой «мази Вишневского».
Через несколько часов почерневшие брёвна выгружают из бассейна и оставляют на воздухе, чтобы выровнять температуру чурака — тепло должно переместиться от коры к самой сердцевине.
Берёза — порода настолько плотная и тяжелая, что даже тонет в воде. Но если древесину распарить — она станет мягкой и пластичной.
После распаривания чурак направляется на лущильный станок. Здесь брёвна вращаются вокруг своей оси, а лущильный нож срезает с них кору и снимает с древесины широкую стружку, двигаясь по архимедовой спирали.
Небольшой экскурс в историю: В 300-ом году до н. э. Архимед вывел формулу идеальной спирали — она должна вращаться вокруг точки, с каждым новым витком приближаясь к ней на одинаковое расстояние.
Похожим принципом пользуется паук, когда плетет свою паутину.
Архимедова спираль позволяет срезать с бревна идеально ровный слой древесины. Можно сравнить это с заточкой деревянного карандаша. Карандаш — это ствол дерева, а канцелярская точилка — лущильный нож. Процесс лущения выглядит почти так же, как заточка карандаша. Правда стружка срезается не с кончика, а со всего цилиндра. Эта стружка, снятая с бревна, и называется шпоном.
Длина шпона, снятая с одного чурака, может достигать 16-ти метров. Какое-то время шпон всё ещё остается влажным и теплым. Потому, что если бревно не пропаривать, драгоценная стружка при лущении будет рваться и ломаться. Самый тонкий шпон в мире делают только из Российской березы — толщиной всего в 1 мм.
В Америке, например, где березы почти нет, фанеру делают из сосны и пихты. В Китая — из тополя. А из такой мягкой хвойной древесины тонкого шпона не получается.
Снятую стружку раскраивают на гильотине и отправляют в газовую сушилку. Потоки горячего воздуха выгоняют из древесины лишнюю влагу, чтобы будущая фанера не расслаивалась и не пузырилась.
Кстати, разбить рукой обычный тонкий фанерный лист очень сложно. И под силу очень немногим большим мастерам Тамеши-вари (искусство разбивания твёрдых предметов). Если деревянная доска ломается за счет разрушения структуры волокон древесины под действием механической энергии удара, то тонкий лист фанеры эту энергию не просто поглощает, а возвращает мощь удара.
Устранение дефектов шпона
Если на древесине остался след от сучка — березовый шпон отправляют на починочный станок. Машина вырубает дефект и одновременно ставит на его место заплатку.
Теперь — ключевой момент. Сборка фанеры. Для листа толщиной 1 см. нужно склеить 7 слоев шпона. Такой способ склеивания фанеры из нескольких листов в конце 19-го века называли «Русским». Раньше для склеивания использовали состав на основе казеина — молочного белка. Его получали из молока и сыра. Казеиновая фанера была прочной, но сильно впитывала влагу и промокала.
Сегодня шпон склеивают с помощью формальдегидной смолы — благодаря ей фанера становится влагостойкой. Обычная мука делает смолу гуще, а древесину прочнее. Мел не позволяет клею проникать на поверхность и портить товарный вид.
У фанеры всегда нечетное число слоев. Клеем пропитываются лишь четные листы шпона, которые при сборке чередуются с сухими нечетными. Но самое главное — все слои взаимно перпендикулярны. Именно это делает фанеру такой прочной. У одного листа шпона волокна расположены вдоль. У следующего — поперек. Слой за слоем фанера увеличивает ударную вязкость — способность поглощать механическую энергию. Перекрестное расположение листов делает древесину устойчивой к деформации.
Собранные в пакеты слои шпона на несколько минут отправляют в холодный пресс, где сухие и проклеенные листы схватываются друг с другом. Это — подготовительный этап перед горячим прессованием. Каждый лист будущей фанеры загружают в подъемник, который транспортирует их в 20-ти пролетный горячий пресс. На каждом его этаже размещается фанерный полуфабрикат. Под большим давлением шпон накрепко склеивается друг с другом. Из-за высокой температуры клей даже кипит, а фанера испускает горячий пар. Всего за 10 минут бутерброд из тончайшей березовой стружки и клея превращается в сверхпрочный материал, который в течение суток будет остывать. За это время завершится процесс полимеризации клея.
Теперь остается лишь обрезать неровные края шпона и придать изделию привычный вид. Сложно поверить, что на самом деле обычная фанера — уникальный сверхпрочный материал.
Бакелитовая фанера
Оказывается, из обычной древесины можно сделать еще нечто более прочное! Например — древесно-слоистый пластик. Его называют бакелитовой фанерой. Или — дельта-древесиной. Она настолько прочная, что может заменить бронзу. Из бакелитовой фанеры делают подшипники скольжения и бесшумные зубчатые передачи. Дельта-древесин сопротивляется любому виду деформации, не скалывается, не ломается и не растягивается.
Прочным, как цветные металлы, дерево становится благодаря бакелитовому лаку. Он делает материал почти неуязвимым. Им можно пользоваться даже под водой. Обычный березовый шпон покрывается лаком с обеих сторон и отправляется в сушилку. Здесь при температуре в 100 градусов он полностью впитывается в древесину. Т. е. у древесного пластика лаком пропитан каждый лист шпона. Пласты разделяют металлическими листами и отправляют под пресс. Он часами сжимает дельта-древесину при давлении в 6 раз большем, чем при изготовлении обычной фанеры. Количество слоев у древесного пластика доходит до сотни.
Из легкой и сверх прочной дельта-древесины делали фюзеляжи и крылья летательных аппаратов. Среди них есть первый цельно деревянный Советский истребитель по прозвищу «Рояль» и немецкая ракета класса «воздух-воздух» времен 3-го рейха.
Фанера — это… Что такое Фанера?
Фанера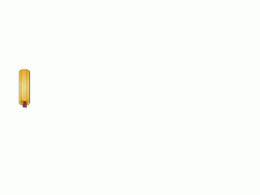
Фане́ра (древесно-слоистая плита) — многослойный строительный материал, изготавливаемый путём склеивания специально подготовленного шпона. Количество слоёв шпона обычно нечётное, от 3 и более. Для повышения прочности фанеры слои шпона накладываются так, чтобы волокна древесины были строго перпендикулярны предыдущему листу.
Применение
Самодельный вездеход «Каракат» с кузовом из фанерыКлассификация
Фанера называется продольной, если волокна в лицевых слоях направлены вдоль длинной стороны, в противном случае — поперечной
Фанера из древесины как твёрдых, так и мягких пород выпускается нескольких типов и сортов, которые различаются назначением, сроком службы, внешним видом и стоимостью.
По предназначению — строительная, промышленная, упаковочная, мебельная, и конструкционная.
По видам фанеру часто разделяют на два популярных вида — ФК (влагостойкая) и ФСФ (повышенной влагостойкости).
По типу обработки — ламинированная.
По внешнему виду (определяется количеством сучков на квадратный метр поверхности наружного слоя шпона): E (элита), I, II, III, IV.
По материалу, из которого изготовляется
- Хвойная фанера (изготавливается из шпона хвойных пород деревьев: лиственницы, сосны, пихты, ели). Иногда для изготовления фанеры используется шпон кедра — такая фанера используется в декоративных целях. Для хвойной фанеры обязательным является содержание хвойного шпона в наружных слоях — внутренние могут содержать шпон лиственных пород древесины.
- Берёзовая фанера (изготавливается из шпона берёзы) получила распространение практически во всех областях, но из-за относительно более высокой стоимости в строительстве используется не так широко, как хвойная.
По количеству слоев

- трёхслойная
- пятислойная
- многослойная
В основном листы фанеры имеют нечётное количество слоёв шпона: в этом случае шпон расположен симметрично относительно среднего слоя. Если слоёв шпона в фанере четыре, то центральные слои располагают и склеивают перпендикулярно наружным, что увеличивает общую прочность и стойкость к деформации.
По пропитке
Влагостойкая фанера — материал, обработанный специальным образом для увеличения сопротивления влаге. Максимально увеличить влагостойкие характеристики фанеры может помочь ламинирование.
- ФСФ (фанера, изготавливаемая с применением смоляного фенолформальдегидного клея). Эта фанера характеризуется относительно высокой износоустойчивостью, механической прочностью и высокой влагостойкостью. ФСФ — один из самых популярных видов фанеры, используется в строительстве, производстве, кровельных работах.
- ФК (фанера, получаемая при приклеивании шпонов карбамидным клеем). Обладая меньшими влагостойкими характеристиками, ФК используется преимущественно при внутренней отделке помещений, в мебельном производстве, при изготовлении деревянной тары, при работе с конструкциями внутри помещения.
- ФБ (фанера, пропитанная бакелитовым лаком, впоследствии склеивается). Этот вид обладает максимальной сопротивляемостью воздействию агрессивной среды и может использоваться в условиях тропического климата, при повышенной влажности и даже под водой.
- БС (фанера, пропитанная бакелитовым клеем, С — спирторастворимый). Эта фанера обладает фантастическими свойствами — сверхвысокой прочностью, стойкостью к агрессивным средам, гибкостью, упруготью, водонепроницаема, не гниет, не раскисает. Ее ещё называют называют авиационная фанера за то, что раньше использовалась только в авиа- и судостроении.
- БВ (фанера, пропитанная бакелитовым клеем, В — водоорастворимый). Эта фанера обладает теми же свойствами, что и предыдущая, за исключением влагостойкости, т.к. клей, применяемый при склеивании слоев — водорастворим.
По виду обработки поверхностей
- НШ — нешлифованная фанера
- Ш1 — материал, шлифованный с одной стороны
- Ш2 — материал шлифованный с двух сторон
Виды и сорта фанеры
В настоящий момент ГОСТы предусматривают наличие пяти сортов фанеры, которые отличаются главным образом наличием и количеством допустимых дефектов обработки[1].
- сорт Е (элита). Дефекты не допускаются, кроме незначительных изменений случайного характера в строении древесины;
- сорт I. Максимальная длина покоробленности или трещин для фанеры первого сорта не должна превышать 20 мм;
- сорт II. Допускаются трещины до 200 мм, вставки из древесины, просачивание клея площадью до 2 % от общей площади листа фанеры;
- сорт III. Допускаются червоточины до 10 шт. на квадратный метр при диаметре каждой не более 6 мм; общее количество перечисленных пороков не может быть больше 9;
- сорт IV. Фанера 4 сорта является крайне низкокачественной. Такая фанера может иметь следующие пороки: частично сросшиеся и выпавшие сучки — без ограничения; червоточины диаметром до 40 мм без ограничения; дефекты кромок листа глубиной до 5 мм;
Технология изготовления
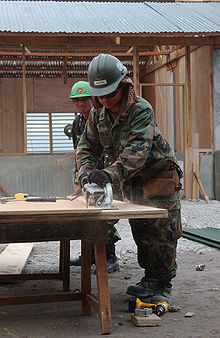
Бревно (чурак), очищенное от коры и термически обработанное, вращают вокруг своей оси. К вращающемуся бревну подводят лущильный нож, шириной на всё бревно, который как на токарном станке снимает «широкую стружку»; эта стружка называется шпон[2].
Шпон впоследствии раскраивают, сушат, сортируют, собирают в пакеты, то есть перекладывают шпон таким образом, чтобы направление волокон в смежных слоях было взаимно перпендикулярным, число слоёв нечётно и каждый чётный лист с двух сторон намазан клеем. Эти пакеты затем подвергаются давлению и нагреву в прессе, в результате получается фанера, которую затем обрезают в формат и упаковывают в пачки. Фанеру затем могут шлифовать и ламинировать плёнками — в результате получается шлифованная и ламинированная фанера.
Производство в России
Фанера в России выпускается следующих основных форматов 1525х1525, 1220х2440, 1500х3000,1525х3050 мм.
Производство фанеры в России (млн. м³): 2002 г. — 1,8; 2003 г. — 2,0; 2004 г. — 2,2; 2005 г. — 2,6;
Фанерное производство в России расположено по большей части в привязке к регионам, богатым лесными ресурсами. Основная доля выпуска приходится на предприятия Северо-Западного федерального округа — около 35 % в общем объёме производства. В 2005 году экспорт составил 1,5 млн м³, то есть около 60 % всей произведённой в стране фанеры.
См. также
Примечания
Литература
- Григорьев М. А. Материаловедение для столяров, плотников и паркетчиков: Учебное пособие для ПТУ. — М.: Высшая школа, 1989. — 223 с. — 100 000 экз. — ISBN 5-06-000345-0
- ГОСТ 3916.1-96 Фанера общего назначения с наружными слоями из шпона лиственных пород.
- ГОСТ 3916.2-96 Фанера общего назначения с наружными слоями из шпона хвойных пород.
- ГОСТ 13913-78 (ГОСТ на ДСП)
Ссылки
Всё о фанере
Структура и производство фанеры
Фанера (нем. Furnier, от франц. fournir – снабжать, накладывать) – листовой строительный материал, который обычно состоит из плотно склеенных по толщине нескольких тонких слоев древесины (шпона), причем направления волокон в соседних слоях шпона, как правило, взаимно перпендикулярны.
Для производства фанеры используют главным образом берёзовый шпон, в меньшей степени ольховый, буковый, сосновый и др. пород. Однако производятся и специальные виды фанеры, рассчитанные на повышенное сопротивление изгибу и кручению.
Industrial plywood – «специальная фанера». Специальной считается такая фанера, которая, приобрела особые свойства в результате каких либо технологических процессов и применяется в определённой области или нескольких областях. Отчасти специальной можно считать большеформатную фанеру (1220х2440;1525х3050), которую в Европе и Северной Америке широко используют в строительстве. Под это определение подходит и фанера ламинированная. Сюда относится и фанера бакелизированная («финская», «водостойкая»), а также другие марки фанеры узкой области применения: облицованная стеклотканью, листовым металлом, пробковой крошкой, армированная, биостойкая (антисептированная), композиционная, электротермическая, с рельефной поверхностью и т.д.
Фанера с симметричной относительно среднего слоя (серединки) структурой лучше всего сопротивляется короблению. Такая структура типа «сэндвич» характерна для промышленно выпускаемой фанеры, которая обычно склеивается из нечетного числа слоев и соответственно называется трехслойной, пятислойной, семислойной и т. д. Лист шпоновой фанеры набирается из слоев шпона одной древесной породы. Столярные фанерованные изделия с облицовкой и декоративной отделкой широко применяются при изготовлении мебели, дверей, стен и пр.
Основными качественными параметрами фанеры являются следующие:
· порода
· сорт
· формат листа
· толщины
· тип склейки
· обработка
Применение
Листы фанеры (размерами 1220 х 2440 мм) разного рода, различные по качеству, назначению и толщине, складируются и продаются как готовые строительные панели.
Такие панели широко используются при
· облицовке стен,
· настиле полов,
· возведении перегородок,
· крыш,
· сооружении различных желобов, опалубок и пр.
В разрезанном виде их применяют во многих отраслях производственной деятельности.
В высококачественных изделиях мебельной промышленности плоские поверхности делаются из фанеры, обычно облицованной дорогим декоративным шпоном. Такая фанера изготавливается, как правило, в специальном цехе мебельного предприятия, поскольку качество и внешний вид мебели существенно зависят от совместимости лицевого шпона и породы дерева основы или каркаса.
Фанера из древесины как твердых, так и мягких пород выпускается нескольких типов и сортов, которые различаются назначением, сроком службы, внешним видом и стоимостью. Среди этих типов выделяют, например, фанеру для внешних работ, для судостроения, для опалубок и влагостойкую фанеру. В самолетостроении применяется фанера толщиной от 1 мм и более; в домостроительстве используются готовые фанерные панели толщиной от 6 до 25 мм; для изготовления мебели применяется фанера толщиной от 3 мм (трехслойная низкосортная для задников зеркал и днищ ящиков) до 30 мм (пятислойная высокосортная для столешниц письменных столов). Для изделий различных отраслей промышленного производства требуется фанера толщиной от 3 мм (для фасонных лотков и желобов) до 38 мм (для печатных форм на линолеуме). Из дешевой тонкой фанеры повсеместно производят комплекты для тары, которая сшивается гвоздями.
Большая часть фанеры выпускается в виде плоских листов или панелей, но существуют механизированные методы производства и гнутых изделий из нее. Фанеру можно проклеивать, согнув ее по несложным контурам, например, заготовок для сидений в общественных местах или корпусов радиоаппаратуры и т.п. Обычно фанеру слегка изогнутой формы прессуют, зажимая ее между парой горячих пресс-форм. Выпускаются из фанеры также фасонные заготовки для кабин и кают, самолетных деталей и т.д.
Производство
Клеящие составы готовятся в механизированных смесителях и при производстве фанеры подаются в желобки пары клеевых вальцов (из металла или жесткой резины), которые прокатываются с обеих сторон каждого второго слоя шпона или пиломатериала. Затем пакеты промазанного клеем шпона зажимаются и склеиваются в гидравлических или пневматических, а иногда в винтовых (что наименее желательно) прессах.
Если клей наносится при комнатной температуре (от 21° до 27° С), то после этого листы проклеенной фанеры обычно складываются в штабели и выдерживаются в них 6 ч и более для затвердевания клея. Прессование фанеры с синтетическими термореактивными клеями наиболее эффективно при повышенной температуре — горячей склейкой, когда на получение готовых листов уходит всего несколько минут. Для этого гидравлические прессы делаются в виде многоярусного набора инструментальных плит с паровым подогревом от 120° до 150° С; между каждой парой таких плит закладывается прессуемый пакет — будущий лист фанеры. Существуют прессы с электрическим подогревом инструмента резисторами или высокочастотным электрическим полем.
Для производства гнутой фанеры плоские инструментальные плиты пресса снабжаются соответствующей парой металлических пресс-форм. При изготовлении фасонной фанеры сложного профиля одной из пресс-форм служит нагнетаемый объем в герметичной оболочке, который по всем направлениям давит с одной стороны на формуемую фанеру, помещенную на жесткую неподвижную пресс-форму. Для полимеризации смоляных клеев при этом применяют либо нагреваемые пресс-формы, либо в нагнетаемый объем накачивается горячий пар. Так как податливость древесины возрастает при ее подогреве, то для изготовления качественной сложно профилированной фанеры нельзя применять клеи, застывающие при комнатной температуре.
Выпускаются различные виды клееной фанеры:
· с облицовкой крафт-бумагой;
· с пропиткой и без нее;
· пригодные для внешней обшивки и фанерования.
Металлизированная фанера, т. е. клееная фанера со слоями металла, применяется там, где по условиям эксплуатации необходима прочная и плотная поверхность, например, в кузовах грузовиков, или там, где благодаря металлической прокладке повышается износоустойчивость и противопожарная безопасность материала.
Производится и фанера высокой плотности. Обычно их листы набираются из слоев бакелизированного шпона и прессуются методом горячей склейки. Удельный вес фанеры этого типа может достигать значения 1,3, причем древесина такой фанеры существенно уплотняется в процессе горячего прессования.
Сорта фанеры
В зависимости от внешнего вида наружных слоев фанеру подразделяют на пять сортов:
· Е (элита),
· I,
· II,
· III,
· IV.
Сорт фанеры обозначается сочетанием сортов шпона лицевого и оборотного слоев: сорт лицевого слоя / сорт оборотного слоя, например, E/I, I/I, I/II, II/II, II/III, II/IV, III/III, III/IV, IV/IV и т.д
Сорт I — булавочные сучки до 3 шт., здоровые сучки до 15 мм , выпадающие сучки до 6 мм допускаются, сомкнутые трещины допускаются не более 200 мм в количестве 2 шт. на 1 м ширины, здоровое изменение окраски допускается не более 5%, остальные дефекты древесины не допускаются.
Сорт II — допускаются булавочные сучки, здоровые сросшиеся до 25 мм, выпадающие до 6мм, сомкнутые трещины и разошедшиеся 2 мм в количестве 2 шт. длиной до 200 мм, здоровые изменения окраски, вставки из древесины.
Сорт I |
Сорт II |
Сорт III — допускается здоровые сучки, выпадающие сучки до 6мм, сомкнутые трещины, разошедшиеся трещины 2 мм в количестве 2 шт. длиной до 300 мм, здоровые изменения окраски, вставки из древесины, волнистость, рябь.
Сорт IV — допускаются выпадающие сучки до 40 мм без ограничения количества, разошедшиеся трещины шириной не более 10 мм без ограничения, вставки из древесины, волнистость, рябь.
Сорт III |
Сорт IV |
Толщина
Фанера является весьма распространенным материалом, который применяется, в том числе, и в мебельной промышленности. Широкое распространение фанера получила благодаря небольшому весу, легкости и простоте в обработке, устойчивости к резким сменам температуры окружающей среды. Кроме того, эстетические свойства фанеры достаточно высоки, она легко сочетается с любым другим материалом. По многим характеристикам, таким как теплопроводность, экологичность и прочность, фанера превосходит ДСП, ДВП и МДФ.
Изготавливать фанеру гораздо экономичней, чем изделия из металла или пластика, рассчитывается это в сравнении себестоимости производства фанеры с ее эксплуатационными показателями. Фанера производится несколькими различными способами. Типы фанеры разделяются по способам производства шпона на: пиленую, строганную и лущеную.
Первый тип фанеры — пиленая фанера, она производится только из ценных пород дерева. Пиловчинка — сырье для изготовления фанеры распиливается на полосы, толщиною до 5 миллиметров. Расходы сырья при производстве пиленой фанеры очень высоки, а производительность мала. По этой причине на данный момент пиленую фанеру во всем мире производить практически перестали.
Из названия типа фанеры понятно, что строганая фанера производится при помощи строгания заготовки. При этом шпон имеет толщину до 3,5 миллиметров. Сейчас подобный шпон производят по большей части из ценных пород лиственных деревьев. Строганая фанера имеет достаточно высокую степень производительности, но показатель этот все же ниже, чем у лущеной.
Лущение — самая производительная технология изготовления фанеры. Толщина шпона при лущении 1,2-1,9 мм. Сам процесс лущения напоминает работу токарного станка, отличие заключается в том, что для заготовки — кряжа (или как его по-другому называют — чурака), верхний слой снимается на всю ширину. Затем большое полотно режут под нужный формат и склеивают.
Изготавливают фанеру из одного или нескольких видов древесины, но фанеру считают изготовленной из той породы дерева, из которой сделан внешний ее слой. Если фанера изготовлена только из одной породы дерева, ее называют однородной. Если используется несколько пород, то комбинированной фанерой. Кроме того, фанера делится на несколько типов: клееную, бакелизированную (отличающуюся большой водостойкостью) и фанеру для декоративных целей. Из всех трех типов фанеры только клееная имеет виды: ФСФ — фанера с высоким показателем водостойкости, ФК и ФБА — средний показатель водостойкости и ФБ — ограниченная водостойкость.
Водостойкая фанера ФСФ применяется в строительстве для защиты наружной части домов (при этом саму фанеру дополнительно окрашивают) и внутреннего помещения (без окрашивания) от влаги. Кроме того, фанера используется в судо-, вагоно- и автостроении как строительный материал для конструкций, а также применяется в качестве многоразового опалубка во время заливки бетона в строительной промышленности.
Для того, чтобы повысить прочность и продлить срок эксплуатации фанеры, ее ламинируют. Делают это при помощи нанесения на фанеру импрегнированной фенольной смолы. Для строительных целей изготавливают ламинированную фанеру с сетчатой поверхностью. Такую фанеру используют при заливке бетона. Когда бетон застывает, на его поверхности отпечатывается сетчатый узор. Такую хитрость применяют потому, что на сетчатые углубления в бетоне гораздо легче наносится отделочный материал.
Статья предоставлена компанией All-fanera
http://www.vashdom.ru/ — Интернет портал «все для строительства и ремонта» Ваш ДОМ.RU
Фанера — это… Что такое Фанера?
Фанера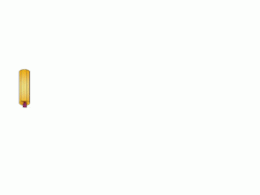
Фане́ра (древесно-слоистая плита) — многослойный строительный материал, изготавливаемый путём склеивания специально подготовленного шпона. Количество слоёв шпона обычно нечётное, от 3 и более. Для повышения прочности фанеры слои шпона накладываются так, чтобы волокна древесины были строго перпендикулярны предыдущему листу.
Применение
Самодельный вездеход «Каракат» с кузовом из фанерыКлассификация
Фанера называется продольной, если волокна в лицевых слоях направлены вдоль длинной стороны, в противном случае — поперечной
Фанера из древесины как твёрдых, так и мягких пород выпускается нескольких типов и сортов, которые различаются назначением, сроком службы, внешним видом и стоимостью.
По предназначению — строительная, промышленная, упаковочная, мебельная, и конструкционная.
По видам фанеру часто разделяют на два популярных вида — ФК (влагостойкая) и ФСФ (повышенной влагостойкости).
По типу обработки — ламинированная.
По внешнему виду (определяется количеством сучков на квадратный метр поверхности наружного слоя шпона): E (элита), I, II, III, IV.
По материалу, из которого изготовляется
- Хвойная фанера (изготавливается из шпона хвойных пород деревьев: лиственницы, сосны, пихты, ели). Иногда для изготовления фанеры используется шпон кедра — такая фанера используется в декоративных целях. Для хвойной фанеры обязательным является содержание хвойного шпона в наружных слоях — внутренние могут содержать шпон лиственных пород древесины.
- Берёзовая фанера (изготавливается из шпона берёзы) получила распространение практически во всех областях, но из-за относительно более высокой стоимости в строительстве используется не так широко, как хвойная.
По количеству слоев

- трёхслойная
- пятислойная
- многослойная
В основном листы фанеры имеют нечётное количество слоёв шпона: в этом случае шпон расположен симметрично относительно среднего слоя. Если слоёв шпона в фанере четыре, то центральные слои располагают и склеивают перпендикулярно наружным, что увеличивает общую прочность и стойкость к деформации.
По пропитке
Влагостойкая фанера — материал, обработанный специальным образом для увеличения сопротивления влаге. Максимально увеличить влагостойкие характеристики фанеры может помочь ламинирование.
- ФСФ (фанера, изготавливаемая с применением смоляного фенолформальдегидного клея). Эта фанера характеризуется относительно высокой износоустойчивостью, механической прочностью и высокой влагостойкостью. ФСФ — один из самых популярных видов фанеры, используется в строительстве, производстве, кровельных работах.
- ФК (фанера, получаемая при приклеивании шпонов карбамидным клеем). Обладая меньшими влагостойкими характеристиками, ФК используется преимущественно при внутренней отделке помещений, в мебельном производстве, при изготовлении деревянной тары, при работе с конструкциями внутри помещения.
- ФБ (фанера, пропитанная бакелитовым лаком, впоследствии склеивается). Этот вид обладает максимальной сопротивляемостью воздействию агрессивной среды и может использоваться в условиях тропического климата, при повышенной влажности и даже под водой.
- БС (фанера, пропитанная бакелитовым клеем, С — спирторастворимый). Эта фанера обладает фантастическими свойствами — сверхвысокой прочностью, стойкостью к агрессивным средам, гибкостью, упруготью, водонепроницаема, не гниет, не раскисает. Ее ещё называют называют авиационная фанера за то, что раньше использовалась только в авиа- и судостроении.
- БВ (фанера, пропитанная бакелитовым клеем, В — водоорастворимый). Эта фанера обладает теми же свойствами, что и предыдущая, за исключением влагостойкости, т.к. клей, применяемый при склеивании слоев — водорастворим.
По виду обработки поверхностей
- НШ — нешлифованная фанера
- Ш1 — материал, шлифованный с одной стороны
- Ш2 — материал шлифованный с двух сторон
Виды и сорта фанеры
В настоящий момент ГОСТы предусматривают наличие пяти сортов фанеры, которые отличаются главным образом наличием и количеством допустимых дефектов обработки[1].
- сорт Е (элита). Дефекты не допускаются, кроме незначительных изменений случайного характера в строении древесины;
- сорт I. Максимальная длина покоробленности или трещин для фанеры первого сорта не должна превышать 20 мм;
- сорт II. Допускаются трещины до 200 мм, вставки из древесины, просачивание клея площадью до 2 % от общей площади листа фанеры;
- сорт III. Допускаются червоточины до 10 шт. на квадратный метр при диаметре каждой не более 6 мм; общее количество перечисленных пороков не может быть больше 9;
- сорт IV. Фанера 4 сорта является крайне низкокачественной. Такая фанера может иметь следующие пороки: частично сросшиеся и выпавшие сучки — без ограничения; червоточины диаметром до 40 мм без ограничения; дефекты кромок листа глубиной до 5 мм;
Технология изготовления
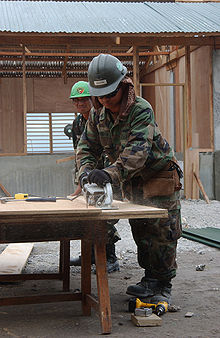
Бревно (чурак), очищенное от коры и термически обработанное, вращают вокруг своей оси. К вращающемуся бревну подводят лущильный нож, шириной на всё бревно, который как на токарном станке снимает «широкую стружку»; эта стружка называется шпон[2].
Шпон впоследствии раскраивают, сушат, сортируют, собирают в пакеты, то есть перекладывают шпон таким образом, чтобы направление волокон в смежных слоях было взаимно перпендикулярным, число слоёв нечётно и каждый чётный лист с двух сторон намазан клеем. Эти пакеты затем подвергаются давлению и нагреву в прессе, в результате получается фанера, которую затем обрезают в формат и упаковывают в пачки. Фанеру затем могут шлифовать и ламинировать плёнками — в результате получается шлифованная и ламинированная фанера.
Производство в России
Фанера в России выпускается следующих основных форматов 1525х1525, 1220х2440, 1500х3000,1525х3050 мм.
Производство фанеры в России (млн. м³): 2002 г. — 1,8; 2003 г. — 2,0; 2004 г. — 2,2; 2005 г. — 2,6;
Фанерное производство в России расположено по большей части в привязке к регионам, богатым лесными ресурсами. Основная доля выпуска приходится на предприятия Северо-Западного федерального округа — около 35 % в общем объёме производства. В 2005 году экспорт составил 1,5 млн м³, то есть около 60 % всей произведённой в стране фанеры.
См. также
Примечания
Литература
- Григорьев М. А. Материаловедение для столяров, плотников и паркетчиков: Учебное пособие для ПТУ. — М.: Высшая школа, 1989. — 223 с. — 100 000 экз. — ISBN 5-06-000345-0
- ГОСТ 3916.1-96 Фанера общего назначения с наружными слоями из шпона лиственных пород.
- ГОСТ 3916.2-96 Фанера общего назначения с наружными слоями из шпона хвойных пород.
- ГОСТ 13913-78 (ГОСТ на ДСП)