Как сделать стол из древесных обрезков
Перевел SaorY для mozgochiny.ru
Приветствую всех мозгоремесленников! Работали с пиломатериалом и остались обрезки, но выкинуть их жалко? Или паллеты бесполезно пылятся в мастерской? Тогда читайте это мозгоруководство о том, как своими руками сделать стол из отходов древесины.
Стол-самоделка описываемый в этом мастер-классе размером 245х76см и количество материалов, описанное ниже, подобрано для этих габаритов.
Шаг 1: Материалы
• поддоны или обрезки досок
• фанера 245х76 и толщиной 1.5см
• брус 5х5см для обрамления столешницы, около 680см
• столярный клей
• гвозди
• редуктор для дрели – приспособление позволяющее высверливать отверстия под углом
• саморезы 3.3см и декоративные заглушки для них
• саморезы 6.25см и 2см
• эпоксидная смола, около 6 литров — но это зависит от желаемой толщины слоя
• емкость для смешивания, палочки для размешивания
• малярный скотч
• металлопрофиль 50х50мм, около 9м
• металлическая полоса 50мм, около 1.2м
• металлическая труба диаметром 5см, около 5м
• краска-спрей для металла
Шаг 2: Подготовка материала
Начинаем с сортировки пиломатериала и отбора нужных мозгодосок, или с разбора паллет. Я собрал имеющиеся у меня поддоны и выбрал разные по текстуре и цвету.
Итак, разбираем паллеты, выбираем доски, вынимаем из них гвозди, скобы и т.п., то что может повредить инструмент при обработке досок.
Шаг 3: Нарезка по размеру
Выбранные доски распиливаем на равные по ширине досочки, длина не имеет значения. Мои досочки я нарезал шириной 4см. Длина не важна потому, что при склейке мы будем выкладывать досочки, заполняя пространство столешнице, друг за другом и лишнее просто обрежем.
Шаг 4: Фанерная основа
Фанерный лист обрезаем по нужным размерам стола и постепенно приклеиваем к нему подготовленные досочки. Стараемся чередовать цвет и длину досочек, чтобы узор поделки получался более интересным.
Я сначала намазывал клеем досочку, прикладывал ее в выбранном месте, прижимал струбциной и прибивал отделочными гвоздями, чтобы она удерживалась ими во время высыхания клея.
Шаг 5: Рамка по периметру
После того как досочки приклеены и обрезаны по периметру мозгоподелки, по этому самому периметру монтируем рамку из бруса, который больше по высоте чем приклеенные досочки. Эта рамка послужит бортикам при заливке эпоксидной смолы.
Для рамки берем брус 50х50см, нарезаем по размерам стола, концы обрезаем под углом 45 градусов и соединяем в рамку. Чтобы соединения бруса и фанерной основы получились качественнее, я использовал редуктор для дрели, который крепил к фанере и по нему высверливал отверстия под саморезы. А далее просто прикладывал брус рамки и через высверленные отверстия крепил его саморезами, сами отверстия потом заполнял шпатлевкой для дерева и зачищал, так они становились незаметными. На саморезы в углах рамки установил заглушки, а затем также зашпатлевал.
Шаг 6: Ножки для стола
Столешница собрана, поэтому переходим к опорам, то есть ножкам. Для создания ножек стола есть много вариантов, я решил сварить их из металлопрофиля.
Прежде всего, определяемся с габаритами мозгоопоры, я решил что моя будет 180х60х30см. Далее нарезаем профиль по размерам и приступаем к сварке.
Сначала свариваем профиль буквой «U», затем к концам привариваем полосы, делаем два таких элемента. Затем эти элементы профилем объединяем в опору, и усиливаем ее пролеты металлическими трубами. Зачищаем сварные швы и красим всю опору самоделки краской по металлу.
Шаг 7: Крепление столешницы
Перед монтажом столешницы на опору в самой опоре нужно просверлить отверстия под крепеж. Для этого по периметру опоры высверливаем в ней отверстия под саморезы, а отверстия в полосах опоры еще и зенкуем, чтобы утопить шляпки саморезов.
Далее переворачиваем столешницу и кладем ее на пол, тыльной стороной вверх. Размечаем на ней место крепления опоры так, чтобы она была по мозгоцентру. Устанавливаем опору, так же вверх ногами, и саморезами крепим ее к столешнице.
Шаг 8: Заливка смолы
Приводим стол в рабочее состояние, то есть переворачиваем и ставим на опору, а затем переходим к ответственному шагу – заливке эпоксидной смолы.
На полу под столом расстилаем клеенку, так как можно запачкать сам пол. Чтобы избежать утечек смолы, малярным скотчем заклеиваем швы, трещинки, отверстия и т.д. По инструкции готовим эпоксидную смолу и, соблюдая ТБ, заливаем столешницу. Желательно чтобы помещение, где проводится заливка, было теплым, проветриваемым и хорошо освещенным, а стол стоял на ровной поверхности. Это важные моменты для получения совершенно гладкой поверхности стола.
При заливке заполняйте все пустоты и уголки столешницы, и не заливайте большими слоями, больше 6мм, давайте каждому слою примерно 6 часов на отвердевание. Тщательно перемешивайте эпоксидку, заливайте медленно, чтобы избежать пузырьков воздуха, если они все-таки образовались, то горелкой «выгоняйте» их.
После полного затвердевания базового слоя смолы, удаляем малярный скотч и заливаем чистовой слой, который превратит столешницу в бесшовный монолит. После затвердевания чистового слоя зачищаем и полируем подтеки, которые могли образоваться по бокам и на нижней поверхности поделки.
Шаг 9: Наслаждаемся творением!
Самоделка из вторсырья готова, радуемся плодам своего безотходного мозготворчества!
(A-z Source)
ПОДЕЛИТЕСЬ С ДРУЗЬЯМИ!
About SaorY
Как без сварки сделать ленточный шлифовальный станок на базе болгарки
Ленточный шлифовальный станок может использоваться для заточки ножей, топоров, стамесок, выведения спусков клинков, обтачивания заготовок, снятия ржавчины и решения десятков других задач. Это незаменимое оборудование, но для маленькой мастерской даже оно может оказаться слишком габаритным. Имея недостаток свободного пространства на рабочем месте, можно смастерить самодельный ленточный гриндер на базе УШМ 125 мм. Такой станок получается очень компактным и недорогим в производстве, а применяемую в качестве его привода болгарку при надобности можно снимать и использовать в обычном режиме.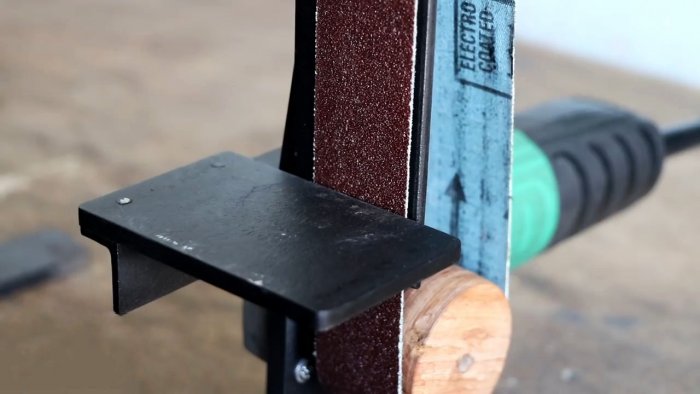
Необходимые материалы
Выбор материалов и их количество зависит от того, какую шлифовальную ленту планируется использовать. Лучше, делать гриндер под ленту стандартных размеров, представленных в продаже, чтобы потом не обрезать бумагу и не склеивать ее самостоятельно. Для гриндера на базе болгарки подойдет лента шириной 40, 45, 50 мм.
Определившись с лентой, можно заготовить прочие материалы:
- удлиненная гайка М12;
- брус или доска толщиной соответствующей ширине ленты;
- двухкомпонентный эпоксидный клей;
- стальная плита или широкая полоса толщиной от 5 мм;
- стальной уголок 50х50 мм или крупнее;
- болты М6;
- болты М10;
- гайки М10;
- подшипники 3-4 шт.;
- пружина растяжения.
Изготовление ленточного шлифовального станка
Для начала нужно сделать ведущий каток для вращения ленты. Его можно высверлить коронкой диаметром 40-50 мм из бруска или доски.
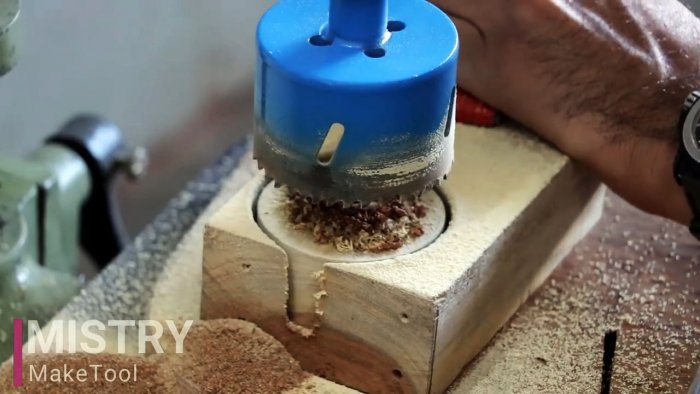
При этом ширина ролика должна быть равной или больше ширины ленты. С одной стороны его центральное отверстие нужно рассверлить и впрессовать в него на эпоксидный клей удлиненную гайку М14.
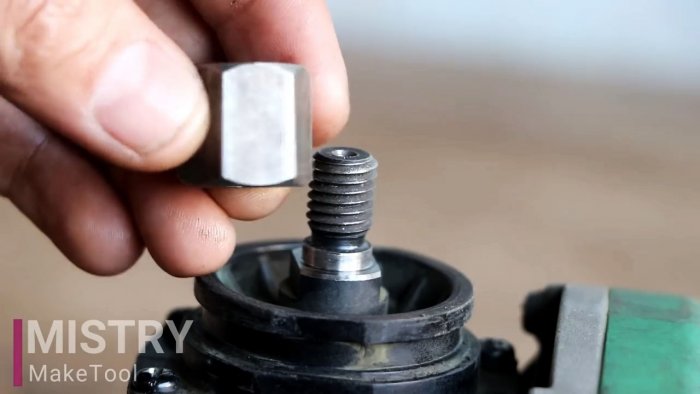
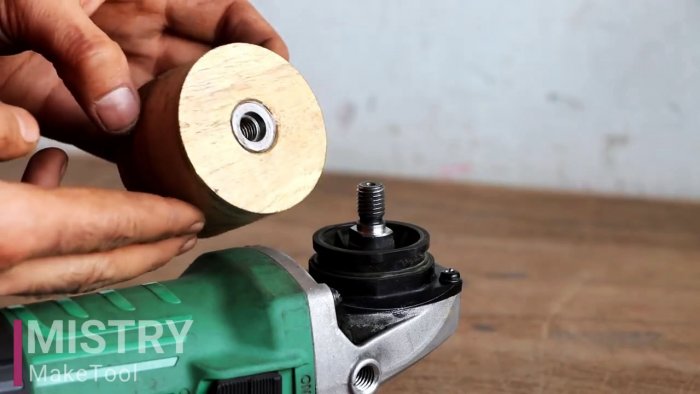
После застывания клея ролик устанавливается на болгарку. Далее нужно включить УШМ и прошлифовать его, прижав к наждачной бумаге. Нужно придать ему бочкообразную форму, слегка присадив края и оставив центральный диаметр. В таком случае лента потом ну будет слетать.
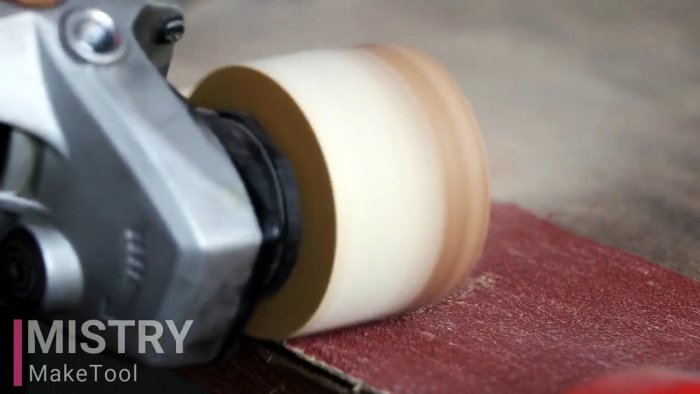
Из полосы или стальной плиты вырезается станина гриндера. Ее размеры будут зависеть от длины выбранного стандарта шлифовальной ленты.
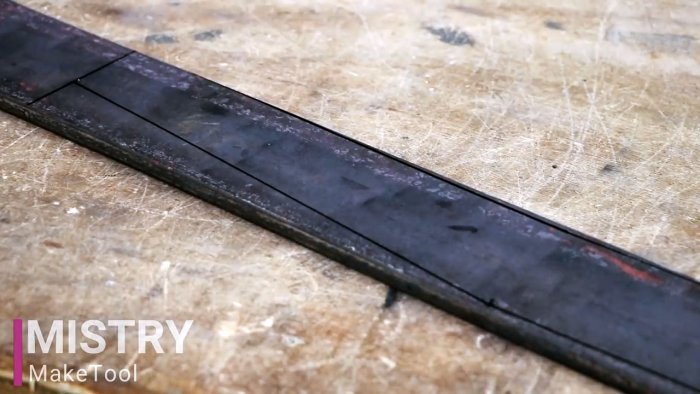
В станине делается отверстие диаметром 40-45 мм. В него будет вставляться редуктор болгарки и выводится вал.
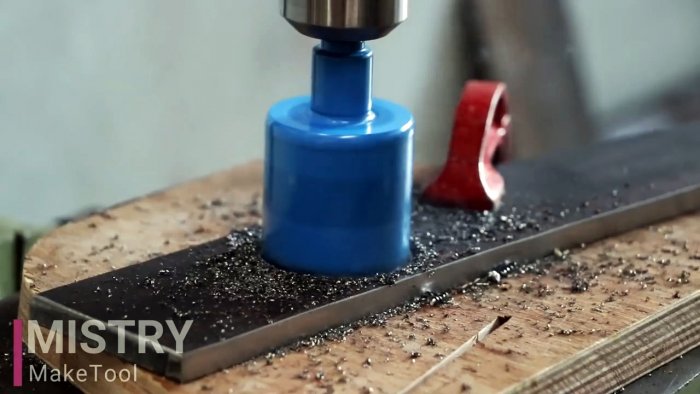
Для разметки креплений нужно снять на время редуктор, приложить его по месту и отметить отверстия под винты.
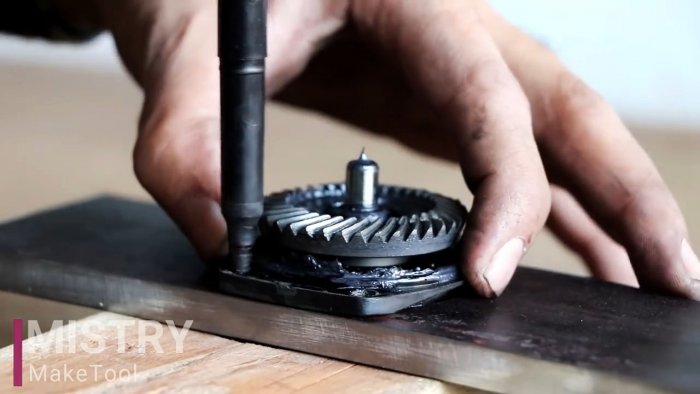
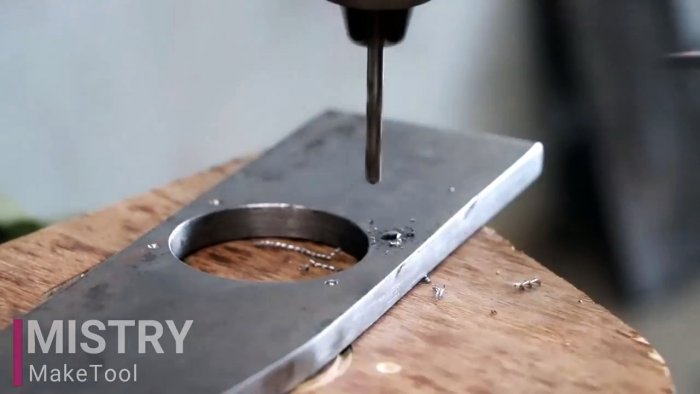
В станине делаются 4 крепежные отверстия и 2 проточки сбоку, чтобы при состыковке она не мешала винтам, прижимающим редуктор к корпусу УШМ.
Из двух обрезков уголка делается подставка станка.
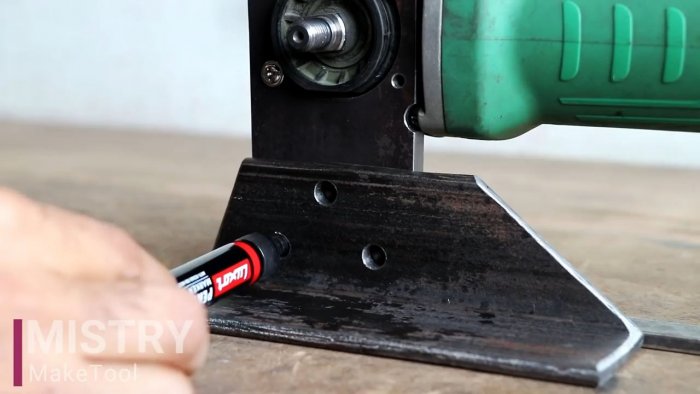
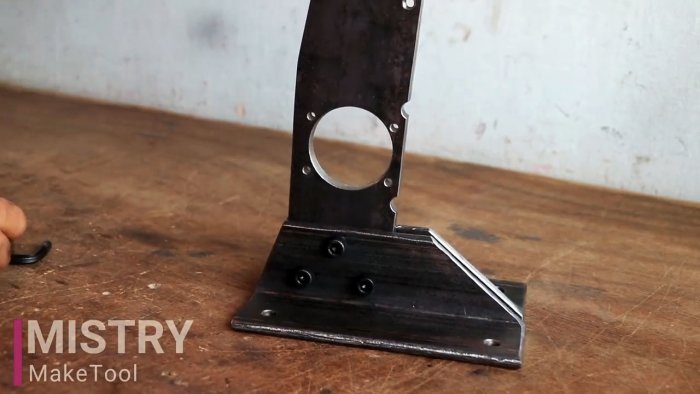
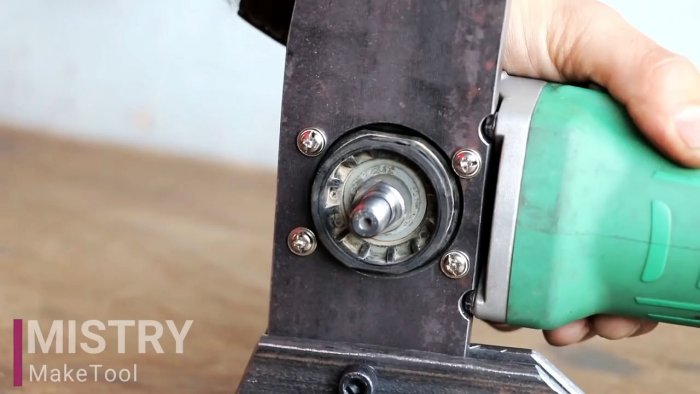
Между ними болтами зажимается станина в вертикальном положении. Для этого делаются отверстия под 3 болта М6, в которых нарезается резьба. Также понадобятся отверстия на дне подставки, чтобы прикручивать станок к столу. Закрепив станину можно примерить и болгарку, но штатные винты на ее редукторе нужно заменить удлиненными.
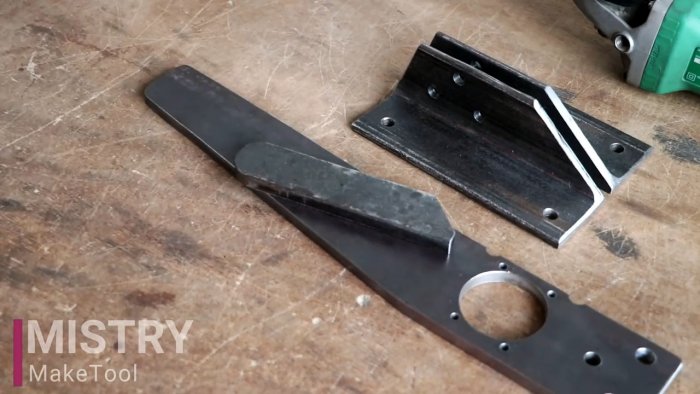
Далее вырезается плечо для натяжения ленты. По центру оно крепится к станине болтом М10 с гайкой.
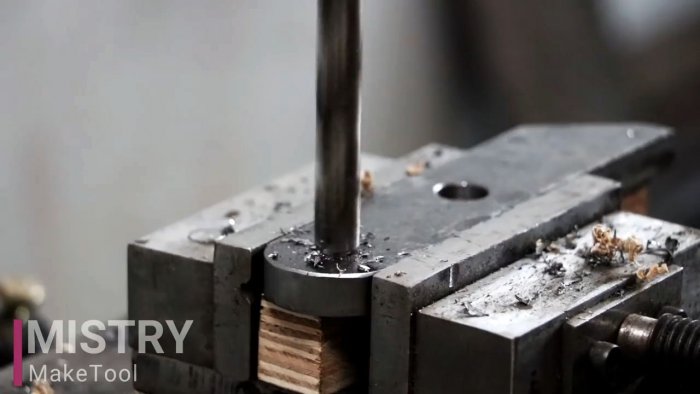
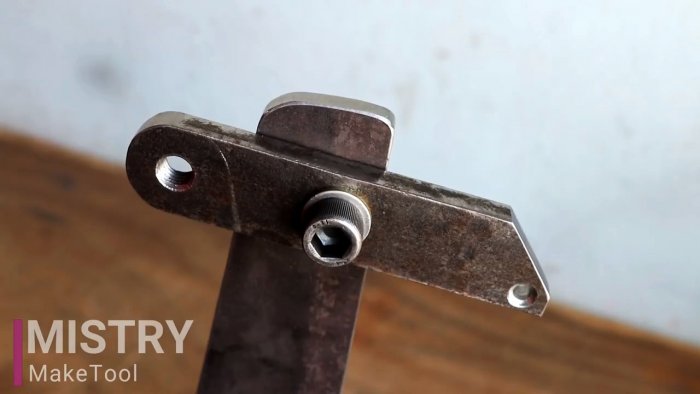
На конце плеча ставится второй болт М10, прижимающий 3-4 подшипника. Нужно чтобы ширина группы подшипников соответствовала ширине ленты. Они будут выполнять функцию ведомого катка натяжения.
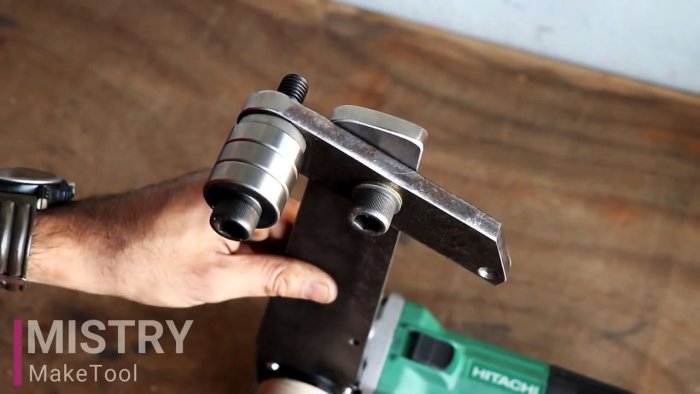
Для подтяжки полученного ролика, на второй конец плеча ставится пружина, зацепленная внизу станины.
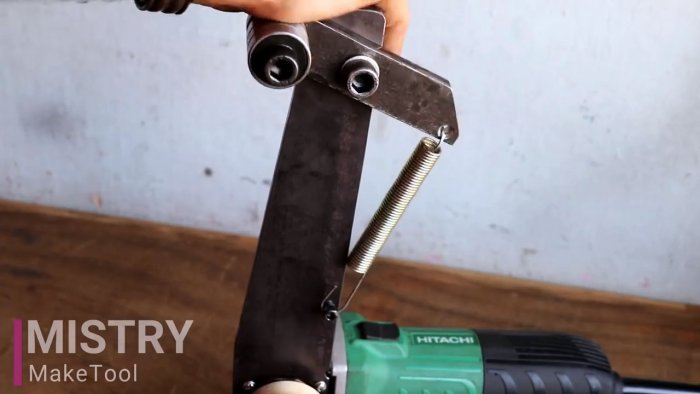
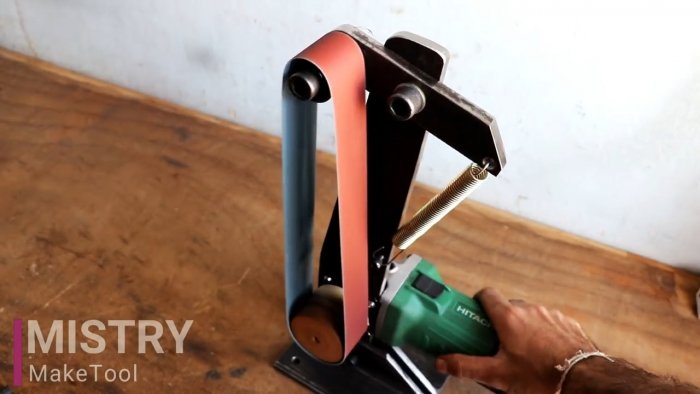
Из уголка вырезается регулируемая плита упора, как на фото. У нее должна быть проточка для возможности изменения положение при зажатии.
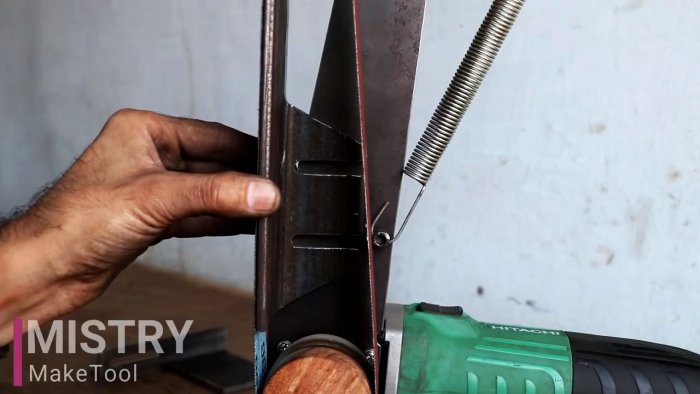
Также из стальной плиты и маленького уголка делается рабочая площадка. На ее уголке также нужно сделать проточку для возможности регулировки положения.
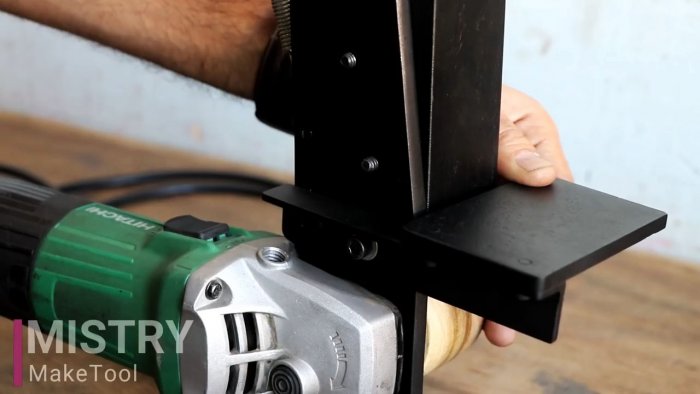
Упор и рабочая площадка прикручиваются к станине болтами М6. После натяжения шлифовальной ленты станок может использоваться по назначению. Он может выполнять абсолютно те же задачи, что и фабричный гриндер. При ненадобности станок можно разобрать и компактно сложить. Применяемая с ним болгарка не подвергается конструктивным изменениям, поэтому по прежнему может использоваться по основному назначению.
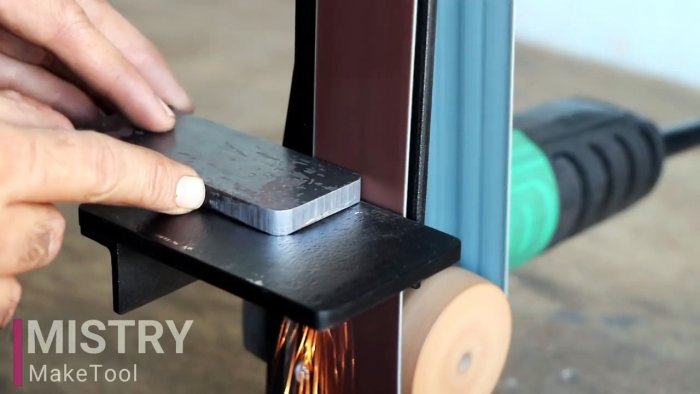
Смотрите видео
как сделать деревянную столешницу для кухни
Производственные технологии постоянно совершенствуются — создаются новые недорогие полимеры и прочные композиты, однако без натуральных материалов обойтись пока нельзя. Дерево находится в числе особо востребованных и значимых в строительстве материалов. И если вам хочется, чтобы кухню украшал деревянный стол, пришло время заняться разработкой проекта.
Для эффектного и прочного изделия не обязательно использовать элитные и дорогие сорта древесины. С помощью воображения и тщательной проработки задуманного, можно сделать столешницу из досок, обрезков, спилов и бруса. Современные дизайнеры научились превращать недостатки в достоинства: этим замечательным опыт определенно стоит воспользоваться.
Кратко о склейке столешниц из дерева
Изготовление мебели в домашних условиях — непростое и ответственное дело. И все же многие решаются на монтаж деревянной столешницы для кухни своими руками.
Столы ручной работы имеют немало достоинств:
- Экономия бюджета. Материалы обойдутся гораздо дешевле, нежели готовое изделие. К тому же можно использовать домашние запасы от прошлых проектов.
- Индивидуальный дизайн. Готовое изделие трудно подобрать идеально под интерьер и размеры кухни. Самостоятельный монтаж дает для этого все возможности.
- Уникальность. Сделанная собственноручно, мебель всегда единственная и неповторимая.
- Уверенность. Качество изделия от начала до конца под вашим личным контролем.
- Удовольствие. То, что сделано своими руками всегда украшает дом и радует семью особенным уютом.
Несколько недостатков самостоятельного монтажа:
- Время и силы. Сразу необходимо учесть немалые трудозатраты и найти свободное время для работы.
- Инструменты. Без набора специализированных современных инструментов строительные работы существенно усложнятся. Приобрести инструменты — необходимость.
- Техника безопасности. Некоторые виды работ вредны для здоровья — рекомендуется тщательно соблюдать правила техники безопасности.
Как правильно, легко и просто сделать столешницу из дерева своими руками
Массив дерева — это материал, который полностью состоит из натурального дерева. Главное отличие массива от материалов, произведенных из стружки и других отходов деревообрабатывающей промышленности в том, что он всегда производится из цельных кусков древесины.
Необработанный массив выпускается в виде брусков, досок, полотен. Цельный массив считается элитным материалом — он выполняется из идеально чистых кусков древесины, без сучков и полостей. Клееный массив состоит из нескольких слоев древесины, которые фиксируются между собой специальным клеящим веществом. Каждый из этих слоев называется ламелью.
Столешницы из массива разнообразны по конфигурации, расцветке и внешним параметрам. В этой статье рассмотрим самые интересные варианты, которые можно сделать своими руками из деревянных массивов.
Столешница из досок
Если в кладовой или гараже лежат ненужные доски, которые остались от предыдущих работ, не спешите выбрасывать столь ценный материал. Столешница из досок, сделанная в домашних условиях, не потребует от вас профессионального столярного умения, при этом вещь выглядит необычно и обойдется совсем недорого.
Вам потребуются материалы:
- Доски. Они могут быть разного размера и цвета. Ширина 4 см.
- Фанера. Размер 140х260 см, толщина 20 мм.
- 4 бруса по 70 см (ножки стола).
- 3 бруса по 90 см (долевые детали каркаса).
- 4 бруса по 45 см (поперечные детали каркаса).
- Саморезы.
- Гвозди.
- Мебельный клей.
- Морилка и мебельный лак.
Потребуются инструменты:
- Ручная циркулярная пила.
- Торцовочная пила.
- Электродрель.
- Шуруповерт.
- Шлифовальная машинка.
- Рулетка, угольник, карандаш.
Порядок работ:
- Изучить чертеж, на котором показаны соединения деревянных деталей.
Сделать стол из ненужных досок своими руками
- Собрать из брусьев 0,35х0,35 см каркас-основание, как показано на схеме (обозначение А). Использовать косое потайное крепление на саморезы, предварительно смазав соединения столярным клеем. Угол крепления должен быть ровно 90°. Контролировать угольником.
- Укрепить основание стола поперечными перекладинами, затем долевой перекладиной (обозначение В). Это необходимо для гарантированной устойчивости конструкции. Места соединений крепить потайными саморезами, посаженными на столярный клей.
- На лист фанеры нанести разметку для крепления основания. Замеры выполнять тщательно, чтобы основание пришлось точно по середине фанерного листа. Уложить фанеру на раму основания. Закрепить лист с помощью 12 — 16 саморезов, сверху вниз.
- По периметру столешницы установить планки-бортики (обозначение D). Бортики крепить с помощью клея и гвоздей. Бортики должны выступать над столешницей на 4 см — толщину доски.
- Подготовить доски. Вытащить старые гвозди, очистить. Длинна не так важна, доски будут подгоняться. Ширина точно 4 см.
- Доски разложить на фанерной основе, подбирать разные по цвету и длине. Такая мозаика сделает столешницу эффектнее.
- Подобранные доски отпилить и подогнать по длине. Склеить доски для столешницы, сажая каждую на столярный клей и закрепляя отделочными гвоздями.
- После окончания набора и высыхания клея, заполнить все неровности, щели и шляпки гвоздей шпаклевкой по дереву. Шпаклевку подобрать в тон дереву.
- Дать полностью просохнуть столешнице. Отшлифовать машинкой с разными насадками, меняя от крупных к мелким.
- Последним этапом покрыть дерево морилкой и лаком. Лак нанести как минимум в три слоя. Сделать окончательную полировку войлоком.
Наборная столешница из брусков
Деревянный брус — это отличный строительный материал, который нужен для возведения стен, колонн, перегородок и опорных балок. Для изготовления столов брус применяется в тех случаях, когда это оправдано интерьером, например для беседки или на даче. Такое изделия массивно, прочно и долговечно.
Смотрится стол из бруса весьма брутально, но купить готовое изделия в подобном стиле сложно. Поэтому есть смысл взяться за собственноручное изготовление. Рассмотрим вариант наборной столешницы из брусков для кухни. Потребуются материалы:
- Брус 100х100 для двух вертикальных опор.
- Брус 100х50 для горизонтальных и диагональных элементов ножек, ребер жесткости.
- Лак и малярная кисть.
Нужные инструменты:
- Пила.
- Электродрель.
- Набор наждачной бумаги или шлифмашина.
- Шуруповерт или отвертка.
- Саморезы.
- Струбцины.
- Уровень.
- Рулетка.
- Линейка и карандаш.
Порядок работ:
- Собрать столешницу по схеме. Во всех брусках на одном уровне просверлить сквозные отверстия, делая в крайних зенковку под шайбы с гайками. Смежные грани промазать клеем и стянуть столешницу шпильками.
- Изготовить широкие опоры для стола. На выровненные боковые поверхности соседних брусков нанести клей, после чего бруски соединить. На время высыхания клея зафиксировать струбцинами.
- В готовых опорах вырезать сквозное квадратное отверстие для установки перемычки.
- Отрезать от бруса перемычку такого размера, чтобы она была длиннее расстояния между опорами стола, но короче длины столешницы. Оба конца перемычки уменьшить до размеров отверстий в опорах, чтобы они свободно в них входили и выступали за внешнюю плоскость на 8-10 см.
- В уменьшенных частях перемычки сделать отверстия для деревянных клиньев, которые послужат замком. Внутренние поверхности отверстия тщательно выровнять и зашлифовать.
- Вырезать два клина, подогнав их под размер пазов в перемычке.
- Собрать каркас стола. Точно подогнать все детали.
- Уложить столешницу дном вверх на ровную плоскость. Сделать разметку карандашом под крепления ножек. Установить перевернутый каркас и выровнять его относительно осевых линий.
- По осевым линиям закрепить небольшие бруски или рейки. Получившиеся прямоугольники будут служить пазами, фиксирующими основания в заданном положении под весом столешницы.
- Отшлифовать столешницу машинкой, меняя насадки. Начинать с крупной зернистости, закончить мелкой.
- Покрыть стол морилкой. Последний этап — тройная последовательная лакировка.
Столешница из дуба
Изделия из дуба всегда славились своей особой прочностью, устойчивостью к перепадам температур и долговечностью. Дубовый стол надежен, красив и не меняет своих качеств под воздействием окружающей среды. Самой большой популярностью у современных дизайнеров пользуются столешницы из дубового слэба и эпоксидной смолы.
Справка. Слэб —это цельный продольный спил дерева. Одну сторону такого спила выравнивают и обрабатывают под край столешницы, а внутренние стороны остаются неровными. Это придает изделию эффектности и максимально сохраняет природную красоту уникального материала.
Сделать своими руками столешницу в стиле лофт, которая также получила название стол-река, вполне возможно.
Потребуются материалы:
- Лист фанеры для заливочного стола.
- Дубовый слэб желаемого размера.
- Эпоксидная смола и отвердитель.
Нужные инструменты:
- Тара для смешивания смолы, 2 шт.
- Электродрель.
- Шлифмашина со съемными насадками.
- Пила.
- Фреза.
- Строительный уровень.
- Шпатель.
Важно! Эпоксидная смола должна быть специализирована для разведения в больших объемах! Нельзя нарушать инструкции производителя, смола «закипит» или не полностью отвердеет.
Порядок работ:
- Продумать вентиляцию помещения, в неотвержденном виде смола вредна для здоровья. Подготовить защитные средства. Костюм, перчатки, защитные очки.
- Собрать опалубку. Так называется форма для заливки столешницы. Форма должна точно соответствовать размерам задуманного изделия. Опалубку собрать из листа фанеры.
- Все швы опалубки заполнить силиконовым герметиком. Внутреннюю поверхность тщательно натереть воском или вазелином. Иначе смола прикипит к форме.
- Слэб подготовить к заливке. Тщательно очистить от коры, выровнять наружный край. Отшлифовывать машинкой до гладкости. Покрыть морилкой и лаком. Дождаться высыхания лака.
- Выровнять опалубку для столешницы по уровню. Очень важный этап, если допустить неровности, изделие получится ассиметричным.
- Расположить слэб на опалубке.
- Подготовить смесь смолы с отвердителем. Делать все точно по инструкции производителя. Пропорции отмерять на весах. Осторожно влить отвердитель в смолу, размешать строительным миксером на невысоких оборотах. Несколько раз перелить смесь из одной емкости в другую для более тщательного перемешивания. Добавить колер.
- Залить первый слой в опалубку, осторожными зигзагообразными движениями. Состав должен растечься равномерно по всех площади. Тщательно контролировать толщину слоя, указанного производителем.
- Проследить, чтобы в слое смолы не осталось пузырьков. Образовавшиеся осторожно удалить иголкой или прогреть поверхность феном в течении 2-3 минут.
- Закрыть опалубку листом фанеры. Крышка предохранит изделие от пылинок. Выдерживать отверждение слоя, согласно инструкции.
- Залить следующий слой. Заливку делать в несколько этапов, пока не заполнятся все полости в столешнице. Последний слой должен тонко покрыть весь слэб.
- Отвержденное изделие (полный процесс займет не меньше 7 дней) вынуть из опалубки. Оформить финальной шлифовкой все поверхности столешницы при помощи шлифмашинки.
- Покрыть прозрачным защитным лаком и установить столешницу на основу.
- Полюбоваться своим творением и осознать, что жизнь прожита не зря.
Столешница из ламелей
Деревянные лемели — это монолитный клееный массив из деревянных фрагментов. По этой технологии деревообрабатывающая промышленность производит фанеру, клееный брус, клееный брусок, мебельный щит, столярный щит, сращённый погонаж.
Материалы натуральны, доступны и часто используются в изготовлении кухонных гарнитуров. Как пример рассмотрим круглый стол из фанеры —надежный, недорогой и простой в изготовлении.
Потребуются материалы:
- Брус 3050х120х50 – для ножек стола.
- Круг берёзовой фанеры диаметр 1500 мм, толщина 35 мм для столешницы.
- Диск фанеры с внешним диаметром 1280 мм, внутренним диаметром 1040 мм, толщиной 20 мм для связующего диска.
- Фанера 1060х120х20 мм – 2 шт. для планок.
Необходимые инструменты:
- Дрель-шуруповёрт.
- Лобзик электрический.
- Биты для шуруповёрта.
- Свёрла по дереву.
- Дисковая шлифмашинка.
Порядок работ:
- Распилить строительный брус на четыре части. Ножки, длинной 760 мм каждая, отшлифовать и покрыть тройным слоем лака.
- Диск, в верхней части схемы, выпилить из фанеры толщиной 20 мм. Это связующая часть для ножек. Из этого же листа выпилить планки.
- Прикрутить планки к ножкам по схеме.
- Столешницу выпилить из берёзовой фанеры толщиной 35 мм.
- Ножки закрепить плоскостью вовнутрь. Размер планок, которые придают конструкции жесткость 120х1060 мм.
- Все детали покрыть морилкой. После высыхания сделать лаковое покрытие в три слоя.
Заключение
Вариантов для индивидуального творчества придумано немало. Каждый настоящий мастер ищет что-то новое. Художники по дереву украшают столешницы резьбой, выжиганием узоров.
Наборные мозаики из шпона и кусочков дерева поражают тонкостью работы. Декупажная техника и роспись столешниц снова в моде, художники создают в этом стиле абсолютно изделия или реставрируют старую мебель. А технология заливки столешниц эпоксидной смолой предоставляет грандиозные возможности для работы с деревом и создания уникальных и долговечных изделий.
Брусок 50х50: почему этот размер так востребован?
В строительстве не обойтись без брусков – дешевых пиломатериалов, которые служат для сооружения различных вспомогательных конструкций: обрешеток, опалубок, лаг. На брусок 50х50 цена такова, что его применение для черновых работ выгодно с финансовой точки зрения. Одновременно он достаточно прочен, чтобы выдержать значительную нагрузку и безупречно выполнять свои функции.
Обрешетка, опалубка, лаги
Бруски 50х50 применяется для создания обрешеток, пригодных для монтажа имитации бруса, разных видов вагонки, включая широкий блок-хаус. В этом случае бруски размещаются таким образом, чтобы расстояние между ними составляло от 50 см до 1 метра.
Шатровая крыша – эффектна и надежна. Основанием для монтажа кровельного материала служит обрешетка из сухих строганных брусков. Сочетая в себе высокую прочность и малый вес, они незаменимы при возведении кровельных конструкций.
Этот размер идеально подходит для строительства опалубки под фундамент. Бруски 50х50 помогают соединять доски опалубки, с их помощью устанавливаются щиты для залива бетонного раствора.
Устройство полов предусматривает установку лагов для дальнейшего крепления на них досок пола, террасной доски или других видов покрытия. В роли лагов традиционно выступают бруски50х50.
Лестницы, балконы, перегородки
Балясины – это важнейшие элементы лестничных перил, ограждений веранд и балконов. Они выполняют поддерживающую функцию и просто обязаны быть максимально надежными. Для изготовления балясин также используются бруски указанного размера. После дополнительной обработки они принимают вид фигурных столбиков и становятся не только функциональным элементом конструкции, но и её изысканным украшением.
Создание внутренних перегородок – одна из самых интересных сфер применения брусков 50х50. Именно из них формируют каркас для дальнейшей его обшивки гипсокартонном, пластиковыми панелями, МДФ, вагонкой и прочим.
Производители оптимизируют технологический процесс, используют автоматические линии для обработки древесины. В результате такого подхода снижается себестоимость пиломатериалов, а следовательно и порядок отпускных цен.
К примеру, здесь строганный сухой брусок предлагают приобрести по цене ниже среднерыночной. При этом качество обработки и точность размеров полностью отвечают установленным требованиям. Учитывая все вышесказанное, стабильный спрос на такой простой, но такой нужный материал воспринимается, как абсолютно закономерное явление.
Чертежи & Видео & Фото Монтажа

Самый простой и лаконичный стеллаж из дерева
Как часто бывает, что вещей в доме становится все больше, а мест для их хранения не находится. Тогда мы начинаем придумывать самые немыслимые варианты – складываем вещи в коробки, пакеты и прячем подальше от глаз. А на самом деле всего-то нужно обзавестись стеллажом.
Тот же принцип действует и в теплицах – рассада и саженцы нуждаются в надлежащем уходе и быстром доступе, который можно обеспечить, сделав стеллаж из брусков самостоятельно.
Содержание статьи
Что в теплице живет

Примерная схема стеллажа для теплицы
Теплица нужна для того, чтобы даже в холодное время года можно было выращивать овощи и фрукты, зелень и даже цветы. Температура в теплице может быть такой как в субтропиках, а значит, при надлежащем уходе можно вырастить даже ананасы!
Но в основном в теплицах выращивают более простые овощи и фрукты, которые встречаются на рынках и полках магазинов в любое время года. На стеллажах же удобно выращивать зелень, цветы, некоторые виды саженцев и рассады.
Рассмотрим подробнее несколько видов тепличной деятельности :
Выращивая зелень в теплице, вам следует знать, что она не привередлива к условиям, достаточно будет поддерживать температуру до 19 СО и дополнительно подсвечивать до 14 часов в сутки. Период времени, за который зелень полностью созревает, достаточно мал, а это означает, что при поддержании правильных условий за год можно собрать около 10 урожаев.
Еще одним плюсом является то, что зелень выгодно выращивать на стеллажах, ведь ее можно сажать плотно друг к другу и размещать в несколько ярусов, что позволит экономить пространство и выращивать продукт в больших количествах.
Так же стоит заранее подумать о том, кто будет реализовывать вашу продукцию – займетесь вы этим самостоятельно или продадите перекупщикам. На разных стеллажах можно разместить сразу несколько видов растений, к примеру – один стеллаж полностью отведен под фиалки, а другой под цветочную рассаду.
- Саженцы и рассаду очень удобно размещать на стеллажах, но нужно знать, что у таких стеллажей должны быть высокие борта для пикировки.
Строим стеллаж в теплицу

Конструкция деревянного стеллажа с перемещающимися полками
Для того, чтобы изготовить стеллаж из бруса своими руками не нужен большой багаж знаний и огромный опыт работы с мебелью. Будет достаточно иметь под рукой все необходимые материалы и инструменты, и следовать алгоритму действий.
Такой стеллаж позволяет экономить финансы, ведь цена материалов, которые нужны для самостоятельного изготовления, значительно ниже, чем уже готовая фабричная мебель.
Нам понадобятся:
- Деревянный брус квадратного сечения не менее чем 30 на 30 мм.
- Деревянные рейки для дополнительно укрепления конструкции.
- Доски ДСП, фанера, натуральное дерево, в общем все, из чего можно сделать полки.
- Отвертка, шурупы и дюбеля.
- Рулетка, карандаш.
- Ватерпас (уровень).
- Ножовка по дереву или электрический лобзик для большего удобства.
Важно! Подбирая материал, не забывайте, что стеллаж будет находиться в теплице, под воздействием света, воды и температуры, а значит, он должен быть крепок и долговечен. Как вариант – на деревянные детали можно нанести защитное покрытие.
В этой статье вы имеете возможность ознакомиться с несколькими фото того, как должна выглядеть подготовка к работе.

Деревянный брус квадратного сечения
Создавая чертеж нужно вооружиться рулеткой и простым карандашом, чтобы выбрать подходящие для вашей теплицы размеры будущего стеллажа. Ширина полок может варьироваться в различных пределах, но так как на этих полках будут стоять растения, то достаточно будет 60-70 см.
Длину следует подбирать в зависимости от того, сколько рассады вы планируете расположить на одной полке. Если ее вес будет слишком велик, то длинные полки будут прогибаться, чтобы этого не случилось, придерживайтесь рекомендуемой длины 80-90 см.
Рассчитать высоту предполагаемой конструкции можно измерив рабочие поверхности в доме, это делается для того, чтобы ряд, на котором вы планируете пересаживать, шевелить или удобрять растения соответствовал вашему росту.

Деревянный стеллаж с дополнительным искусственным освещением
Обычно нижнюю полку делают на такой высоте, чтобы под нее можно было поставить необходимые в теплице вещи, например удобрения, перчатки и прочий садовый инвентарь. Если на стеллаже планируется ставить цветы, то лучше сделать низкие борта, это значительно упростит проведение системы полива к растениям.
После того как все пожелания учтены, а параметры сопоставлены делают чертеж. Обычно схематического рисунка с указанием всех размеров вполне достаточно.
Переходим к основному процессу

Усиленная конструкции деревянного стеллажа
Дальнейшая инструкция не представляет особой сложности. Начнем с монтажа – несущую опору делаем из деревянного бруса, это даст гарантию, что основание стеллажа будет прочным.
Для того, чтобы зафиксировать брусья с досками основания лучше всего подойдут саморезы размером 3 см. В процессе монтажа нужно помнить, что несущие опоры должны размещаться только вертикально.
Когда окончательно готово основание стеллажа переходят к установке коробки. Подготовленный для этой цели материал крепят к брусьям внизу, вверху и по бокам. В итоге получается коробка, но без задней стенки.

Двухуровневый, ступенчатый стеллаж из дерева
После того как коробка готова переходят к установке полок. Для точности и удобства следует сделать небольшие пометки на боковых сторонах коробки, они будут указывать те места, где расположатся полки. Полки закрепляются так же при помощи саморезов, но можно выбрать, к примеру, металлические уголки.
Сверху к ним прикрепляют поперечные бруски, на которые будет приходиться опора полок. Самая большая нагрузка обычно приходится на полки, расположенные в средине, поэтому возможно ее следует дополнительно укрепить.
Совет! Стоит обратить внимание, что саморезы, которые используются для соединения полки и бруса, необходимо брать на 5-6 мм больше, чем толщина полки.
Так как стеллаж будет установлен в теплице, то дополнительная отделка ему не требуется, разве что для более длительной эксплуатации следует покрыть конструкцию защитными средствами. В целом, на прикрепленном видео в этой статье доступно показан процесс создания стеллажа из бруса, который делается в несколько этапов.
Как правильно разместить стеллажи в теплице

Примерная схема размещения стеллажей вы теплице стандартного размера
Между стеллажами обязательно должны быть проходы, он может быть один или несколько. Ширина прохода зависит от того, будете ли вы пользоваться дополнительным инвентарем, например тачкой.
Для обычной ходьбы достаточно 50 см, а для тачки – около 60 см. Так же расставляя стеллажи, стоит учитывать систему полива, которой нужен доступ к растениям, и размещение дополнительного освещения.
В теплицах обустроенных стеллажами необходимо отвести отдельную зону для растений, которым требуется изоляция. К примеру, только что купленное новое растение не ставят рядом с остальными, так как нет гарантий, что почва не загрязнена яйцами паразитов или растение не болеет.
Обычно для таких нужд выделяют одну полку на стеллаже, куда должно помещаться не больше 3-4 растений. Ее со всех сторон дополнительно ограждают стеклом, и следят, чтобы освещение в карантинной зоне не было слишком сильным. Если отрицательных изменений в новых растениях не происходит, то через несколько недель их можно пересаживать на основные стеллажи.
И в заключении

Сборка стеллажа
Как видно, процесс изготовления стеллажей из дерева довольно прост, и выполнить его под силу даже человеку, никогда ранее не сталкивавшемуся с подобными работами.
Главное – это помнить несколько нехитрых правил:
- Выбирайте только тщательно просушенный лес, с минимальным количеством влаги.
- Сучки на деревянных брусках, самые слабые места, поэтому, чем их меньше, тем прочнее и надёжнее будет конструкция.
- Используйте дополнительные пропитки для дерева. Они уберегут дерево от появления плесени и жучков.
- Каждая планка должна быть закреплена минимум на двух саморезах. Только так можно получить прочую конструкцию, которая не будет шататься.
Вот в принципе и всё, можно покупать все необходимые материалы, готовить инструмент и вперёд, к высокому званию домашнего мастера.
Как изогнуть дерево в домашних условия или в мастерской
Как изогнуть древесину
Если вы решили отделать помещение деревом или заняться созданием красивой мебели в классическом стиле – то вам необходимо будет изготавливать криволинейные детали. К счастью, древесина является уникальной субстанцией, ведь она позволяет опытному мастеру немного поиграться с формой. Это не так сложно, как кажется, но и не так легко, как хотелось бы.
Ранее на сайте уже была публикация по изгибанию фанеры. В этой статье мы разберёмся в принципах гнутья массивной доски и бруса, узнаем, как это делают на производстве. А также приведём полезные советы от профессионалов, которые будут полезны домашнему умельцу.
Почему гнутьё лучше выпиливания
Криволинейную деревянную деталь можно получить двумя методами: изогнув ровную заготовку, либо вырезав необходимую пространственную форму. Так называемый способ «выпиливания» привлекает пользователей своей простотой. Для такого изготовления деталей и конструкций не нужно использовать сложные приспособления, не приходится тратить много времени и сил. Однако, чтобы выпилить криволинейное деревянное изделие, приходится применять заведомо слишком крупную заготовку, причём очень много ценного материала будет безвозвратно теряться в качестве отходов.
Но главной проблемой являются рабочие характеристики полученных деталей. При раскрое криволинейной детали из обычного обрезного пиломатериала, волокна древесины не меняют своего направления.
Как результат, в зону радиусов попадают поперечные срезы, которые не только ухудшают внешний вид, но и заметно усложняют последующую доводку изделия, например, его фрезерование или чистовое шлифование. Кроме того, на самых уязвимых для механического воздействия скруглённых участках волокна идут поперёк сечения, что делает деталь склонной к разлому в этом месте.
Тогда как при гнутье обычно наблюдается противоположная картина, когда древесина становится только прочнее. На кромки изогнутого бруса или доски не выходят «торцевые» срезы волокон, поэтому впоследствии можно без ограничений обрабатывать такие заготовки, с использованием всех стандартных операций.
Изгибание волокон дерева
Что происходит в древесине при изгибании
Технология гнутья основана на способности древесины, сохраняя целостность, в некоторых пределах менять свою форму по мере приложения силы, а затем сохранять её после снятия механического воздействия. Однако все мы знаем, что без подготовительных мероприятий пиломатериал является упругим – то есть он возвращается в исходное состояние. А если приложенные силы слишком велики, то брус или доска попросту ломается.
Слои деревянной заготовки при изгибании работают неодинаково. Снаружи радиуса материал растягивается, внутри – сжимается, а в середине массива волокна практически не испытывают существенных нагрузок и мало сопротивляются действующим на заготовку силам (этот внутренний слой называют «нейтральным»). При критичной деформации волокна на внешнем радиусе разрываются, а на внутреннем радиусе обычно образуются «складки», которые являются довольно распространённым дефектом при изгибании мягкой древесины. Сжиматься волокна пластичных лиственных или хвойных пород могут на 20 и более процентов, тогда как предел растягивания составляет около одного-полутора процентов.
То есть для определения возможности для изгибания (без разрушения) более важным показателем будет предел относительного удлинения растянутого слоя. Он напрямую зависит от толщины детали и определяет радиус, который нужно получить. Чем толще заготовка и чем меньше радиус – тем больше будет относительное удлинение вдоль волокон. Имея данные о физических свойствах популярных пород древесины, можно для каждой из них сформулировать максимально возможное соотношение толщины и радиуса деталей. В цифрах это будет выглядеть так:
Изгиб с использованием стальной шины
Порода | Возможный (внутренний) радиус изгиба по отношению к толщине детали после пропаривания и применения шины. |
---|---|
Сосна | 1:11 |
Ель | 1:10 |
Берёза | 1:5,7 |
Дуб | 1:4 |
Бук | 1:2,5 |
Изгиб без использования шины
Тип подготовки пиломатериала | Возможный (внутренний) радиус изгиба по отношению к толщине детали. |
---|---|
Только нагрев | 1:80 – 1:100 |
Только увлажнение | 1:50 – 1:60 |
Нагрев и увлажнение | 1:20 – 1:30 |
Эти данные говорят о том, что хвойный пиломатериал, по сравнению, с плотными лиственными породами, хуже приспособлен к свободному изгибанию. Для работы с пиломатериалами на агрессивных радиусах нужно обязательно использовать комбинированные методы предварительной подготовки деталей и механической защиты.
Шина как действенный способ избежать разрушения древесины при изгибании
Так как основной проблемой является разрыв волокон со стороны наружного радиуса, именно эту поверхность заготовки нужно как-то стабилизировать. Одним из самых распространённых методов является использование накладной шины. Шина представляет собой стальную полосу толщиной от полмиллиметра до двух миллиметров, которая охватывает брус или доску по наружному радиусу и изгибается на шаблоне вместе с древесиной. Упругая полоса поглощает часть энергии при растягивании и одновременно с этим перераспределяет разрушающую нагрузку по длине заготовки. Благодаря такому подходу в купе с увлажнением и нагревом, допустимый радиус изгиба уменьшается в разы.
Параллельно с использованием стальной шины в гибочных приспособлениях и станках добиваются механического уплотнения древесины. Делается это при помощи прессующего ролика, который давит на заготовку по наружному радиусу изгиба. Кроме того, форма-шаблон в таком приспособлении часто наделена 3-миллиметровыми зубьями (с шагом около 0,5 см), ориентированными навстречу ходу заготовки.
Задача зубчатой поверхности шаблона — не дать заготовке проскользнуть, предотвратить взаимный сдвиг волокон в деревянном массиве, а также создать мелкую вдавленную гофру в вогнутом радиусе детали (волокна тут запрессовываются вовнутрь массива, следовательно, решаются проблемы со складками).
Схема изгиба с шиной
Прессование с шиной позволяет с минимальным процентом брака изгибать бруски и доски из хвойной и мягкой лиственной древесины. Обратите внимание, что детали из относительно твёрдых пород при гнутье с прессованием становятся примерно на десять-двенадцать процентов тоньше, а сосновые и еловые заготовки – на 20-30% тоньше. Но к положительным моментам этого метода нужно отнести значительное увеличение прочностных характеристик готового изделия, а также существенное снижение требований к наличию пороков и дефектов в заготовках из древесины.
Как улучшают пластичность древесины
В нормальном состоянии пиломатериалы обладают упругостью, существенной пространственной жёсткостью и стойкостью к сжатию. Эти ценные свойства древесина получает от лигнина – природного «сетчатого» полимера, который придаёт растениям стабильную форму и прочность. Располагается лигнин в межклеточном пространстве и в клеточных стенках, соединяя целлюлозные волокна. В древесине хвойных пород его содержится порядка 23-38 процентов, в лиственных породах – до 25 процентов.
По сути, лигнин является своего рода клеем. Мы можем его размягчить и превратить в «коллоидный раствор», если нагреть пиломатериал путём пропаривания, проваривания, обработки током высокой частоты (для мелких деталей применима также бытовая микроволновка). После расплавления лигнина заготовку изгибают и фиксируют – остывая, расплавленный лигнин отвердевает и не даёт древесине вернуться в исходную форму.
Практика показывает, что оптимальной температурой для гнутья цельной древесины (брусок, рейка, доска) будет 100 градусов Цельсия. Эту температуру нужно получить не на поверхности, а внутри заготовки. Поэтому во многом от того, насколько массивной является деталь, будет зависеть время температурного воздействия. Чем толще деталь – тем дольше её придётся нагревать. К примеру, если использовать пропаривание для подготовки к изгибанию рейки толщиной 25 мм (с влажностью около 28-32%), то в среднем на это уходит около 60 минут. Примечательно, что время выдержки под паром аналогичных по габаритам деталей для любых пород примерно одинаковое.
Кстати, считается, что перегревать деталь тоже нельзя, так как лигнин после отвердевания может потерять упругость и стать слишком хрупким.
Метод проваривания используется не часто, так как заготовка сильно и неравномерно увлажняется, а такие водонасыщенные волокна и клетки при гнутье могут рваться, как минимум, с образованием ворса. Детали после варки приходится потом слишком долго сушить. Но этот способ хорошо показывает себя, если нужно обработать для гнутья только часть заготовки.
Пропаривание позволяет прогревать заготовку равномерно, причём влажность её на выходе стремится приблизиться к оптимальной. Наиболее подходящая влажность для достижения максимальной пластичности пиломатериалов считается диапазон в 26-35 процентов (момент насыщения волокон древесины).
Чтобы пропарить древесину для гнутья в домашних условиях, используют самодельные цилиндрические камеры из металлических/полимерных труб или прямоугольные короба из дерева. В качестве источника пара выступают нагревающиеся баки, электрические чайники и прочие подобные приспособления, которые могут обеспечить температуру порядка 105 градусов и небольшое давление. Далее всегда следует этап просушивания детали (+ выдержки зафиксированной формы) примерно до пятнадцати процентов и её финишной обработки.
Парогенератор из чайника
Парогенератор из полимерной трубы
Фиксация и сушка заготовки
Химические методы пластификации древесины
Известно также, что можно сделать пиломатериал более податливым, используя пропитку различными составами. Есть готовые пропитки, которые делают клетки древесины пластичнее, например, «Super-Soft 2». Некоторые практикующие мастера замачивают дерево в так называемых кондиционерах для текстиля, получая схожий результат.
Но могут использоваться также довольно примитивные «рецепты» с содержанием нашатырного и этилового спирта, глицерина, щелочей, перекиси водорода, растворённых квасцов… Многие из них действуют предельно просто — повышают способность заготовки поглощать воду и помогают удерживать влагу в волокнах.
Тонкие изделия типа шпона обрабатываются распылением, но подготовительная пропитка химией нормальных пиломатериалов, как правило, выполняется методом полного погружения. Чтобы рабочие вещества попали вовнутрь бруска или рейки, нужно время, обычно требуется от 3-5 часов до нескольких суток (правда, нагревание помогает сократить ожидание).
Во многом именно из-за длительности процессов химическую пластификацию применяют не часто, хотя есть и другие проблемы: цена химии, изменение окрасов, необходимость обеспечить защиту от вредных испарений, увеличенная склонность таких изогнутых деталей к распрямлению…
Химические пластификаторы для дерева
Советы по изгибанию пиломатериалов с использованием гидротермической подготовки
- Очень тщательно подбирайте по качеству заготовки для гнутья. Лучше не использовать материал с трещинами, сучками (даже живыми и сросшимися), наклоном волокон. Если вариантов для этого нет, то ориентируйте деталь в гнутарном приспособлении (станок или шаблон) так, чтобы дефекты попадали в зону вогнутого радиуса, а не в зону растяжения на наружном радиусе. Отдайте предпочтение методу изгибания с шиной.
- При подборе заготовки обязательно нужно предусмотреть изменение размера детали после формования. Например, на 30 процентов уменьшаться может толщина хвойного бруска, если выполняется гнутьё с прессованием.
- Даже если вы планируете обширную финишную обработку – не оставляйте слишком много материала. Чем тоньше заготовка, тем легче она гнётся без разрушения.
- Если объём работ небольшой, то лучше не выпиливать заготовки, а накалывать их из чурок. Так удаётся избежать среза волокон и, как следствие – брака при изгибании.
- Для гнутья желательно использовать пиломатериал с естественной влажностью. Если применять сухие заготовки, то предпочтение стоит отдать тем, что не обрабатывались в сушильной камере, а вялились под навесом — атмосферным способом.
- После пропаривания работайте с размягчённой древесиной очень быстро, так как лигнин начинает отвердевать практически сразу, особенно в самых уязвимых наружных слоях массива древесины. Обычно нужно ориентироваться на запас времени от получаса до 40 минут, поэтому нет смысла делать крупные камеры, если весь материал из которых вы попросту не успеете установить в шаблоны.
- Располагайте материал в пропарочной камере так, чтобы именно поверхности, обращённые к внешнему радиусу, беспрепятственно попадали под струи пара.
- Чтобы сэкономить время, многие столяры отказываются от применения шаблонов со струбцинами. Вместо этого они используют на шаблонах металлические скобы и клинья, либо столбики-ограничители.
- Имейте ввиду, что изогнутый брусок или рейка всё-равно стремиться к распрямлению. И это распрямление всегда происходит на несколько процентов. Поэтому когда требуется высокая точность в изготовлении детали, необходимо провести испытания и на основе полученных результатов подкорректировать форму шаблона (уменьшить радиус).
- После остывания детали в форме дайте ей ещё постоять. Некоторые опытные мебельщики предпочитают сделать выдержку в 5-7 дней. Шину, как правило, на всё это время оставляют закреплённой на детали.
Изгибание деревянной заготовки по шаблону
Использование приспособлений для изгиба дерева
Сарай своими руками: каркасный, деревянный, пошагово,фото, видео
Какой бы ни был площади дом без сарая на участке не обойтись. Не все можно и нужно заносить в дом, даже если и место есть, а уже если нету, так тем более — хозпостройки необходимы. Это, кстати, может быть первым опытом в самостоятельном строительстве: построить сарай своими руками можно и без навыков. Главное, чтобы руки росли из нужного места.

При желании сарай можно сделать похожим на маленький домик
Из каких материалов строят
Содержание статьи
Если сарай расположен недалеко от дома и вас заботит его внешний вид, есть смысл использовать тот же материал материал что и при строительстве дома. Если не хочется тратить большую сумму на хоз-постройку, можно подобрать отделку так, что и издали и не отличить. В большинстве случаев это не очень сложно: технологий много и многие материалы очень точно воспроизводят внешний вид дорогостоящих отделочных материалов. Яркий пример тому — сайдинг. Он есть под бревно, брус, кирпич, камень с разной фактурой. Так что для постройки сарая не обязательно использовать дорогие материалы. Практичнее использовать недорогую технологию строительства, а потом обшить материалом с фактурой, похожей на отделку основного строения.
Как быстро и дешево построить сарай
Самый быстрый и одновременно недорогой вариант постройки сарая — по каркасной технологии. Каркас может быть деревянным или металлическим, его обшивают снаружи отделкой, ставят крышу и все, сарай готов. Если сарай планируется деревянный, его собирают из бруса и досок. Сарай металлический можно удобнее делать из профилированной трубы: квадратное сечение и варить и стыковать проще в разы. Есть еще специальный металлокаркас. Он собирается на саморезы, а вся конструкция заказывается и изготавливается на заводе. Такие дома считаются наиболее дешевыми, вряд ли сараи будут дорогими. Сборка и металлического и деревянного сарая занимает несколько дней: проверено не единожды.

На половину построенный сарай: пол и две длинные стены стоят, осталось установить короткие и сделать стропильную систему
Каркасная постройка получается легкая, потому фундамент под сарай нужен облегченный. В большинстве случаев достаточно столбиков, бетонных блоков, иногда устанавливают винтовые сваи или делают буронабивные. На более сложных грунтах и для тех, кто любит надежность, можно построить монолитный или сборный (из фундаментных блоков) ленточный фундамент мелкого заложения.
На армированном ленточном фундаменте можно ставить даже сарай из строительных блоков или кирпича. В этом случае даже на пучнистых грунтах постройка будет стоять нормально. Она если и будет двигаться, то вместе с фундаментом, так что риск возникновения трещин минимален.
Каркасный сарай можно построить и без фундамента. Тогда стойки (обработать от гниения) нужно будет заглубить на 60-80 см, забетонировать, и потом к ним крепить нижнюю обвязку, но которую будут опираться лаги пола. Но таким способом большое строение не построишь. Максимум — небольшую каморку и дровник рядом.
Еще один вариант. Он пригоден для грунтов, с которых хорошо уходит вода, а подпочвенные воды расположены глубоко. Тогда размечают участок, который больше планируемого сарая на 50 см в каждую сторону, снимают дерн и делают песчано-гравийную подсыпку. На утрамбованный щебень укладывают брус обвязки и крепят к ним лаги пола (обработанные антисеплитком для прямого контакта древесины с грунтом). Вот и все. Никаких сложностей.

Сарай без фундамента
Это далеко не лучший вариант: даже при низком уровне грунтовых вод и тщательной обработке древесины сарай простоит недолго. Если вас это устраивает, можно делать и так.
Какой построить туалет на даче читайте тут (схемы и чертежи).
Фундамент для каркасного сарая
Все типы свайного или столбчатого фундамента предполагают расположение единичных опор по периметру: обязательно под углами строения и в местах примыкания перемычек (перегородок), если такие предусмотрены. Шаг установки опор зависит от размеров сарая и от того, какие лаги планируете использовать. Чем больше пролет, тем большего сечения требуются лаги.
Например, для ширины сарая 2 метра, можно поставить только два ряда столбиков и лаги при этом будут 150*50 мм (в крайнем случае 150*40 мм). Если ширина сарая 3 метра, то или ставить промежуточные опоры (столбики, сваи), или брать доску 150*70 мм. Посчитайте, что в вашем регионе дешевле выйдет, и выбирайте.

Вырытые котлованы под столбы
При ширине доски 100 мм пол под ногами ощутимо прогибается. Так что приходится шаг установки лаг делать около 30 см. Тогда прогиба нет совсем, или он незначительный (от веса зависит).
Быстрее всего сделать фундамент на готовых блоках: их можно купить или сделать самостоятельно. Под них копаются котлованы чуть больше по размерам чем блоки. На дно насыпают песок, трамбуют, затем гравий, его тоже трамбуют. Толщина подсыпки в утрамбованном виде — 20-30 см. На нее устанавливаются блоки, а уже на блоки монтируется нижняя обвязка.

После того как выложены блоки, на них крепится нижняя обвязка
Если речь про мелкозаглубленный ленточный фундамент, то траншею копают вглубь на 40-60 см относительно уровня грунта, ширина ленты порядка 25 см, а сама траншея должна быть шире как минимум на полметра или более: в нее устанавливается опалубка. Дно ровняют, трамбуют. На дно насыпают щебень и снова трамбуют.

Для опалубки использованы доски 150*50 мм, чтобы была возможность использовать их в дальнейшем, их оббили пергамином. После демонтажа опалубки (как бетон схватился) их разобрали и поставили как лаги пола
Из прутка 12-14 мм вяжут каркас. Четыре ребристых продольных прутка связывают при помощи рамок, изготовленных из гладкого прутка 6-8 мм. Размеры рамок должны быть такими, чтобы вся арматура находилась от краев ленты на расстоянии не менее 5 см. Например, если фундамент будет 40*25 см, то прутки связывают в конструкцию с прямоугольным сечением 30*15 см.

В опалубку устанавливают связанный каркас, который затем заливается бетоном марки не ниже М-200
Подробнее о каркасе для ленточного фундамента читайте тут.
Деревянный каркасный сарай своими руками: пошагово с фото
Был построен каркасный сарай размером 6*3 метра. Крыша односкатная, крыта ондулином. Высота передней стены 3 метра, задней — 2,4 м. Эксплуатация показала, что при таком перепаде высот снега много не скапливается (Лен. область).
В качестве фундамента под сарай использованы стандартные блоки ФБС 600*300*200. Они уложены на песчано-гравийную подсыпку толщиной 25 см. Поверх блоков уложена отсечная гидроизоляция — слой рубероида, на битумную мастику. Сверху еще приклеен на ту же мастику слой «гидротекса». Такой пирог сделан потому что уровень грунтовых вод высокий, необходимо было гарантированно защитить постройку от сырости.

Начало строительства сарая. На фундамент уложена гидроизоляция, на нее — обвязка,, а к обвязке прикреплен брус
На гидроизоляцию укладывался брус сечением 150*150 мм (все пиломатериалы обработаны). Соединялся в полдерева, бился гвоздями — 100*4 мм. Для тех, кто незнаком с плотницким делом, можно соединить брусья встык, на места соединения прибить изнутри усиленные уголки, снаружи — монтажную пластину.
В данном варианте каркас к блокам ничем не крепился. В регионах с повышенными ветровыми нагрузками это неоправданно. Крепить можно при помощи шпилек: под них насквозь, через брус, в блок, сверлится отверстие такого же диаметра, (12-14 мм). В него загоняется шпилька, болт потом подтягивается ключом. Чтобы шляпка спряталась, под нее можно рассверлить отверстие.
Следующий шаг — крепление лаг пола. Установлены на ребро доски 150*60 мм. Крепятся к обвязке специальными скобами соответствующего размера. Крепились на гвозди 100*4 мм.

Лаги пола крепятся к обвязке такими скобами
Лаги выравнивались по верхнему краю обвязочного бруса. Все должно быть ровно, иначе пол будет стелить тяжело. Возможно, придется ровнять рубанком или переделывать.
Каркас собирался по технологии «платформа»: сначала настелили пол, а на него монтировали стены. Каркас стены или ее часть собираются на полу. В некоторых случаях сразу обшиваются с наружной стороны, если выбран для обшивки плитный материал. И уже в таком виде (с обшивкой или без) поднимаются, выставляются вертикально и закрепляются.
Есть вторая технология «баллун». По ней каркас монтируется постепенно: на обвязку или даже сразу на блоки монтируются угловые стойки каркаса. Они выставляются в уровень во всех плоскостях. Между ними натягивают канат, по которому затем выставляют остальные стойки. Их также прибивают по одной, скрепляя между собой укосами и временными поперечинами.
Вам может быть интересна статья «Делаем дровники и поленницы своими руками»
В данном случае была выбрана технология «платформа» и на лаги настелили ОСП 18 мм толщины. Вообще, пол можно сделать из досок, фанеры (влагостойкой), ОСП и т.д. Доска потребуется 20, фанера — 13-15 мм, но нужна влагостойкая (ОСБ влагостойкая по умолчанию).

Настелен пол в сарае
Далее началась сборка стен. Полностью сбивается каркас: нижняя обвязка, стойки, верхняя обвязка. В таком виде устанавливается ровно по краю бруса обвязки, выставляется, укрепляется страховочными распорками, упорами, укосами. Прибивается насквозь через настил пола к брусу обвязки. Гвозди брали 200*4 мм.

Собраны стены. Верхняя обвязка будет сразу и опорой для стропил
Для сборки каркаса использованы доски 100*50 мм, расстояние между стойками 600 мм, стропила установлены с таким же шагом. Стропильная система собиралась из 150*40 мм.
Оконные и дверные проемы усилены — прибиты по две доски, которые между собой сбиты гвоздями в шахматном порядке через 20 см. Нагрузка тут больше, потому требуется усиление. В одном из торцов предусмотрены ворота — для загрузки/выгрузки крупногабаритных вещей. Потому в этой стене (на фото видно) только угловые стойки и усиленные — для крепления створок.

Вид на торец, в котором будут широкие двустворчатые двери
Так как крыша односкатная, стропильная система простая: укладываются на ребро доски, которые выбраны под стропила. Их длина больше, так как необходим свес кровли. Он обычно 30-50 см с каждой стороны. В данном варианте при ширине сарая 3 метра, длина стропильных ног (с учетом уклона) составила 3840 мм.
Прибивались наискось гвоздями — по два с каждой стороны. Можно усилить установкой уголков: так выдержит даже значительные ветровые и снеговые нагрузки.

Обрешетка под ондулин
Далее — на крыше смонтирована обрешетка (100*25 мм). Шаг ее установки — по рекомендациям производителя «ондулина» — 40 см. И настелен кровельный материал (гвозди покупались вместе с покрытием).
Стены снаружи зашили ОСП 9,5 мм толщиной.

Процесс наружной обшивки сарая
Установили двери, сделаны небольшие ступеньки.

Двери установлены старые, приведенные в порядок
Последними штрихами устанавливалась ветровая доска. Затем сарай был обшит вагонкой и покрашен краской в тон остальным постройкам на участке. Сарай своими руками на готовом фундаменте построен за два выходных дня. Обшивка вагонкой и покраска были значительно позже -почти через месяц.

Окончательный вариант сарая…красиво
Непривлекательный фундамент зашит нарезанным по размерам асбестовым листом. Красивый получился сарай.
Более подробно о принципах каркасного строительства из древесины читайте тут.
Сарай с двускатной крышей из металлочерепицы
Этот сарай строился в одиночку. Постройка тоже каркасная: самый дешевый способ. В этом случае способ сборки — «баллун» — постепенное выставление стоек. Все начинается также: сначала сделали столбики под фундамент. Только на этот раз кирпичные.

Фундамент под сарай из кирпичных столбиков
Как видите, в угловые стойки вмонтированы шпильки. В обвязочном брусе сверлятся отверстия и он одевается на шпильки. Их можно делать не только в углах, но и на промежуточных столбах тоже: крепче будет держаться.
Этот сарай имеет небольшое крыльцо-веранду, потому на требуемом расстоянии установлен поперечный брус. А него будет опираться стенка. Под него предварительно сделаны и столбики.

Лаги крепились тоже на пластины
Лаги могут крепится еще и врубкой. Тогда в обвязочном брусе вырезается выемка по форме лаги. По глубине она не должна превышать 30% от толщины бруса, потому лага подрезается так, чтобы она встала на одном уровне с обвязкой. Это способ более трудоемкий.
Далее собирался каркас: угловые стойки 100*100 мм, промежуточный — 50*100 мм, верхняя обвязка и стропильная система собиралась из той же доски. Треугольники вверху усилены накладными металлическими пластинами. Пластины меньшего размера крепились и в местах стыковки верхнего бруса обвязки и стоек. Они соединялись встык без врубки, прибивались сверху и наискосок гвоздями. Пластины уменьшили вероятность складывания при боковых нагрузках.

Каркас собран
Далее собиралась стропильная система — доска 150*50 мм, на нее — обрешетка под металлочерепицу. Была выбрана, так как таким же материалом крыта дача.

Собранная стропильная система с обрешеткой
Каркас обшивался листами ОСП — самый удобный размер для постройки. Впоследствии стены будут отделаны сайдингом под дерево.

Это почти готовый сарай с двускатной крышей. Осталась отделка стен
Обшивка, кстати, не обязательно должна быть из фанеры или ОСП. Можно вагонку или доску крепить сразу а стойки. Но тогда при сборке каркаса нужно ставить укосы: без жесткости плитного материала постройка будет хлипкой. Если укосы не ставить, качнуть можно рукой.

Такие раскосы придадут достаточную жесткость стенам каркасного сарая
После установки раскосов можно набивать доску, вагонку, блок-хаус, имитацию бруса, сайдинг — выбор за вами.

Каркасный сарай обшивается доской
Похожие каркасные сараи можно сделать из профильной трубы. Для обвязки и угловых стоек достаточно сечения 60*60 мм или 60*40 мм, для промежуточных и того меньше — 20*40 будет нормально. Только для крепления наружной обшивки нужно будет собирать и крепить обрешетку. Подробнее о строительстве сарая из труб и металлопрофиля читайте тут.
Для тех, кого волнует внешний вид строения, несколько идей о том, как сделать сарай красивым в видео-формате.
О планировании участка и основах ландшафтного дизайна можно прочесть тут.
Видео о строительстве сараев из дерева
Сарай получился красивый, но недешевый. Зато приличный по размерам, крепкий и по внешнему виду не отличается от дома — вписывается в композицию. Все показано/расписано подробно, есть одно нарушение: гидроизоляция под металлочерепицу уложена вертикально. Даже при хорошем склеивании полос рано или поздно вода сделает себе дорожку. В остальном — все грамотно.
В этом случае сарай своими руками построен на самом дешевом, наверное, фундаменте: в старые покрышки залит бетон. На этих «столбиках» и стоит каркас. Естественно, выставлять их нужно на ровную надежную поверхность и сами они должны быть в одном уровне. По прочности такон основание не уступит лучшим бетонным блокам, а может еще и превзойдет их. Выступающие из-под строения покрышки, можно закрыть, сделав ступеньку и расставив впоследствии на ней цветы или используя под другие нужды. Еще практичней получится.
Еще одно видео с пошаговой иллюстрацией строительства каркасного сарая из бруса.
Чертежи с размерами
Несколько чертежей, которые помогут вам сориентироваться с габаритами постройки. При необходимости корректируйте под свой участок или потребности.

Сарай с односкатной крышей — чертеж со схемой расположения стоек

Сарай на три отделений под односкатной крышей. Пунктиром указаны места установки стоек (и опор под них)

Конструкция сарая с указанием всех требуемых элементов

Двускатная крыша на сарае из металлопрофиля

Квадратный сарай — размеры

Сарай с ломаной крышей